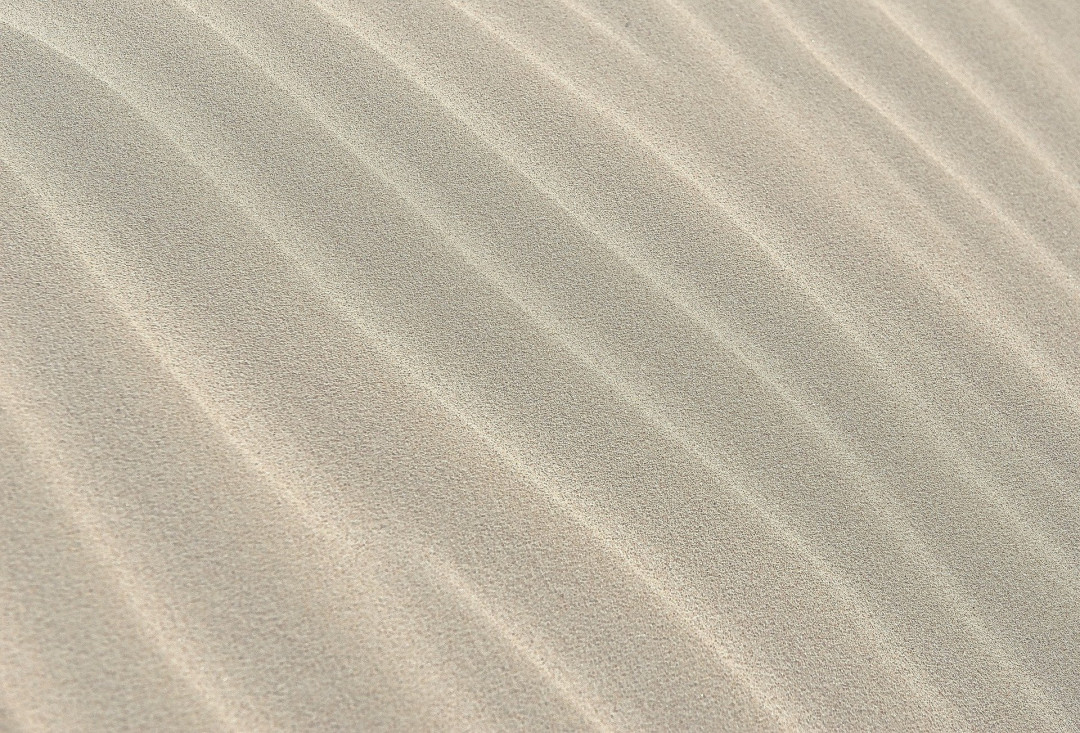
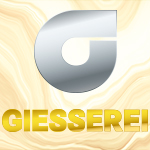
Kürzlich ist in der Gießerei Stolle eine hochmoderne mechanische Sandrückgewinnungsanlage in Betrieb gegangen. Die Projektkosten betrugen eine dreiviertel Million Euro. Hersteller der Wöhr-Regenerierung ist die AAGM Aalener Gießereimaschinen GmbH aus Bopfingen. Über die neue Sandregenerierung und weitere Anlagenpläne der Gießerei Stolle sprach die GIESSEREI mit Gießereileiter Florian Lorenz und AAGM-Geschäftsführer Peter Wagner.
Sie haben eine neue mechanische Sandregenerierungsanlage für Furanharzsand in der Gießerei Stolle installiert. Welche Eckdaten hat sie?
Wagner: Der Durchsatz der Sandregenerierungsanlage liegt bei 10 Tonnen pro Stunde. Herzstück ist ein Wöhr-Fluidbettkühlersichter. Dieser entstaubt den Sand und kühlt ihn von 150 auf 25 Grad herunter. Der Staubanteil im fertigen Regenerat liegt in der Fraktion unter 0,09 Millimetern kleiner 0,25 Prozent, wodurch der Formstoff eine sehr gute Gasdurchlässigkeit bekommt und gleichzeitig Bindemittel am Mischer eingespart wird.
Wie funktioniert Ihre Anlage?
Wagner: Am Beginn der Anlage stehen zwei Silos mit Heißgut sowie ein Neusandsilo. Diese speisen über ein Trennsieb den Fluidbettkühlersichter mit einem einstellbaren Gemisch aus Regenerat und Neusand – derzeit 95 Prozent Regenerat und 5 Prozent Neusand. Das Trennsieb sondert Grobanteile aus dem Regenerat ab. Bevor das Sandgemisch in den Sichter gelangt, scheidet eine Magnettrommel zuverlässig magnetische Metallanteile ab. Nichtmagnetische, schwere Feinteile wie Chromitsand lagern sich am Boden des Kühlers ab. Diese werden automatisch in Intervallen durch eine spezielle Einheit ausgetragen. Der Fluidbettkühler ist modular aufgebaut. Die einzelnen Kühlsegmente können flexibel von den Kühlaggregaten versorgt werden. Dadurch lässt sich die beim Kunden verfügbare Kühltechnik möglichst effizient einbinden. Wir können flexibel auf die Kundenwünsche eingehen. Ein Wöhr-DUO-Sandförderer übernimmt die Verteilung des fertigen Sandes in der Gießerei. Bei Stolle kommt an den Mischern ausschließlich ein vorgemischtes Regenerat-/Neusand-Gemisch zum Einsatz. Derzeit werden nur 5 Prozent Neusand zugesetzt. Eine höhere Zugabe von Neusand ist aufgrund der hohen Regeneratqualität nicht erforderlich. Damit entspricht die Zugabemenge an Neusand den Sandverlusten im Prozess-umlauf innerhalb der Gießerei. Sand aus der Produktion muss nicht mehr auf die Deponie gefahren werden, um ein Überlaufen des Systems zu verhindern. Entsorgt werden lediglich die von den Filtern aufgefangenen Stäube.
Sie reden von einer flexiblen Kühlung des Sandes. Bitte erläutern Sie das näher?
Wagner: Wir haben eine komplett neue Kühlanlage in geschlossener wartungsarmer Ausführung geliefert. Es handelt sich um ein zweistufiges Kühlsystem mit einem passiven Freikühler und einem aktiven Kühlkompressor. Durch geeignete Beschaltung der Kühlregister wird möglichst viel Energie über den Freikühler abgeführt. Nur die letzten Kühlregister werden vom Kühlkompressor versorgt. Und dies auch nur dann, wenn zu hohe Außentemperaturen dem Freikühler Grenzen setzen. So können wir den Bedarf an Kompressorleistung deutlich reduzieren.
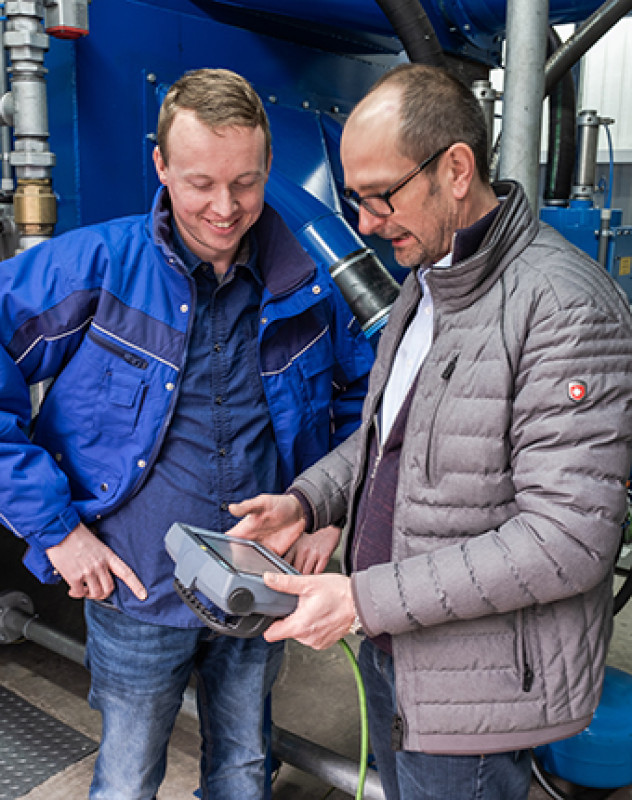
Baut Wöhr auch thermische Regenerierungsanlagen?
Wagner: Nein, wir vertreiben ausschließlich mechanische Rückgewinnungsanlagen. Thermischen Anlagen sind aktuell natürlich ein Thema. Vor allem vor dem Hintergrund fehlender Deponiekapazitäten. Unser Fokus liegt auf einer hocheffizienten mechanischen Regenerierung, die eine gleichbleibend hohe Sandqualität erzielt. Im Zusammenspiel mit unseren leistungsfähigen Wöhr-Mischern, die durch geringe Binderzugabemengen überzeugen, lässt sich der Einsatz von Neusand merklich reduzieren, was gleichzeitig die Entsorgungskosten für Staub und Formsand erheblich verringert.
Herr Lorenz, beim Thema Stäube sind Sie weiter von der Deponieentsorgung abhängig. Und die Deponiekosten sind in den vergangenen Jahren um das 5 bis 10-Fache angestiegen...
Lorenz: Wir arbeiten daran, auch hier unabhängiger zu werden. Erst vor wenigen Wochen haben wir das Genehmigungsverfahren für eine Staubeinblasanlage eingeleitet. Wir wollen unsere Stäube in den Kupolofen einblasen lassen. Die Firma Velco aus Velbert hat eine Anlage entwickelt, die uns überzeugt hat.
Sie wollen tatsächlich Regeneratreste, also Stäube, in den Ofen einblasen?
Wagner: Bei der Regenerierung besteht der Staub hauptsächlich aus Binderhüllen, das ist brennbares Material, ein Energieträger.
Lorentz: Wir wollen dort zum einen den Brennwert nutzen und zum anderen den Quarzstaub in Schlacke umwandeln. Und Schlacke kann man sehr gut entsorgen.
Stichwort Industrie 4.0. Was bietet die neue Sandregenierung da?
Wagner: Die gesamte Anlage ist vernetzt und damit fernwartungsfähig, das ist man der Zeit schuldig. Dabei konzentrieren wir uns zunächst auf die Funktionalität der Anlage. Es geht aktuell vorrangig um Prozesssicherheit in der Produktion, damit die Anlage möglichst störungsfrei läuft. Durch einen Fernzugriff auf die vernetzte Anlage ist eine Fernwartung möglich. Durch langfristig mitgeschriebene Log-Dateien lässt sich durch Analyse der Prozessparameter die Funktionalität der Anlage systematisch verbessern.
Inwieweit nutzen Sie diese Daten, Herr Lorenz?
Lorenz: Industrie 4.0 wird immer wichtiger – auch bei uns. Bei dieser Wöhr-Anlage erhalten wir viele Daten, die zunächst einmal gesammelt werden. Wir loggen viel und beobachten, was die Log-Dateien ausspucken. Als Beispiel: Abhängig davon, welche Temperaturverläufe festgestellt werden, möchten wir entscheiden, ob wir über eine Energierückgewinnung oder -speicherung nachdenken können. Wir machen das bei vielen anderen Produktionsanlagen, die wir überwachen, ähnlich. Angefangen beim Kompressor, der uns mittlerweile 70 Grad warmes Wasser liefert. Bei der Sandregenerierung kommt es darauf an, was die Messungen ergeben. Das ist ein Zukunftsprojekt, das wir bisher nicht mitprojektiert haben.
Herr Lorenz, Herr Wagner, vielen Dank für das Gespräch!
Schlagworte
GießereiIndustrie 4.0ProduktionSicherheit