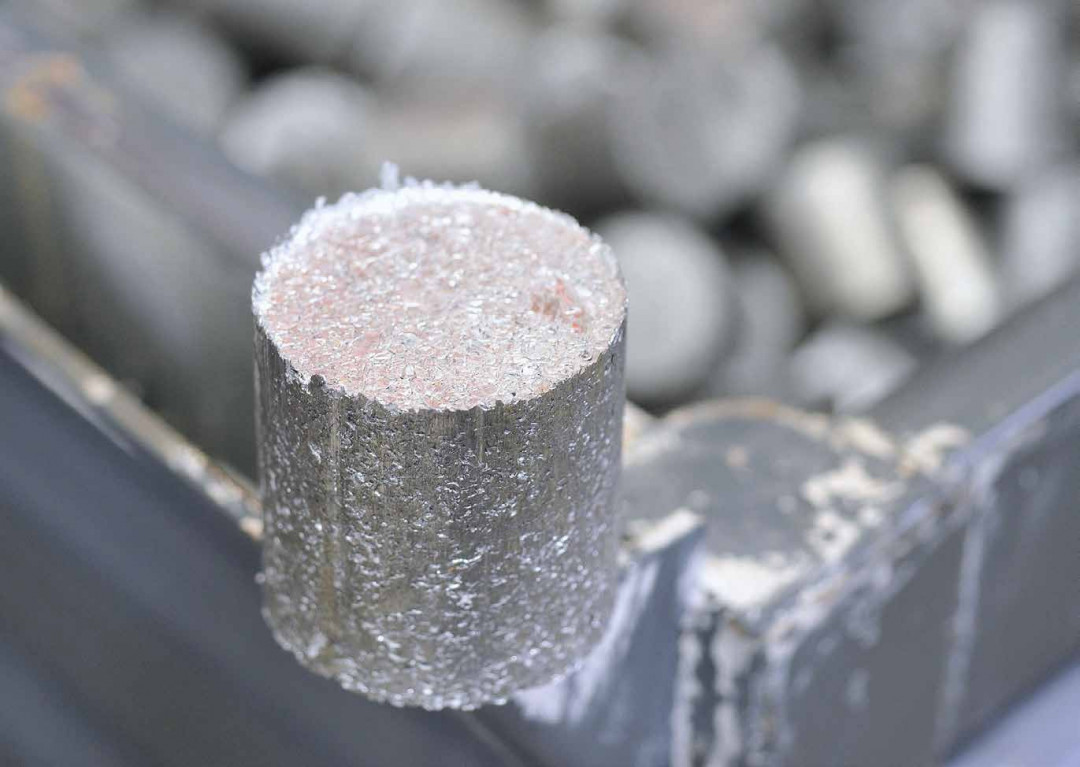
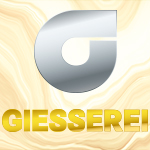
Welcher metallverarbeitende Betrieb will das schon: nasse Späne, die verschmutzte Arbeits- und Containerstellplätze mit sich bringen und einen hohen Aufwand für die Späneentsorgung mit viel Staplerverkehr verursachen. Die zudem einen Austrag von viel Kühlschmierstoff (KSS) sowie geringe Schrotterlöse mit sich bringen. Die Lösung: Anfallende Metallspäne vom KSS trennen. Bleibt die Frage: wie? Brikettieren und Zentrifugieren sind die primär dafür verwendeten Verfahren. Doch was sind die jeweiligen Voraussetzungen, Herausforderungen und Vorteile der beiden Möglichkeiten? Wie hoch die Kosten?
VON PETER KLINGAUF
Diesen Fragen stellte sich Ruf Maschinenbau, Zaisertshofen, in einem Whitepaper. Darin geht der Entwickler und Hersteller von innovativen Brikettieranlagen für Holz, Metall und anderen Reststoffen detailliert auf Vorteile und Schwächen beider Verfahren ein, sodass sich Interessenten einen guten Überblick verschaffen können (Bild 1). Dieser Fachbeitrag fasst die wichtigsten Punkte zusammen.
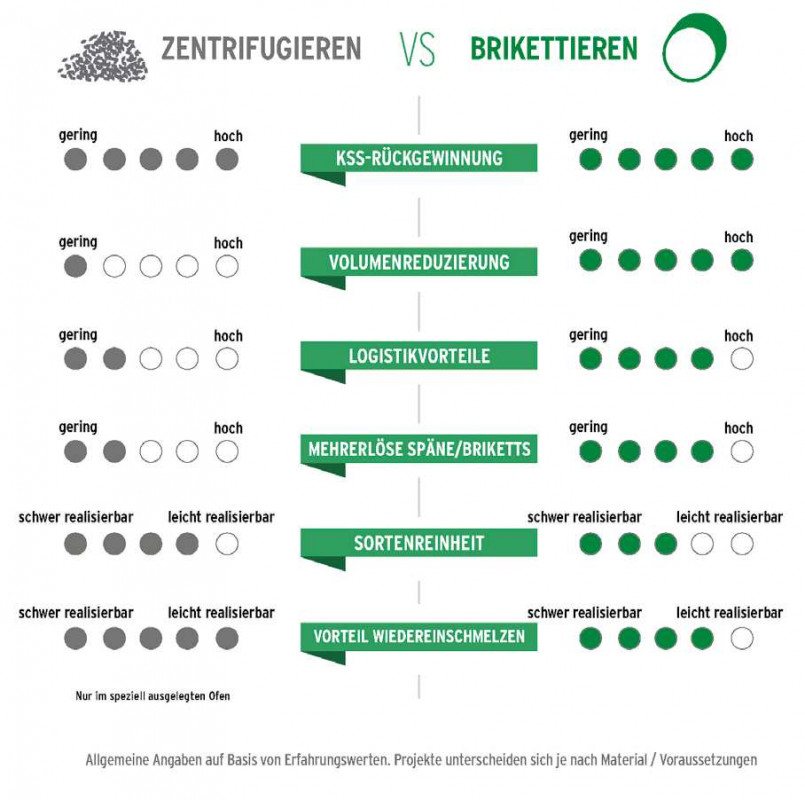
Wie funktionieren Zentrifugen, wie Brikettieranlagen? Metallspäne sind in jeglicher Form ein wertvoller Rohstoff, den es auf die ein oder andere Weise zu erschließen gilt. Beim Zentrifugieren werden die Späne in einer rotierenden Trommel hohen Zentrifugalkräften ausgesetzt, wodurch die Trennung von Spänen und Kühlschmierstoff (KSS – also Öl oder Emulsion) erfolgt. Man unterscheidet Durchlauf-, Schubboden und Chargenzentrifugen. Die ersten beiden sind automatisierte Anlagen, bei denen entweder das Material am Trommelrand von kontinuierlich nachfolgenden Spänen nach oben gedrückt wird oder der Materialaustrag durch Hubbewegungen des Bodens erfolgt. Chargenzentrifugen werden zumeist manuell mit Spänen beschickt.
Beim Brikettieren werden die Späne durch Verpressen verdichtet. Dafür werden im Metallbereich vor allem vollautomatisch betriebene, hydraulische Brikettierpressen genutzt (Bild 2).
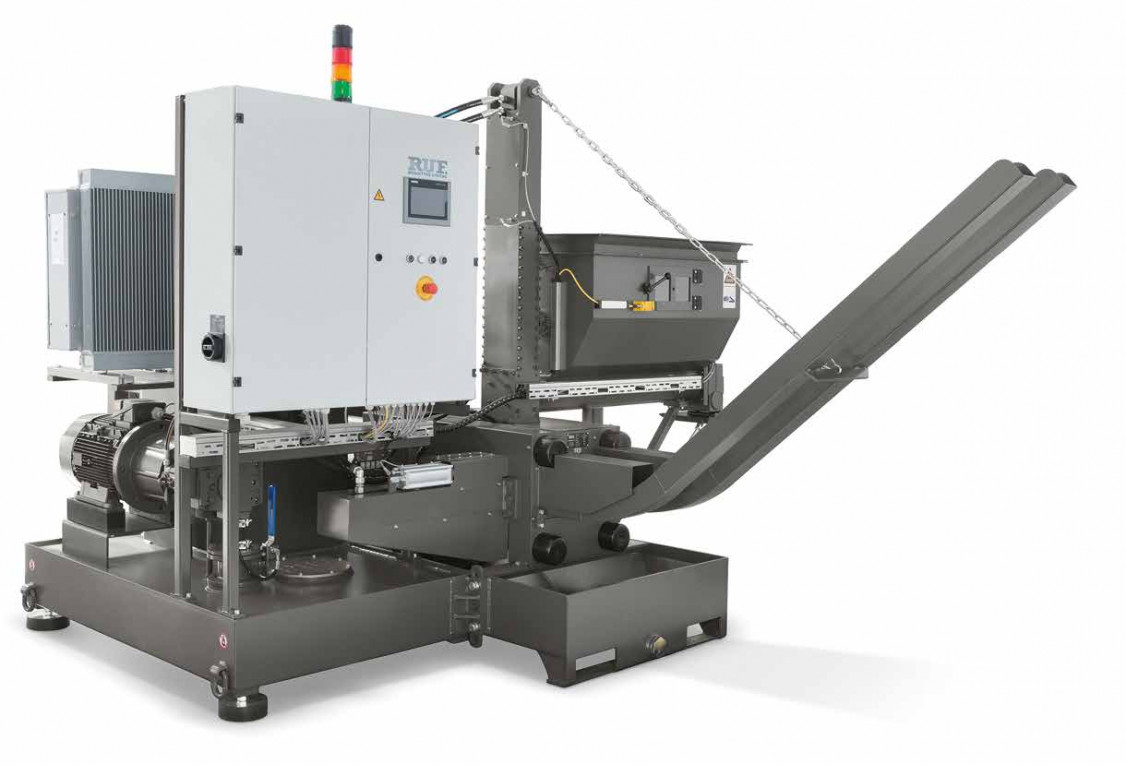
Der Effekt: Das Volumen wird deutlich reduziert – bei Aluminium liegt der Wert typischerweise bei 1:10 – und der KSS (Öl oder Emulsion) tritt aus. Der Anwender erhält ein kompaktes, dichtes Spänebrikett sowie den zurückgewonnenen KSS, den er dem Produktionsprozess wieder zuführen kann, was insbesondere bei Schneidölen besonders lukrativ ist. Die Menge der beim Brikettieren zurückgewonnenen Kühlschmierstoffe entspricht in etwa der von automatisierten Qualitätszentrifugen. Manuelle Chargenzentrifugen erreichen nur geringere Entwässerungsgrade (Bild 3).
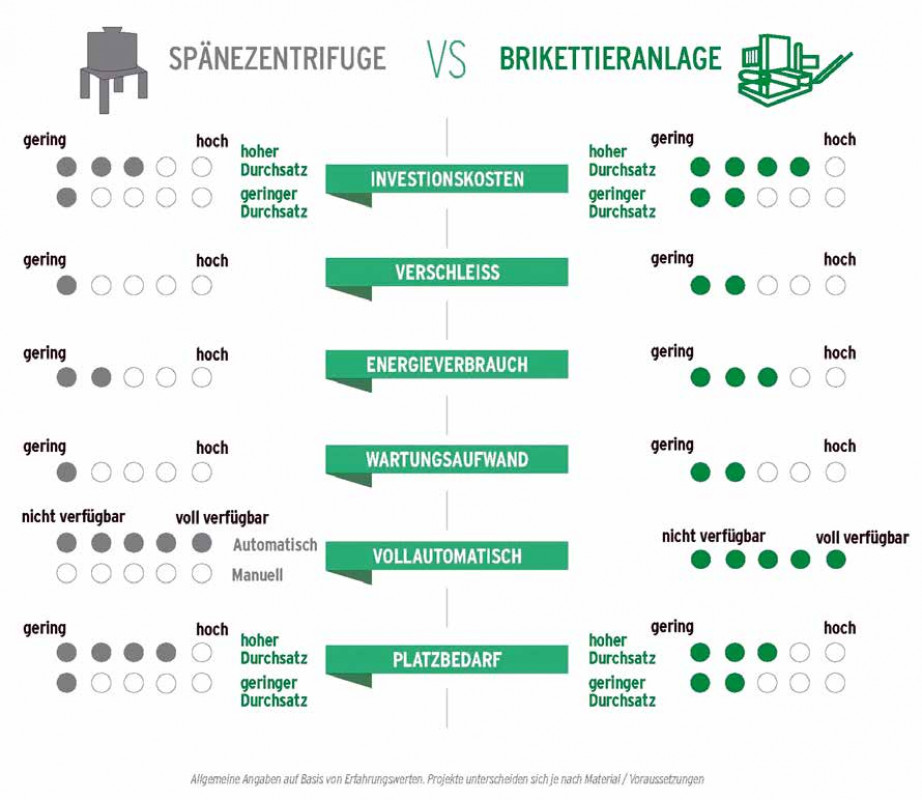
Mehrerlöse bei der Spänevermarktung
Neben der Rückgewinnung des KSS ist die verlässliche, reduzierte Restfeuchte der zentrifugierten Späne bzw. Briketts ein weiterer wichtiger Pluspunkt der Spänebehandlung. Damit ist eine definierte Schrottqualität gegeben, was leidige Diskussionen mit dem Abnehmer zum Wassergehalt erspart.
Übliche Restfeuchten liegen bei Aluminiumbriketts zwischen zwei und sechs Prozent, bei Stahlbriketts zwischen zwei und vier Prozent. Schubbodenzentrifugen und Brikettierpressen mit sehr hoher Presskraft erreichen tendenziell die niedrigeren Werte, in Einzelfällen auch darunter (abhängig von der Qualität der Späne).
Die durch Pressen erzeugten Briketts haben aber noch weitere Vorteile. Gegenüber den beim Zentrifugieren anfallenden trockenen Spänen zeichnen sich Briketts auch durch Volumenreduktion aus. Sie können wie Stückgut behandelt und kostengünstig transportiert werden, auch in Komplettladungen. Dadurch entfallen beispielsweise teure Containertransporte via Absetz- oder Abrollerkipper.
Ein zusätzlicher Pluspunkt: Mit Briketts können die Erzeuger spezialisierte Großhändler oder Schmelzwerke anfragen, auch wenn diese weiter entfernt sind. So lassen sich Verwertungswege optimieren bzw. die Handelsketten verkürzen – was die Verwertungserlöse steigen lässt. Das macht sich insbesondere bei sortenreinen Aluminiumbriketts bemerkbar. Nicht selten werden hierfür hohe zwei-, sogar dreistellige Euro-Beträge pro Tonne als Mehrerlös erzielt. Das bedeutet: Die Investition in eine Brikettieranlage amortisiert sich in vielen Fällen schon in ein bis zwei Jahren.
Eine Pauschalaussage für den Mehrerlös von Briketts zu Spänen ist jedoch nicht möglich. Denn er hängt von verschiedenen Faktoren ab: der Menge an Spänen oder Briketts, den aktuellen Marktpreisen, der Sortenreinheit und Legierung des Schrotts, der jeweiligen definierten Schrottqualität und den Einsparungen beim Transport.
Einen weiteren Vorteil weist das Brikettieren beim Behandeln von Schleifschlämmen auf. Denn beim Zentrifugieren der feinen Schleifspäne kann es zu Funkenbildung kommen, sodass – je nach Material – Brandgefahr droht. Beim Brikettieren besteht diese Gefahr nicht. Schließlich wird durch die Verdichtung die mögliche reaktive Oberfl äche der Späne extrem verkleinert. Außerdem wichtig: Beim Brikettieren entfällt die Staubbelästigung, was zu verbessertem Arbeits- und Umweltschutz beiträgt.
Einzig in zwei Fällen ist eine Brikettierung nicht direkt zu empfehlen. Zum einen, wenn Spänegemische mit Nichteisen- und Eisen-Metallen vorliegen. Dies schließt eine hochwertige Vermarktung der Briketts aus. Zum anderen gibt es wenige, sehr spezielle Schmelzverfahren, die auf lose Späne angewiesen sind.
Was kosten die Anlagen?
Das Investitionsvolumen einer Spänebehandlungsanlage hängt wesentlich vom geforderten Durchsatz, dem gewünschten Automatisierungsgrad sowie den notwendigen Peripheriegeräten der Anlage ab. Deshalb lassen sich die Beschaffungskosten für Zentrifugen und Brikettieranlagen nur dann vergleichen, wenn die genauen Voraussetzungen bekannt sind. Tabelle 1 zeigt den Vergleich an einem Projektbeispiel.
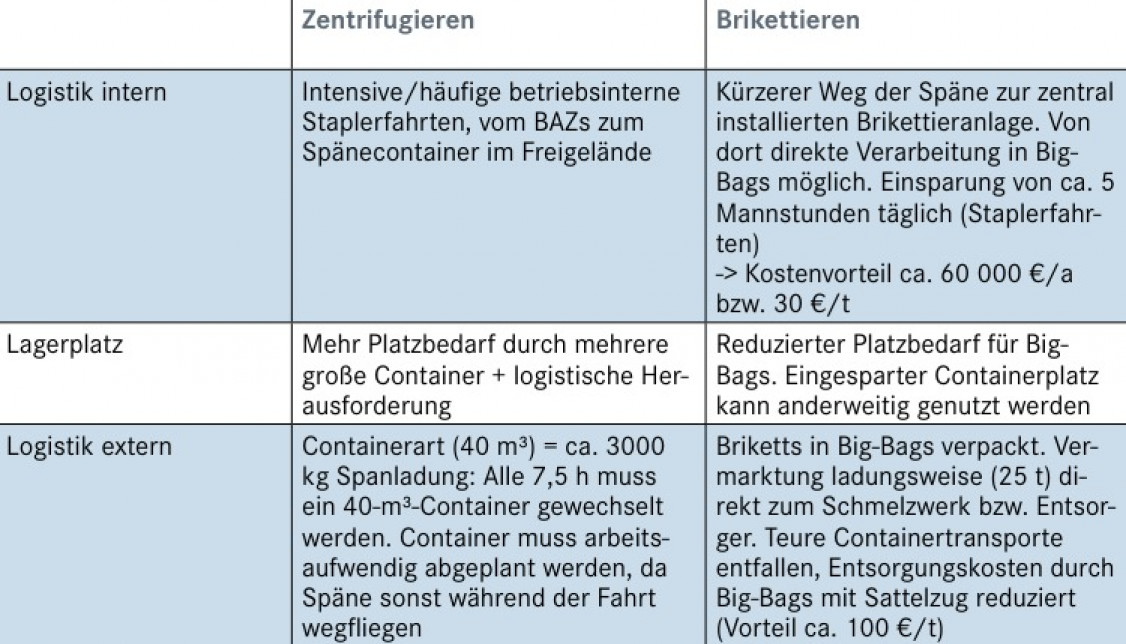
In eine Beurteilung müssen neben der Erstinvestition die laufenden Kosten (pro Tonne Späne) einfließen. Dies sind Strombedarf, Bedien- und Wartungszeiten sowie Wartungskosten. Zentrifugen haben in der Regel einen niedrigeren Stromverbrauch, laufen aber üblicherweise durch, während Pressen nur dann in Betrieb sind, wenn ihnen Späne zugeführt werden. Der Zeitaufwand für Wartung und Bedienung ist bei beiden Systemen sehr niedrig. Auch bei den Wartungskosten schenken sich Zentrifugen und Brikettieranlagen nicht viel: Bei der Spänezentrifuge ist eine jährliche UVV-Prüfung notwendig, die alle drei Jahre in zerlegtem Zustand durchgeführt werden muss. Neben dem Stillstand des Systems verursacht die Prüfung an sich weitere Kosten. Demgegenüber steht bei der Brikettieranlage der Aufwand für den Tausch von Hydraulikschläuchen, Dichtungen, Hydrauliköl und Filter.
Vor der Kaufentscheidung sollten auf jeden Fall die Gesamtkosten dem entstehenden Nutzen gegenübergestellt werden. Hierbei schlagen neben der Wiederverwendung der Kühlschmierstoff e auch der Mehrerlös der Briketts und die gesamten Logistikvorteile zu Buche. Unverzichtbar ist eine qualifizierte Beratung durch Fachleute, wie sie RUF Maschinenbau beschäftigt. Sie stellen ihr umfangreiches Know-how in der Spänebehandlung gerne zur Verfügung, um je nach Material, der geforderten Durchsatzleistung und den Produktionsbedingungen ein maßgeschneidertes Brikettiersystem zu projektieren. Mit mehr als 6000 verkauften Brikettpressen in über 100 Ländern gilt RUF als Weltmarktführer für hydraulische Brikettiermaschinen. So schaff t z. B. die kleinste Maschine RUF Formica mit einer Motorleistung von 2,2 kW einen Durchsatz von bis zu 100 kg/h (je nach Material und Spanart). Die mit 90 kW größte Anlage (RUF 90) erreicht bis zu 2500 kg/h für Aluminium, für Guss bis 3000 kg/h und für Kupferwerkstoffe bis 5000 kg/h.
Checkliste für den Beschaffungsprozess
Metallspäne als wertvoller Rohstoff (Bild 4): Vor einer Investition in eine Spänebehandlung ist gründlich zu prüfen, welche Potenziale diese bietet. Faktoren wie die KSS-Rückgewinnung, Volumenreduzierung, Reduzierung des Logistikaufwands (intern & extern) und des Platzbedarfs, Schrottmehrerlöse sowie Produktionsbedingungen haben einen großen Einfl uss auf das Kosten-Nutzen-Verhältnis. Daher lohnt es sich, auf Basis folgender Fragen eine Entscheidung zu treffen:
- Wie hoch ist das Budget? Welcher Automatisierungsgrad wird angestrebt und welcher Personalaufwand ist akzeptabel?
- Welche Spänemengen und wie viele Sorten sollen verarbeitet werden? Werden sie zusammen entsorgt?
- Ist eine dezentrale oder zentrale Behandlung der Späne vorgesehen?
- Wie viel Platz ist in der Produktion bzw. vor Ort vorhanden?
- Soll Platz für Spänecontainer und/oder Späneloren eingespart werden? Sollen gleichzeitig KSS-Tropfverluste beseitigt und eine Umweltgefährdung verhindert werden?
- Sollen der Staplerverkehr und Lkw-Fahrten reduziert werden?
- Ist die Restfeuchte der Späne bzw. der Briketts beim Verwerter oder im Schmelzprozess ein Thema? Welche maximalen Restfeuchtegehalte werden nach der Behandlung akzeptiert? Im Fall von Schmelzwerken: Ist der Schmelzprozess geeignet für lose Späne und Briketts oder nicht?
- Akzeptiert der Entsorger Briketts? Wenn ja, wie viel mehr zahlt er dafür im Vergleich zu Spänen? Können alternative Abnehmer angefragt werden?
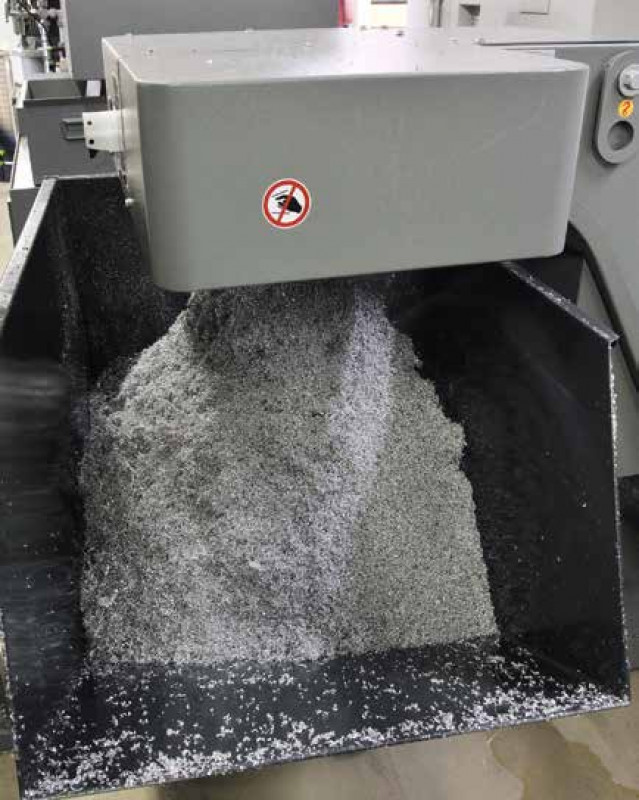
Schlagworte
AluminiumAutomatisierungEisenGussKupferLogistikMaschinenbauProduktionStahlWerkstoffe