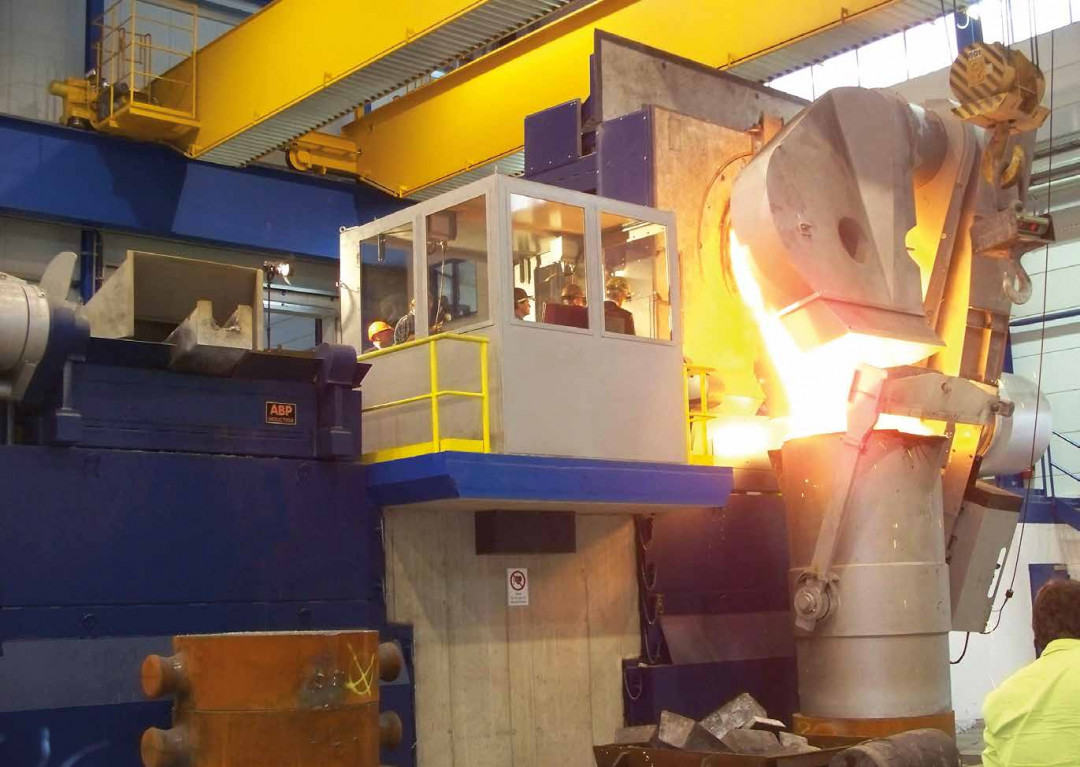
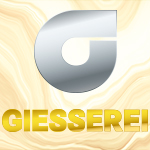
Die metallverarbeitende Industrie ist weltweit einer der größten industriellen Verursacher von CO2-Emissionen. Eine alternative Lösung zur CO2-Reduzierung ist die Induktion für Erwärmungsprozesse unter Verwendung von Ökostrom. Die ABP Induction Systems GmbH geht nun einen Schritt weiter und nutzt die Technologie auch zum Speichern von Energie.
VON MARCO RISCHE
Der Prozess der induktiven Erwärmung ist dynamisch, leicht steuerbar und bei Verwendung von grünem Strom nahezu CO2-neutral. Aufgrund des direkten Energieeintrags in das Material stellt er eine gute Ergänzung oder sogar ein Ersatz für die Erwärmung durch bisher etablierte, CO2-intensive Energieträger dar. Wenn man das Konzept weiterentwickelt, gelangt man direkt zur aktuellen Diskussion über den Einsatz von Energiespeichern. ABP denkt das System Energiespeicher weiter und setzt es in Beziehung zur Induktionsofentechnologie. In der Umsetzung führt dies zu einer messbaren Reduktion von CO2-Emissionen im Prozess und zu einer optimalen Nutzung verfügbarer Energieressourcen am Strommarkt.
Mit vollelektrischer Erwärmung auf dem Weg zur Klimaneutralität
Die großen geopolitischen und gesellschaftlichen Verwerfungen in den letzten Jahren haben die metallverarbeitende Industrie als energiepreissensible und vergleichsweise klimaschädliche Industrie stark belastet. Auch wenn die Industrie von den weiteren Entwicklungen in diesen Bereichen und vielfach auch von politischen Entscheidungen abhängig ist, so kann sie doch auch selbst aktiv werden, um sich spürbar der Preissensibilität am Energiemarkt und der Erzeugung von klimaschädlichem CO2 zu entziehen: Dekarbonisierung ist das Stichwort, mit dem ABP Induction hier seit der GIFA 2023 agiert. ABP hat den Paradigmenwechsel zur CO2-Neutralität erkannt und sich dem durch seine Kampagne „Your Partner on the way to Zero Emission“ gestellt.
Um dem Anspruch der Dekarbonisierung gerecht zu werden, sieht ABP großes Potenzial im Ersatz der fossilen Brennstoffe durch moderne Induktionsofentechnologie zur ökologischen, ökonomischen und technischen Unabhängigkeit. Anwender leisten so einen signifikanten Beitrag zur Umsetzung der Ziele für die Dekarbonisierung. Begibt sich die metallverarbeitende Industrie auf den Weg zum grundlegenden Wandel, so sind mehrere Prämissen bei der Umstellung zu berücksichtigen. Es geht darum:
- eine Reduktion der CO2-Emisisonen zur Erreichung der Klimaziele umzusetzen,
- eine Aufrechterhaltung der Produktion von Gussteilen zu international wettbewerbsfähigen Preisen zu gewährleisten,
- eine Flexibilisierung des Produktspektrums zur Erhöhung der Wettbewerbsfähigkeit zu erreichen.
Damit steht die Industrie naturgemäß vor gewissen Herausforderungen bei der Umstellung. Im Kern geht es für viele klassische, gewachsene Betriebe zunächst einmal um die metallurgische Umstellung von Kupolofen- auf Induktionsofeneisen. Im Fokus stehen ebenfalls die bereits erwähnten Kosten der elektrischen Energie im Vergleich zu konventionellen Energieträgern. Auch Planung und Kosten für die Neuinvestition sollten berücksichtigt werden. Letztlich hantieren die Akteure mit einem veränderten Materialfluss und Platzbedarf für die Umstellung.
Aufseiten des Energiebedarfs der metallverarbeitenden Industrie spielen mehrere energiemarktpolitische Faktoren eine Rolle. Im Fokus steht der Preis, dann aber auch der Energiemix, und schließlich der Zeitpunkt der Inanspruchnahme der elektrischen Energie. Alle drei Faktoren hängen mit den Rahmenbedingungen des Energiemarktes, hier insbesondere des Strommarktes für die industrielle Nutzung, zusammen. Auf der Angebotsseite muss grundsätzlich gewährleistet sein, dass so viel Energie zur Verfügung gestellt wird, wie verbraucht wird. Das hat damit zu tun, dass auch Lastspitzen in der Abnahme abgedeckt sein müssen, entsprechende Kapazitäten oder Reserven sind also obligatorisch. Die Menge der Abnahme schwankt je nach Tages- und Nachtzeit, was allerdings kein Spezifikum der metallverarbeitenden Industrie ist, sondern des kompletten Marktes insgesamt. Ausgleichsmöglichkeiten bei potenziellen Unterversorgungsszenarien aus der eigenen Stromerzeugung in Deutschland können Stromimporte sein, oder auch die Speicherung überschüssiger Energie bei Schwachlastzeiten und Rückführung bei Hochlastzeiten, oder bei schwankender regenerativer Erzeugung. Denn diese ist verschiedenen geografischen, topografischen und klimatischen Verhältnissen ausgesetzt.
Beitrag der Erneuerbaren Energien zum Brutto-Endenergieverbrauch in Deutschland
Da die regenerative Erzeugung einen immer größeren Stellenwert einnimmt, wird sie auch zu einer zu berücksichtigenden Komponente bei der Energieverbrauch-Planung. Im Jahr 2023 wurden nach aktuellen Schätzungen des Umweltbundesamtes [1] gemäß den Berechnungsvorschriften der EU-Richtlinie zur Förderung Erneuerbarer Energien 22 % des deutschen Brutto-Endenergieverbrauchs aus Erneuerbaren Energien gedeckt (Bild 1).
![© STATISTA [2] © STATISTA [2]](/storage/media_foundry/images/4778/conversions/b1-full.jpg)
Dies entspricht einem Anstieg um 1,4 % im Vergleich zum Vorjahr. Im Jahr 2020 hat Deutschland sein Ziel von 18 % gemäß der EU-Richtlinie übertroffen und einen Anteil von 19,1 % erreicht. Um die neuen, als ambitioniert zu bezeichnenden Klimaziele der EU zu erreichen, wird ein weiteres Wachstum der Erneuerbaren Energien notwendig sein. Insbesondere der Windenergiesektor bietet Potenziale. Andere Sektoren wie die Biomasse scheinen hingegen ihr Maximum erreicht zu haben.
In Bezug auf die industrielle Nutzung von Strom für die Metallverarbeitung und andere Industrien zeigt sich, dass der Anteil Erneuerbarer Energien im Stromsektor von 41,5 % im Jahr 2021 auf 46,0 % im Jahr 2022 deutlich gestiegen ist. Im Jahr 2022 wurden insgesamt 254,2 Mrd. kWh Strom aus erneuerbaren Energieträgern erzeugt, was über 17 Mrd. kWh mehr als im Vorjahr (+ 7 %) entspricht [3]. Der Blick auf die Verbrauchsseite zeigt: Im Jahr 2023 wurden insgesamt 513 Mrd. kWh aus erneuerbaren Energieträgern genutzt. Etwa 53 % dieser Energiemenge stammten aus erneuerbaren Energiequellen für die Stromproduktion (Bild 2).
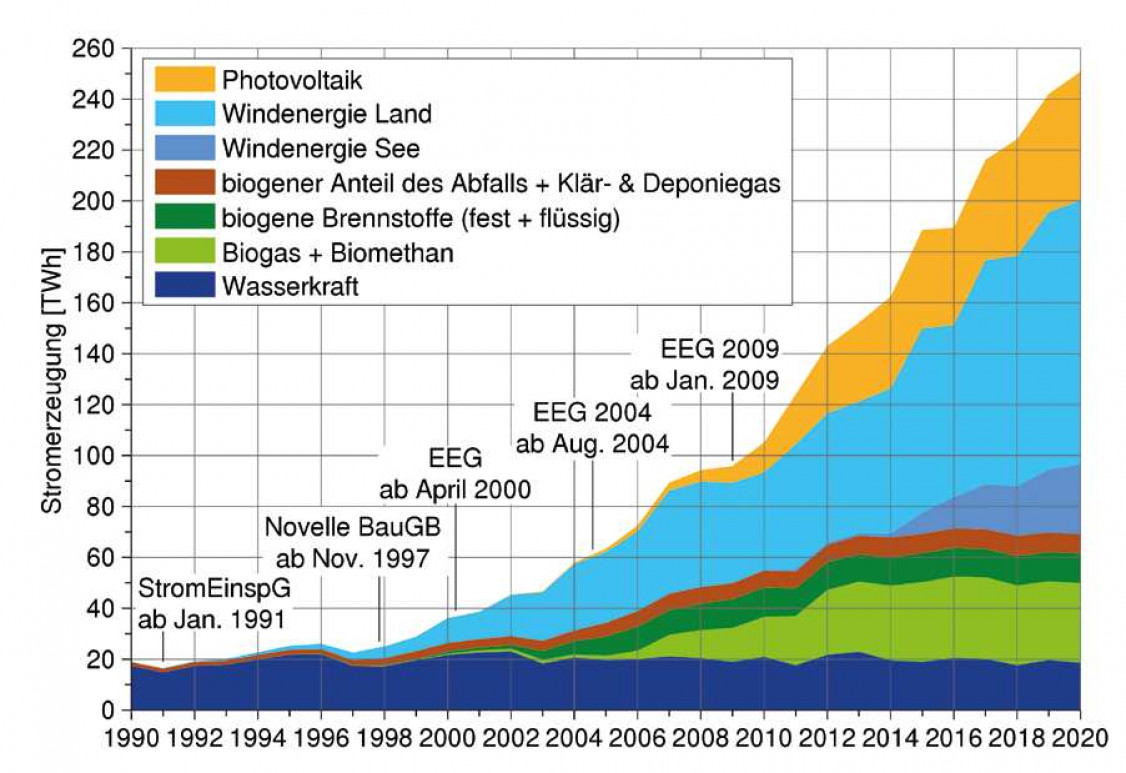
Biomasse ist aufgrund ihrer vielfältigen Nutzungsmöglichkeiten in allen Sektoren der wichtigste Akteur im Spektrum der erneuerbaren Energieträger. Sie wird in Form von festen Brennstoffen zum Heizen, Biokraftstoffen im Verkehr oder Biogas zur Stromerzeugung genutzt und macht knapp 50 % der Bereitstellung von erneuerbarer Endenergie aus. An zweiter Stelle folgt die Windenergie mit einem Anteil von 28 %. Die Nutzung von Sonnenenergie in Photovoltaik- und Solarthermieanlagen trägt weitere 14 % bei. Wasserkraft und Geothermie sind mit jeweils weitere 8 % vertreten. Hierbei sind räumliche Verteilungen und Besonderheiten zu beachten. Auch Tages- und Jahreszeiten spielen eine relevante Rolle [4].
Die zunehmende Nutzung Erneuerbarer Energien führt dazu, dass fossile Energieträger verdrängt und somit klimaschädliche Treibhausgase vermieden werden können. Im Jahr 2023 konnten laut Umweltbundesamt durch Erneuerbare Energien etwa 250 Mio. t CO2-Äquivalente eingespart werden [4]. Der größte Anteil entfällt auf die Stromerzeugung aus erneuerbaren Quellen (195 Mio. t CO2-Äquivalente, also etwa 78 % der Gesamtmenge). Im Wärmesektor wurden fast 18 % der Treibhausgasemissionen vermieden, das entspricht 44 Mio. t CO2-Äquivalent. Biokraftstoffe haben dabei einen Anteil von etwa 4 %, was etwa 10 Mio. t CO2-Äquivalenten entspricht.
Berechnungen des Umweltbundesamtes zeigen, dass Erneuerbare Energien insbesondere Steinkohle und Erdgas im deutschen Energiemix ersetzen. Der Einsatz Erneuerbarer Energien führt im Bereich der Wärmeversorgung zu Einsparungen von Heizöl und Erdgas. Im Verkehrsbereich werden vor allem Diesel- und Ottokraftstoffe durch Erneuerbare Energien ersetzt.
Stationäre Energiespeicher zur Lastspitzenkappung
Unternehmen haben oft einen stark schwankenden Stromverbrauch, der von Tages- und Jahreszeiten abhängt (Bild 3).
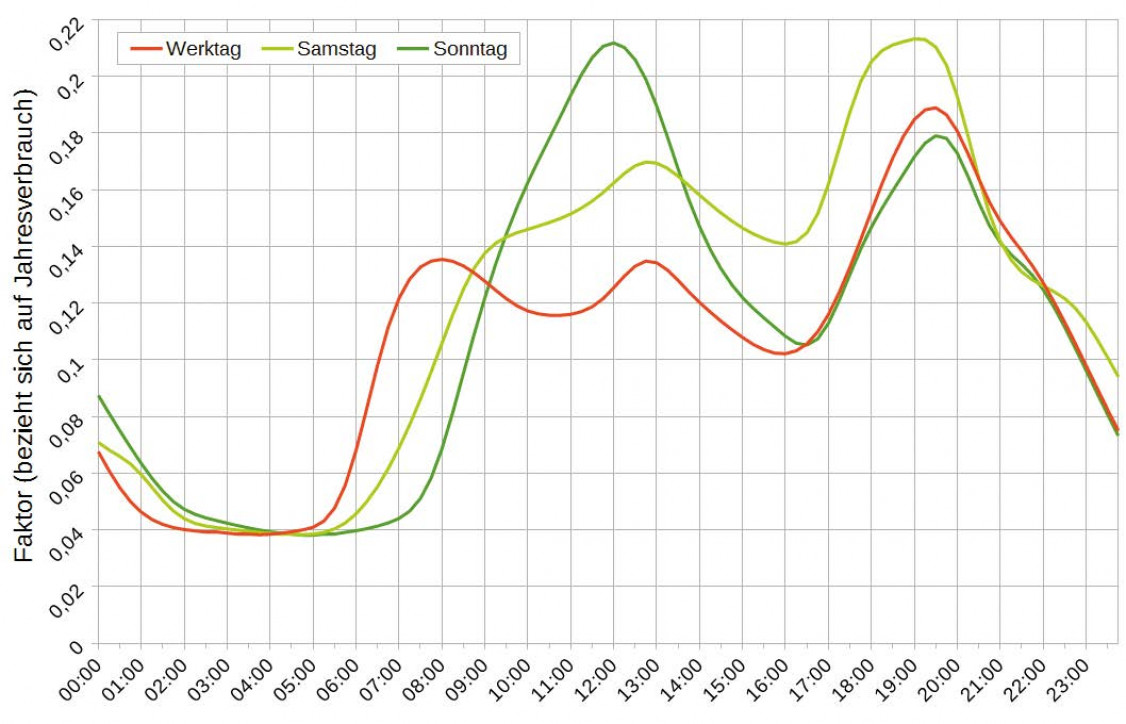
Wenn beispielsweise mehrere Maschinen gleichzeitig hochgefahren werden, wird eine höhere Strommenge benötigt. Diese Höchstbelastung des Stromnetzes wird in der Regel als „Spitzenlast“, „Lastspitze“ oder „Peak“ bezeichnet. Die Abnahme von Energie ist also alles andere als konstant. In Betrieben treten sogenannte Lastspitzen zu bestimmten Zeiten auf. Diese Spitzen schlagen sich in der Stromrechnung nieder, da Stromversorger die Leistung, die nur kurzzeitig abgerufen wird, dauerhaft vorhalten müssen. Die nächste Spitze ist schlecht planbar.
Bei der Berechnung der Stromkosten für Industrieunternehmen werden nicht nur die bezogenen Energiekosten (Arbeitspreis), sondern auch die Kosten für auftretende Lastspitzen (Leistungspreis) berücksichtigt. Dadurch erhöhen sich die Stromtarife für Unternehmen unabhängig von der Häufigkeit oder Dauer der Lastspitzen deutlich. Die Berechnung der Netzentgelte durch den Energieversorger hängt ebenfalls von den Lastspitzen ab. Eine Reduzierung der Lastspitzen führt unmittelbar zu Kosteneinsparungen für das Unternehmen. Es gibt zwei grundlegende Möglichkeiten, Lastspitzen zu vermeiden: Unternehmen können Maschinen zeitversetzt starten oder Produktionsanlagen abschalten. Allerdings stellt dies einen schwerwiegenden Eingriff in oft sensible Fertigungsprozesse dar.
Eine weitere Möglichkeit zur Reduzierung von Energiekosten ist die Vermeidung von Lastspitzen durch Energiespeicher, die als Energielieferant fungieren, wenn der Stromverbrauch im Unternehmen besonders hoch ist. Diese Methodik passt sich optimal an die individuellen Arbeitsabläufe an und greift nicht in sensible Produktionsprozesse ein. Dies kann zum Beispiel durch eine physikalische Lastspitzenkappung (LSK), auch Peak Shaving genannt, oder durch die Lastspitzenkappung mit registriertem Lastgang (RLM) erfolgen. In beiden Fällen wird der Strombezug von Anlagen und Maschinen so gesteuert, dass die benötigte Energie bei Lastspitzen direkt aus dem Speicher und nicht aus dem Netz abgerufen wird. Die Umsetzung kann über einen Batteriespeicher erfolgen, oder - und das ist ein einzigartiges Merkmal für die metallverarbeitende Industrie – über einen Flüssigeisenspeicher im Prozess.
Der Flüssigeisenspeicher als Game-Changer bei der Energiespeicherung
Ein Flüssigeisenspeicher kann die Grundlage für eine innovative Fertigungsstrategie sein, um fossile Brennstoff e zu ersetzen. Dies ermöglicht eine Transformation der Gießerei hin zur Herstellung von umweltfreundlichen Gussteilen zu wettbewerbsfähigen Kosten. Dabei müssen verschiedene Einflussfaktoren berücksichtigt werden, um eine agile Produktionsplanung zu gewährleisten. Ein Kernelement ist der Einsatz einer schnellen, induktiven Schmelzanlage [6] (Bild 4).
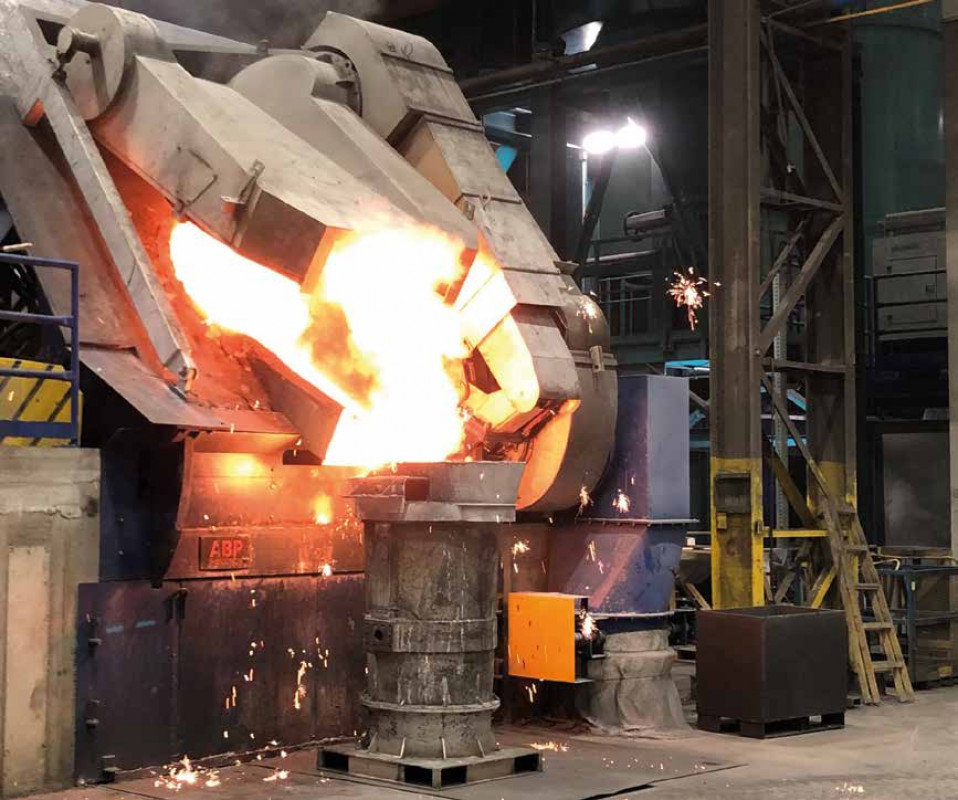
Diese erfordert eine flexible Fertigungsplanung mit angepasstem Personaleinsatz. Es wird angestrebt, ausschließlich 100 % grünen Strom zu nutzen, der durch eine proaktive Einkaufsstrategie zu günstigen Preisen beschafft wird. Dabei werden die dynamischen Vorhersagen der Erzeugerprognosen berücksichtigt. Ein weiterer Faktor ist die Schaffung von energetischen Speichermöglichkeiten, um Schwachlastzeiten zu nutzen.
Ein Flüssigeisenspeicher bietet hierbei grundlegende Vorteile, da die Energie in einem Zustand gespeichert wird, der eine direkte Weiterverarbeitung erlaubt. Das ist gerade für Gießereien interessant, die aktuell noch auf die auslaufende Kupolofen-Technologie setzen und über einen Umstieg auf Induktionsofen-Technologie nachdenken. Aber auch Optimierungen im Bestand von Gießereien, die bereits auf Induktion setzen, haben Potenzial. Es geht um Flexibilität im Prozess: Ziel ist es, Schwankungen in der Energienutzung gegenüber variierenden Energiekosten auszugleichen. Dafür braucht es Speichermöglichkeiten. ABP Induction hat entsprechende Tools zur Simulation und Optimierung entwickelt und setzt außerdem auf die Digitalisierung der Prozesse in der Gießerei, um ein nachhaltiges, sparsames und effektives Handeln zu ermöglichen. Diese Tools werden nachfolgend kurz vorgestellt. Im Fokus stehen dabei die Lösungen Meltshop Designer und OptiCharge.
Erwärmung über Induktion als Prinzip
Wie gerade erwähnt, ist der Ausgangspunkt für die Nutzung eines Flüssigeisenspeichers zur Energiespeicherung die induktive Erwärmung über elektrische Energie in Verbindung mit grünem Strom. Dabei wird die für den Prozess benötigte Wärme direkt in das Schmelzgut eingetragen. Das Verfahren ist effektiv und unter Berücksichtigung grüner Energie auch klimaneutral. ABP kann die gesamte Prozesskette, gerade eben auch für den Ersatz des konventionell beheizten Kupolofens, planen und mit dem Kunden den Weg bis zur Umstellung auf elektrisch betriebene Induktionsofentechnologie beschreiten. Komplettiert wird der ABP-Weg durch digitale Tools, die Transparenz in den Prozess bringen und dadurch Steuerungsmöglichkeiten zur Synchronisierung des verfügbaren Energiestroms mit dem Materialfluss. Ziel ist die optimierte Energienutzung bei maximaler Produktionsleistung.
Wenn Gießereien die Umstellung in Betracht ziehen, um die Potenziale zu nutzen, gibt es zwei Herausforderungen zu beachten:
- Zum einen bedeutet es eine Umstellung von kontinuierlicher Bereitstellung zu diskontinuierlichem Betrieb, dem Chargenbetrieb.
- Die zweite Herausforderung ist die Schrottqualität. Im Kupolofen-Schmelzbetrieb ist es nicht selten an der Tagesordnung, auch schlechte Schrottqualitäten zu fahren. Damit kommt der Induktionsofen-Betrieb nicht zurecht, weil die Ankoppelung dann deutlich schlechter wird. Einen Nutzungsgrad von 100 % zu erreichen, wird damit deutlich erschwert bis unmöglich. Nutzungsgrade von 60 % sind wahrscheinlicher. Diese Lücke so gering wie möglich zu halten, steht und fällt damit, wie das elektromagnetische Feld an den Schrott ankoppelt. Das ist von der Schrottqualität und den Parametern der elektrischen Energieversorgung abhängig.
Planung der Anlage mit dem Meltshop Designer Möchte man auf die Vorteile der Induktionsofen-Technologie setzen und das System zum Beispiel von Kupolofen auf Induktion umstellen, ist eine sorgfältige Planung relevant. Gerade wenn es darum geht, den Flüssigeisenspeicher als Energiespeicher zu nutzen und in den Prozess zu integrieren. Hier lässt sich der gesamte Prozess vorplanen. Um eine Schmelzanlage in dieser Hinsicht perfekt konzipieren, dimensionieren und planen zu können, hat ABP den Meltshop Designer entwickelt (Bild 5).
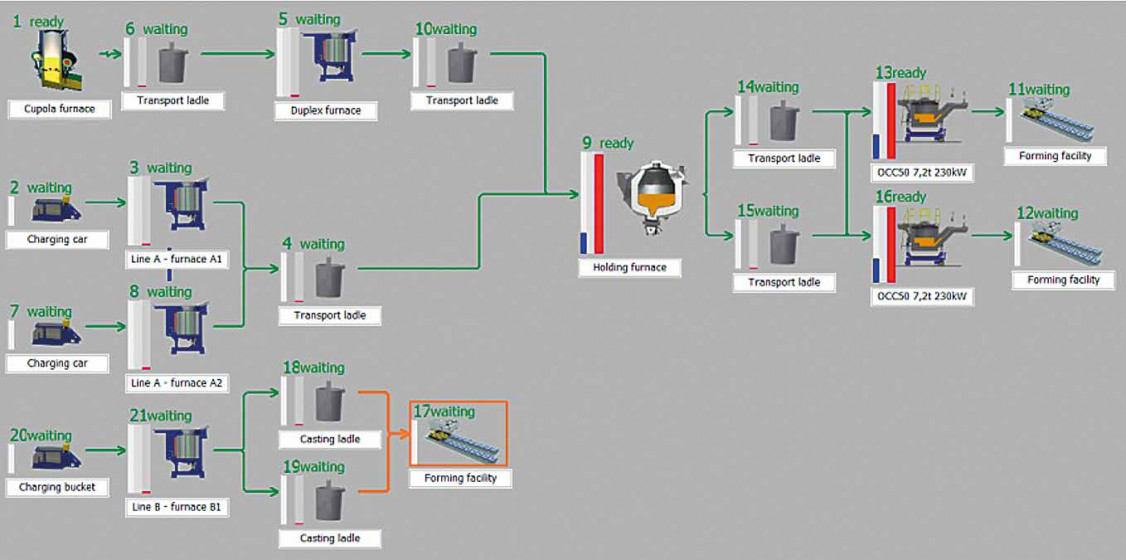
Mit dieser ABP-Eigenentwicklung wird ermittelt, welche Lösung die beste ist, wenn es um den Materialfluss in der Gießerei geht. ABP-Experten können in enger Abstimmung mit den prozessbeteiligten Mitarbeitern des Kunden Simulationen für verschiedene Gießerei-Situationen entwickeln, beim Ofenaufbau Alternativen darstellen, von den Pfannen bis zum Befüllen der Formanlage verschiedene Konfigurationen einbeziehen.
Hierbei ist die genaue Zuordnung der Daten wichtig, um eine Verbindung zu den erzielten Gefüge- und mechanischen Kennwerten herzustellen. Die während dieser Phase gewonnenen Daten dienen einerseits dazu, die Zielparameter für den neuen Schmelzprozess so festzulegen, dass die Kernparameter der Schmelze bei der Umstellung stabil bleiben oder sich verbessern, um einen möglichst reibungslosen Übergang bei der Weiterverarbeitung der Bauteile zu gewährleisten. Diese Phase sollte sich über etwa vier Wochen erstrecken, um sämtliche metallurgischen Zustände zu erfassen. Beim Hochfahren des induktiven Schmelzprozesses dauert es in der Regel weitere vier Wochen, bis alle Aspekte des neuen Verfahrens korrekt abgebildet werden.
OptiCharge: Arbeiten im Konstantleistungsbereich
Weitere Optimierungen sind im Betrieb möglich. Auch hier können Gießereien ansetzen, um die eigenen Prozesse zu verbessern und das Potenzial des Flüssigeisenspeichers bei der Energieverwaltung und der Vermeidung von Lastspitzen größtmöglich zu nutzen. Blicken wir auf die Ankopplung des Induktionsofens, die abhängig vom Lastkreis ist: die Leistung der Anlage stellt sich nach Schüttung des Einsatzgutes aufgrund deren elektrischer sowie magnetischen Eigenschaften ein. Stationäre Verluste durch Nachchargieren müssen also optimiert werden.
ABP ermöglicht es, diese Vorgänge zu messen, auszuwerten und den Kunden beim Chargieren zu führen. Hierzu dient das selbstentwickelte und patentierte Tool OptiCharge (Bild 6).
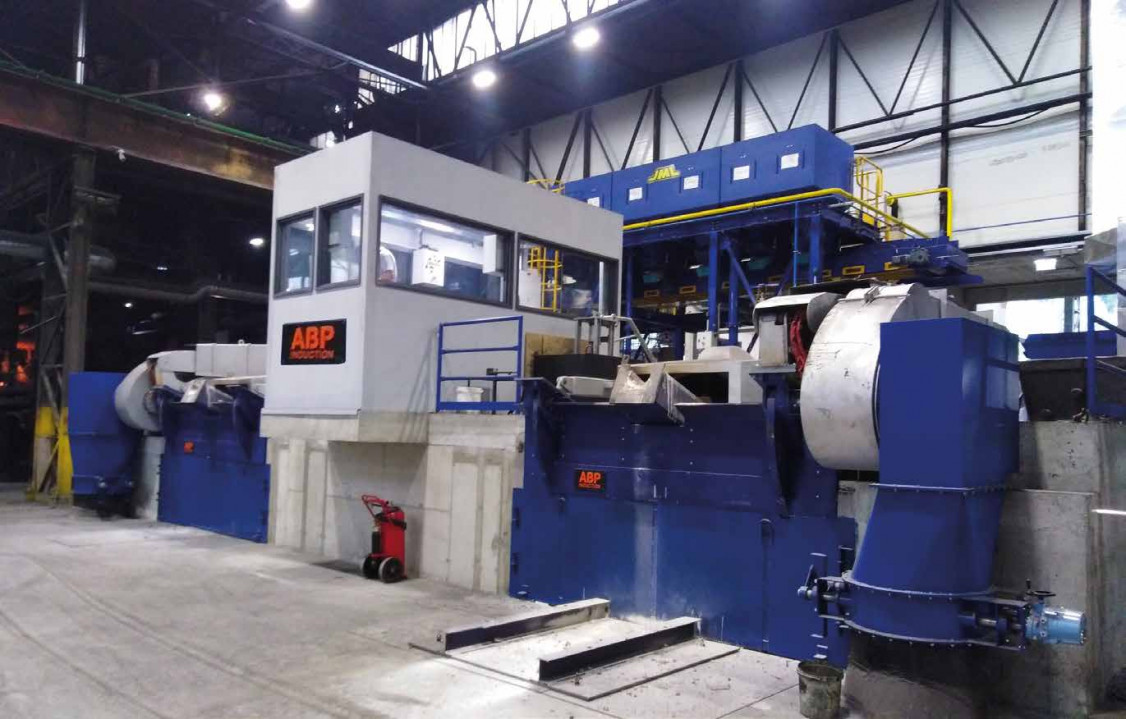
Es misst die elektrischen Einflussgrößen, die zur Leistungsoptimierung notwendig sind. Diese Parameter werden am aktuellen Gewicht gespiegelt und der Algorithmus bestimmt das geringstmögliche Gewicht, das zur Erreichung der vollen Leistungsaufnahme notwendig ist. Eine kontrollierte Chargierung zur optimalen Anpassung des Gewichts an die Leistungsaufnahme über die komplette Chargendauer ist das gewünschte Ergebnis. Wann immer es die physikalischen Bedingungen zulassen, kann nachchargiert werden. Dieses kalte Material koppelt aufgrund seiner ferromagnetischen Eigenschaften optimal an, bis es diese Eigenschaften bei Erreichen der Curie-Temperatur verliert. Die technischen Ofenparameter dazu werden über die digitale Umrichtersteuerung erfasst und über das OptiCharge System in Handlungsempfehlungen umgewandelt. Beim Anfahren einer Charge mit einer Teilfüllung an ferromagnetischem Schmelzgut werden kleine Portionen dieses Materials automatischem nachgefüllt. Dadurch werden im täglichen Produktionsbetrieb messbare Energieeinsparungen und Produktionssteigerungen gegenüber einer ungesteuerten Chargierung realisiert.
Fazit
Die Dekarbonisierung drängt die zukünftige Technologie im Schmelzbetrieb mit steigender CO2-Bepreisung zur Umstellung vom Kupolofen auf die Induktionsofentechnologie. Die Bereitstellung grüner Elektroenergie muss dabei perspektivisch zu wettbewerbsfähigen Weltmarktpreisen gewährleistet werden. Die metallverarbeitende Industrie hat dabei eine besondere Chance: sie hat das Potenzial zur Nutzung des Flüssigeisens als Energiespeicher, um Energiespitzen zu nutzen. Dieser Faktor kann eine große Rolle für die Wirtschaftlichkeit nach der Umstellung spielen. Parallel verändert sich der Markt zu kleineren Serien, was den Prozess zu einer höheren Flexibilität beschleunigt. ABP Induction hat hier Lösungsansätze entwickelt, mit effektiven Planungstools, passenden Ofengrößen und entsprechenden Transformations-Strategien. Die metallurgische Umstellung wird durch die Expertise der ABP-Digitalisierungsplattform ‚myABP2.0‘ mit entsprechenden Anwendungen basierend auf Expertenwissen begleitet. Die Zukunft ist bereits da: es gibt schon verschiedene Referenzprojekte für eine erfolgreiche Umstellung, die sich auf praktisch alle Markt- und Produktionsbedingungen skalieren lassen.
Praxisbeispiel „gelungene Umstellung“
Um die Ziele der Dekarbonisierung zu erreichen, ist der Umstieg des Betriebs von fossilen Brennstoffen hin zu einer praktisch klimaneutralen Produktion von großer Bedeutung, wie dieser Beitrag gezeigt hat. Eine detaillierte Erläuterung der metallurgischen Umstellung sowie der Vorteile beim Betrieb und die Steuerung durch Tools wie ABP OptiCharge und den ABP Meltshop-Designer findet sich in Heft 10/2023 der Giesserei [7], wo an Beispielen der Praxis gezeigt wird, wie eine Umstellung gelingen kann.
Literatur
[1] www.umweltbundesamt.de/themen/klima-energie/erneuerbare-energien/erneuerbare-energien-in-zahlen#ueberblickbeitrag-erneuerbare (abgerufen 12.03.2024).
[2] www.de.statista.com/statistik/daten/studie/156695/umfrage/brutto-stromerzeugung-in-deutschland-nach-energietraegern-seit-2007/ (abgerufen am 12.03.2024).
[3] www.energiewechsel.de/KAENEF/Navigation/DE/Energiewechsel/Erneuerbare-Energien/erneuerbare-energien (abgerufen am 12.03.2024).
[4] www.umweltbundesamt.de/themen/erstmals-ueber-die-haelfte-des-stroms-in (abgerufen 12.03.2024).
[5] https://upload.wikimedia.org/wikipedia/commons/7/7a/Lastprofil_VDEW_H0_Winter.pngLastprofile zeigen das Verbraucherverhalten (abgerufen 12.03.2024).
[6] www.bundesregierung.de/breg-de/schwerpunkte/klimaschutz/faq-energiewende-2067498 (abgerufen 12.03.2024).
[7] Giesserei 110 (2023), [Nr. 10], S. 30-37.
Schlagworte
DesignDigitalisierungEisenFertigungGIFAGussGussteileMesseMetallverarbeitungPlanungProduktionSimulation