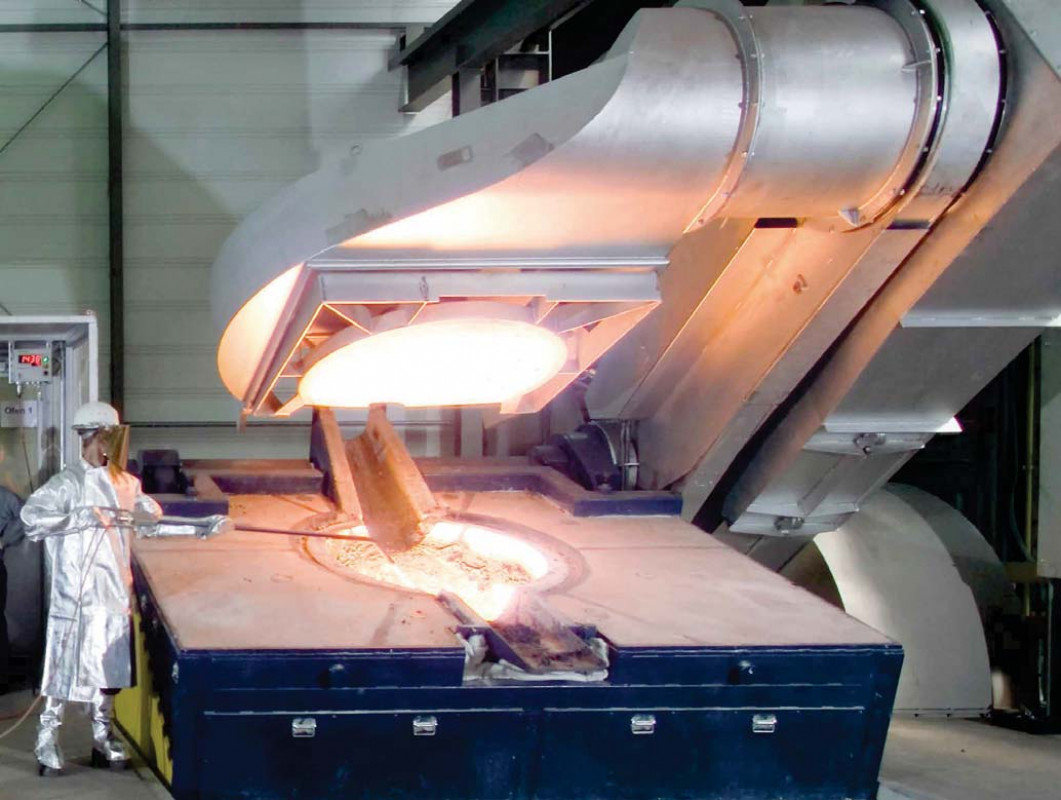
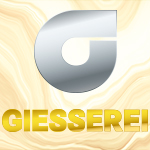
Die Umstellung vom Kupolofen zum Induktionsofen ist ein entscheidender Schritt für Gießereien auf dem Weg zur Dekarbonisierung ihrer Produktion. Eine wichtige Herausforderung dabei ist die Schrottqualität, die beim Induktionsofen besser sein muss als beim Kupolofen. ABP Induction und Zorc Technologies bieten dazu speziell entwickelte Tools an, die eine optimierte Fahrweise des Induktionsofens erlauben. Dieser Beitrag zeigt an Beispielen aus der Praxis wie eine Umstellung gelingen kann.
VON MARCO RISCHE, WOLFGANG BAUMGART, SEBASTIAN HAARDT, STEFAN SCHMITT
Der Druck durch die umweltpolitischen Anforderungen zum Erreichen der festgelegten Klimaziele für industrieller Verbraucher steigt permanent, auch getrieben durch die CO2-Besteuerung fossiler Brennstoffe. Alle industriellen Verbraucher von Koks, Öl und Gas suchen nach alternativen Lösungsansätzen, um den mittelfristig gesteckten Umweltzielen für eine CO2-neutrale Produktion gerecht zu werden. Alle befragten Unternehmen einer Studie von Römheld & Moelle gaben an, dass sie ihre Lieferanten bis spätestens 2050 um klimaneutrale Gussteile bitten werden, 21 % planen dies bis 2025 und 46 % bis 2030 [1].
ABP hat diesen Paradigmenwechsel zur CO2-Neutralität erkannt und sich diesem Ziel durch seine Kampagne „Your Partner on the way to Zero Emission“ gestellt. Um dem Anspruch der Dekarbonisierung gerecht zu werden, sieht ABP großes Potenzial im Ersatz der fossilen Brennstoffe durch moderne Induktionsofentechnologie zur ökologischen, ökonomischen und technischen Unabhängigkeit. Anwender leisten so einen signifikanten Beitrag zur Umsetzung der Ziele für die Dekarbonisierung energieintensiver industrieller Anwendungen.
Die induktive Erwärmung erfolgt über elektrische Energie. Dabei wird die für den Prozess benötigte Wärme direkt in das Schmelzgut eingetragen. Das Verfahren ist effektiv und beim Bezug grüner Energie auch klimaneutral. ABP kann die gesamte Prozesskette für den Ersatz des konventionell beheizten Kupolofens planen und gemeinsam mit dem Kunden den Weg bis zur Umstellung auf elektrisch betriebene Induktionsofentechnologie beschreiten. Komplettiert wird dies durch digitale Tools und KI-Lösungen des ABP-Partners Zorc Technology.
Gießereien mit Kupolofen-Schmelzbetrieb – Status quo & Herausforderungen
Wenn Gießereien die Umstellung von einem Kupolofen- auf einen Induktionsofen-Schmelzbetrieb in Betracht ziehen, gibt es zwei grundsätzliche Herausforderungen zu beachten: Zum einen bedeutet die Umstellung von Kupol- auf Induktionsofen auch eine Umstellung im Betrieb – von kontinuierlicher Bereitstellung zu diskontinuierlichem Betrieb, dem Chargenbetrieb. Zweite Herausforderung ist die Schrottqualität. Im Kupolofen-Schmelzbetrieb ist es nicht selten an der Tagesordnung, auch schlechte Schrottqualitäten zu fahren. Damit kommt der Induktionsofen-Betrieb nicht zurecht, weil die Ankoppelung dann deutlich schlechter wird. Einen Nutzungsgrad von 100 % zu erreichen, wird damit deutlich erschwert bis unmöglich. Nutzungsgrade von 60 % sind wahrscheinlicher. Diese Lücke so gering wie möglich zu halten, steht und fällt damit, wie das elektromagnetische Feld an den Schrott ankoppelt. Das ist stark von der gesetzten Schrottqualität und den Parametern der elektrischen Energieversorgung abhängig.
Ein Beispiel aus der Praxis: Dank der Umstellung von koksbefeuerten Kupolöfen auf Induktion (Bild 1) kann bei Römheld & Moelle ein großer Teil der Emissionen durch eine Änderung des Energiemixes bewältigt werden. Ein Sondervertrag mit seinem Energieversorger ermöglicht es der Gießerei, in den Jahren 2023 und 2024 zu 100 % Strom aus Wasserkraft zu beziehen [2].
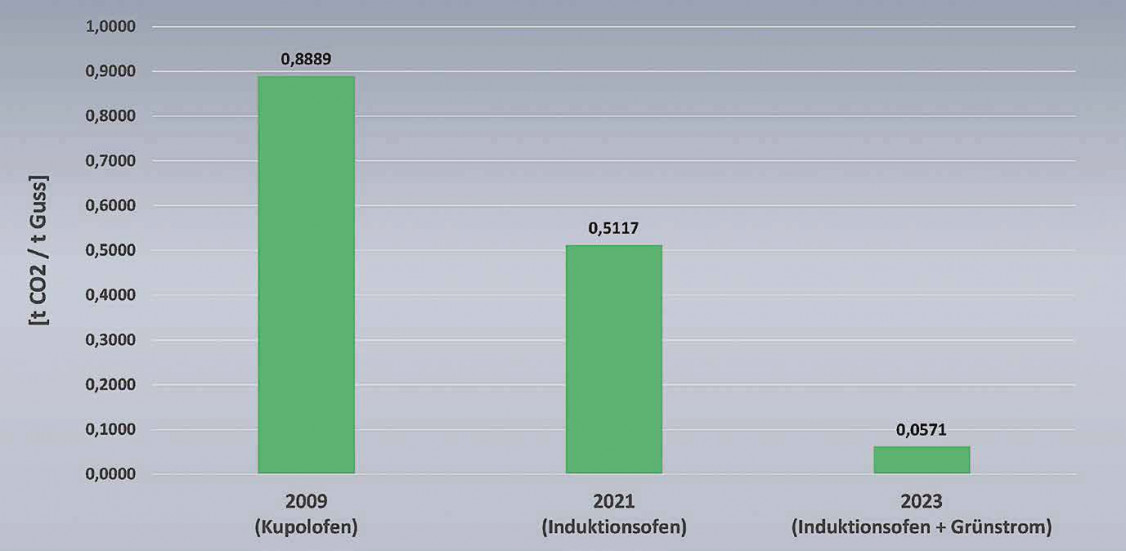
Was bedeutet das aus metallurgischer Sicht? Eisen, das im Kupolofen erschmolzen wird, weist prozessbedingt einen hohen Schwefelgehalt auf. Für die Herstellung von Gusseisen mit Kugelgrafit kommen deshalb ein- oder zweistufige Prozesse zur Herstellung der gießbereiten Schmelze zum Einsatz. Bei der Herstellung von GJV wird jedoch konsequent auf zweistufige Prozesse gesetzt. In diesen zweistufigen Prozessen dient die erste Stufe der Entschwefelung, wobei typischerweise Schwefelgehalte von 0,06 bis 0,025 % erreicht werden. In der zweiten Stufe wird dann die Morphologie der Grafitphase und die Zusammensetzung der metallischen Matrix eingestellt, um die gewünschten mechanischen und physikalischen Eigenschaften des Werkstoffs im Bauteil zu erreichen (Bild 2).
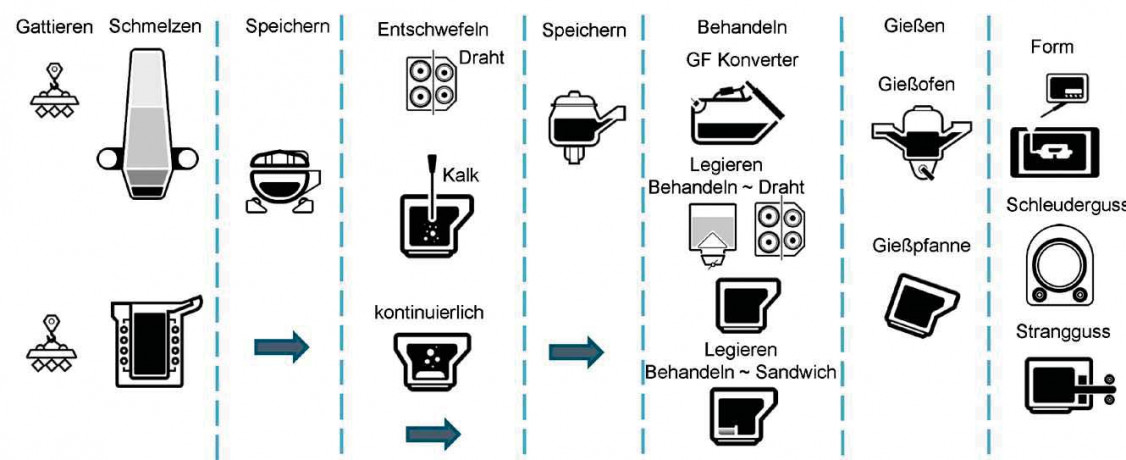
Unter Verwendung von kalziumhaltigen Verbindungen ist eine kontinuierliche Entschwefelung von Kupolofeneisen möglich. Speziell ist die Verwendung von Kalziumcarbid als Entschwefelungsmittel ebenfalls eine Option, diese wird jedoch aufgrund von Umweltaspekten heutzutage nur noch selten in Gießereiprozessen eingesetzt.
Zu den Verfahren der diskontinuierlichen Entschwefelung zählen das Mg-Drahteinspulverfahren sowie das moderne Kalk-Einblasverfahren, das vom Institut für Technologien der Metalle der Universität Duisburg-Essen unter der Leitung von Rüdiger Deike und der Werkstoffentwicklung der Firma Fritz Winter unter der Leitung von Marc Walz entwickelt wurde [3], [4].
Um aus dem resultierenden Basiseisen die gießfertige Schmelze zu erzeugen, erfolgt in einem zweiten Schritt eine Behandlung mit Magnesium, seltenen Erden und Impfstoffen. Hierbei haben sich insbesondere das Drahteinspul- und das Überschüttverfahren durchgesetzt. Moderne Drahteinspulverfahren verwenden neben dem Magnesiumdraht auch einen Impfdraht, wodurch während der Behandlung eine dynamische Impfung erfolgt. Der abschließende Schritt auf dem Weg zur angestrebten Metallurgie ist die Impfung während des Gießvorgangs. Diese Impfung kann mittels einer Gießstrahlimpfung oder eines Impflings im Einguss- oder Laufsystem erfolgen.
Anforderungen an einen modernen Induktionsofen-Schmelzbetrieb
Wie eingangs bereits beschrieben kann ein moderner Induktionsofen nur mit hochwertigen Metallen und Schrotten arbeiten. Deswegen empfehlen Induktionsofen-Hersteller in der Regel auch eine bestimmte Schrottqualität, mit der die Anlage betrieben werden sollte. Anderenfalls kann aufgrund der schlechteren Ankopplung nicht die volle Leistung entwickelt werden. Ziel muss aber ein Konstantleistungsbereich sein – idealerweise mit 100 % Leistungseintrag über den Chargenverlauf, um die Schmelzzeit und damit den Energieaufwand zu minimieren und natürlich die Produktivität zu maximieren.
Die Ankopplung des Induktionsofens ist allerdings abhängig vom Lastkreis: Die Leistung der Anlage stellt sich nach Schüttung des Einsatzgutes aufgrund dessen elektrischer sowie magnetischen Eigenschaften ein. Stationäre Verluste durch Nachchargieren müssen also optimiert werden. ABP ermöglicht es, diese Vorgänge zu messen, auszuwerten und den Kunden beim Chargieren zu führen. Dazu setzt ABP das selbstentwickelte und patentierte Tool OptiCharge ein (Bild 3). Es misst die elektrischen Einflussgrößen, die zur Leistungsoptimierung notwendig sind. Diese Parameter werden am aktuellen Gewicht gespiegelt und der Algorithmus bestimmt das geringstmögliche Gewicht, das zur Erreichung der vollen Leistungsaufnahme notwendig ist. Eine kontrollierte Chargierung zur optimalen Anpassung des Gewichts an die Leistungsaufnahme über die komplette Chargendauer ist das gewünschte Ergebnis. Wann immer es die physikalischen Bedingungen zulassen, kann nachchargiert werden. Dieses kalte Material koppelt aufgrund seiner ferromagnetischen Eigenschaften optimal an, bis es diese an der Curie-Temperaturpunkt bei 760 °C verliert.
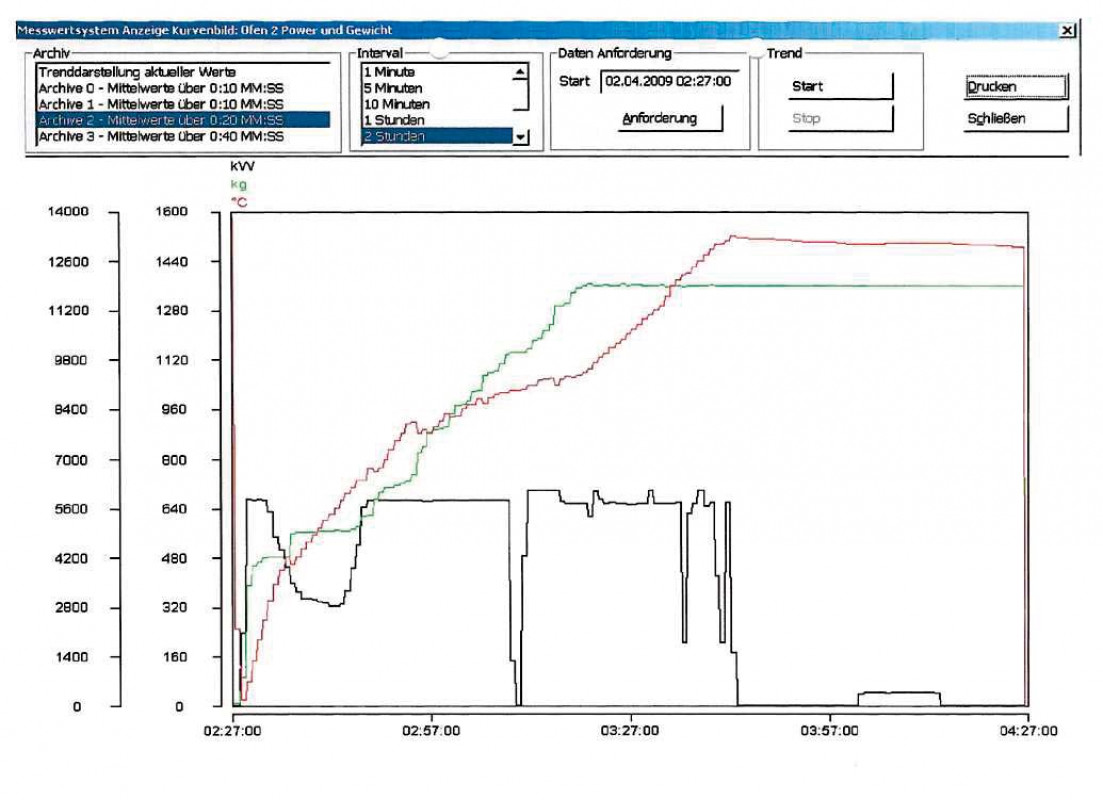
Die technischen Ofenparameter dazu werden über die digitale Umrichtersteuerung erfasst und über das OptiCharge-System in Handlungsempfehlungen für die energieeffiziente Chargierung umgewandelt. Beim Anfahren einer Charge mit einer Teilfüllung an ferromagnetischem Schmelzgut werden kleine Portionen dieses Materials automatisch nachgefüllt. Dadurch sind im täglichen Produktionsbetrieb messbare Energieeinsparungen und Produktionssteigerungen gegenüber einen ungesteuerten Chargierung realisierbar. Erhebungen zeigen, dass Induktionsöfen schon im heutigen Strommix weniger als die Hälfte an CO2-Emissionen für das Schmelzen einer Tonne Gusseisen im Vergleich zu Kupolöfen erzeugen. Steigt der Anteil an regenerativ erzeugtem Strom, sinken die CO2-Emissionen entsprechend.
Dieses System ist also eminent wichtig für den Umstieg vom Kupolofen zum Induktionsofen, um weiterhin eine hohe kontinuierliche Bereitstellung des Flüssigeisens für den Prozess zu ermöglichen. OptiCharge führt an dieser Stelle dazu, dass Leistungseinbrüche auf ein Minimum reduziert werden.
Zum physikalischen Hintergrund: Die Möglichkeit zum Betrieb im Konstantleistungsbereich ist dadurch entstanden, dass es Thyristoren in Baugrößen gibt und sich dabei etabliert hat, dass immer die nächstgrößere Baugröße eingesetzt wird, die über der gewünschten Punktleistung liegt. Dadurch entsteht eine optimale Betriebsart. Das bedeutet allerdings auch, dass Strom und Spannung im Produkt mehr leisten können – die Punktleistung an sich und ein bestimmtes Leistungsfenster darüber hinaus.
Das Prinzip funktioniert, wie die Lastkennlinien zeigen (Bild 4): Fährt man den Induktionsofen auf volle Spannung und es ist wenig Schrottmaterial im Ofen, koppelt wenig Material an und man fährt den Betrieb mit wenig Leistung. Selbst wenn der Ofenbetreiber mehr Material hinzugibt und der Ofen zur Hälfte gefüllt ist, erreicht man den Punkt der 100-prozentigen Leistung bei voller Spannung, und das, obwohl nur 60 % des Stroms genutzt werden. Führt man weiteres Material hinzu, koppelt es noch besser an, nutzt entsprechend mehr Strom und der Ofen braucht dabei weniger Leistung, um mehr Strom zu treiben. Das ist die Spannungsreserve, die man nutzen kann trotz voller Leistung. In der Praxis kommt es dennoch vor, dass über diesen Punkt hinaus weiter Material hinzugegeben wird, da dann der Prozess einfacher wird, weil so seltener Material hinzugegeben werden muss und der Arbeitsaufwand geringer ist. Dem Prozess ist das allerdings nicht zuträglich, denn würde man eher mit dem Auffüllen des Ofens stoppen, würde das eingegebene Material zügig erwärmt, weil der Ofen schnell bis zur Curie-Temperatur ankoppelt. Der Schrott verliert dann seine magnetischen Eigenschaften, die Ankopplung wird schlechter - und der Betrieb fällt eine Kennlinie zurück. Jetzt benötigt man wieder mehr Spannung, um den Strom zu treiben und damit auf 100 % Leistung zu kommen. Da aber immer weniger Material magnetisch ist, geht die Stromstärke immer weiter zurück, da sich die Spannung auf maximalem Niveau befindet. Die Folge ist, dass die Leistung sinkt. Würde man stattdessen jetzt Material nachgeben, hätte man weiter 100 % Leistung.
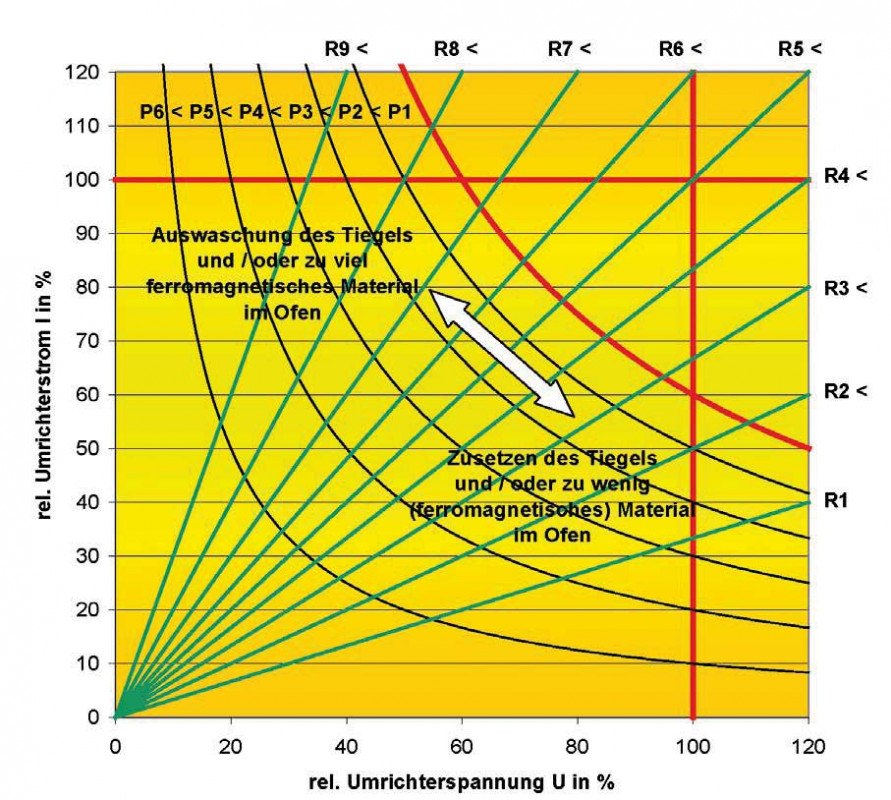
Dieses System ist von wesentlicher Bedeutung für Umsteiger vom Kupolofen auf den Induktionsofen, weil diese Betriebe oft mit schlechteren Schrottqualitäten zurechtkommen müssen, was eben dafür sorgt, dass die Ankopplung schlechter wird. Sie sind außerdem auf eine hohe Bereitstellung ihres Flüssigeisens für ihre Prozesse angewiesen, deswegen ist ein Tool zur Steuerung wie OptiCharge so wertvoll.
Umstellung des Schmelzbetriebs
Um besser bewerten zu können, wie Prozesse, die das induktive Schmelzen verwenden sich von solchen unterscheiden, die einen Kupolofen als Schmelzaggregat einbinden, wollen wir die Besonderheiten anhand von drei Prozessen aus der Praxis erläutern.
Beispiel 1: GJL-Bremsscheiben
Bei der Produktion von Bremsscheiben aus Gusseisen mit Lamellengrafit kann der Kupolofen von seinem vorteilhaften Keimzustand profitieren. Allerdings sind die Anforderungen an Bremsscheiben in den letzten Jahren erheblich gestiegen. Dies hat zur Folge, dass vom Werkstoff eine hohe Wärmeleitfähigkeit gefordert wird, die nur erreicht werden kann, wenn der Gusswerkstoff übereutektisch erstarrt. Die dafür benötigten Kohlenstoffgehalte können in vielen Fällen nicht direkt durch den Kupolofen erzeugt werden, weshalb eine Aufkohlung erforderlich wird. Zusätzlich erfordern die Klangspezifikationen zur Vermeidung des Quietschens moderner Bremsscheiben Kohlenstoffgehalte in engen Toleranzen, die sich nur durch Duplizieren im Induktionsofen herstellen lassen. All dies entfällt bei der Schmelze im Elektroinduktionsofen (Bild 5).
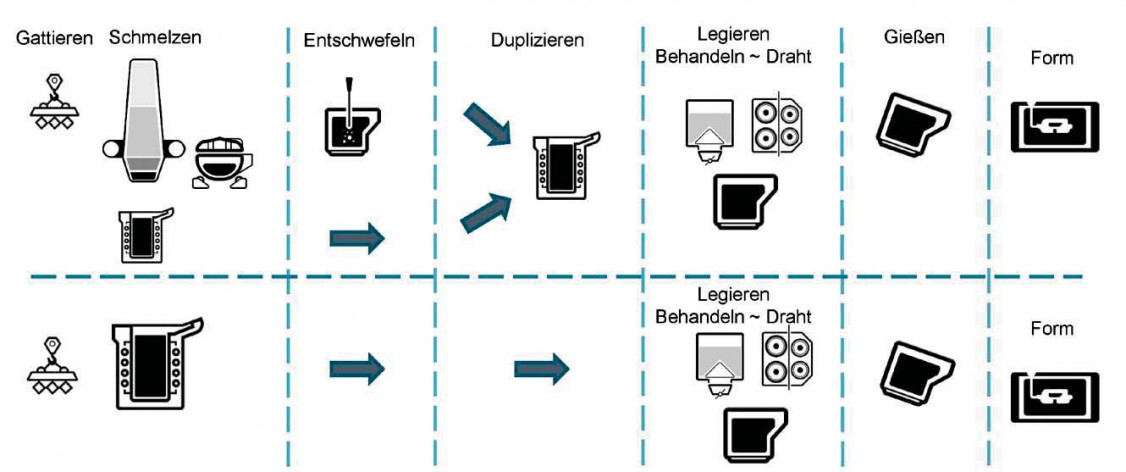
Die Herausforderung bei der Verwendung einer induktiven Schmelzweise ist zum einen eine dynamische Impfung, die sich technisch einfach über die Zugabe eines Impfdrahtes in die Gießrinne realisieren lässt. Strontium als impfwirksames Element ist hier das Mittel der Wahl. Eine weitere Schwierigkeit besteht in der Bekämpfung von Mikroporositäten, die oft an den Übergängen von Hut zu Scheibe auftreten. Mikroporositäten bilden sich zwischen den Armen großer Austenitdendriten. In diesem Zusammenhang hat sich der gezielte Einsatz von Lanthan im letzten Impfschritt als hilfreich erwiesen.
Beispiel 2: GJS-Gussrohre
Die Fertigung von GJS-Gussrohren erfolgt mittels des Schleudergussverfahrens. Dabei kühlt das Gussrohr an der Kokillenwand ab und bildet Eisenkarbide. Da Eisenkarbid einen Kohlenstoffgehalt von 6,7 % aufweist, wird die Menge des freien Grafits, der bei der Erstarrung entsteht, stark reduziert. Dadurch kann der freie Grafit nicht dem Schrumpfen entgegenwirken, wenn die flüssige Phase erstarrt. Dies hat den gewünschten Effekt: Das Gussrohr schrumpft und kann aus der Kokille entnommen werden. Anschließend wird das Rohr durch den Glühofen geführt, wo das Eisenkarbid sich auflöst und der Grafit zu den Sphäroliten diffundiert. Das Rohr dehnt sich aus und erreicht seine finale Dimension. Der ursprüngliche Keimzustand aus den Schmelzaggregaten beeinflusst dabei unmittelbar die Abmessungen des Bauteils.
Ein Kupolofen erzeugt aufgrund variierender Füllstände im Vorherd sowie durch sich verändernde Metallurgie während der An- und Abschaltzyklen einen schwankenden metallurgischen Zustand. Die resultierende Dynamik im Keimzustand erfordert bei der Verwendung eines Kupolofens einen komplexen Regelkreis, während diese Regelung beim Schmelzen im Elektroinduktionsofen wesentlich einfacher ausgeführt wird (Bild 6).
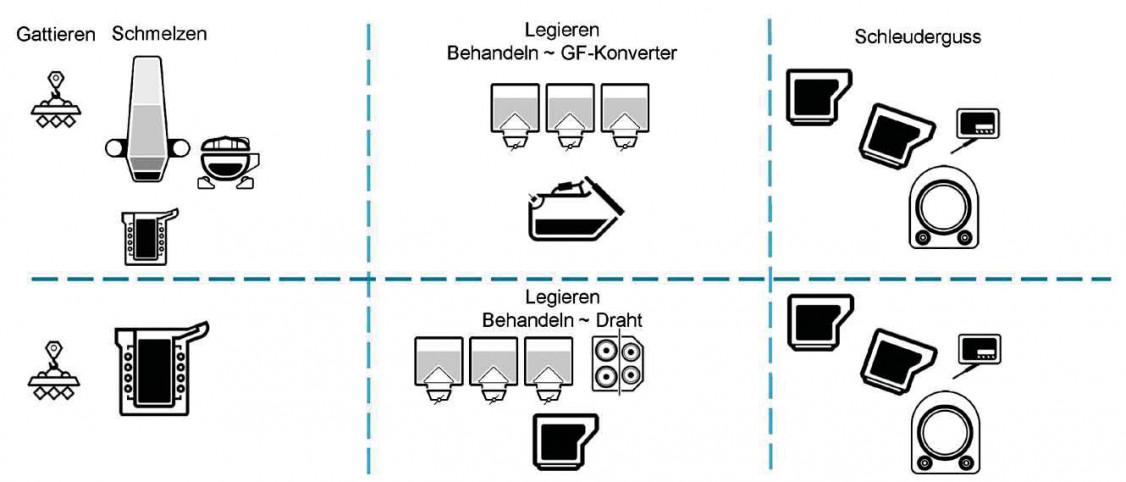
Beispiel 3: GJV
Gusseisen mit Vermikulargrafit findet sich im Antriebsstrang im Zylinderkopf, in den Zylinderkurbelgehäusen sowie in den Kupplungsscheiben. Es handelt sich um einen Werkstoff für den Massenmarkt im Schwerlastverkehr. Auch findet der Werkstoff Verwendung in Bremsscheiben bei Hochgeschwindigkeitszügen.
Wenn GJV durch die Zugabe von entschwefeltem Kupolofeneisen hergestellt wird, ist diese Zugabe begrenzt, da die Begleitelemente aus dem Kupolofen häufig die finalen Analysespezifikationen überschreiten können. Der Anteil an entschwefeltem Eisen kann spezifikationsbedingt zwischen 30 und 70 % variieren. Beim Einsatz dieses Werkstoffs kann der Kupolofen seine Stärke, den von Natur aus vorhandenen guten Keimzustand, nicht effektiv nutzen. Die Bildung von Vermikeln tritt bei hoher Unterkühlung auf, während ein guter Keimzustand metallurgisch bedingt automatisch Sphäroliten entstehen lässt.
Der Regelkreis für die GJV-Herstellung modifiziert die Schmelze durch Zugabe von Magnesium, Cer-Mischmetall und Impfmittel. Dieser Regelkreis nutzt die Messwerte aus der thermischen Analyse der gießfertigen Schmelze und korrigiert rückwirkend die Steuergrößen der nächsten Pfanne über eine Rückkopplungsschleife. Die Schwankungen im Basiseisen aufgrund der Beimischung von Kupolofeneisen stellen hierbei eine Störgröße dar. Ein Wechsel zu vollständig im Induktionsofen geschmolzenem Eisen vereinfacht diesen Prozess erheblich (Bild 7).
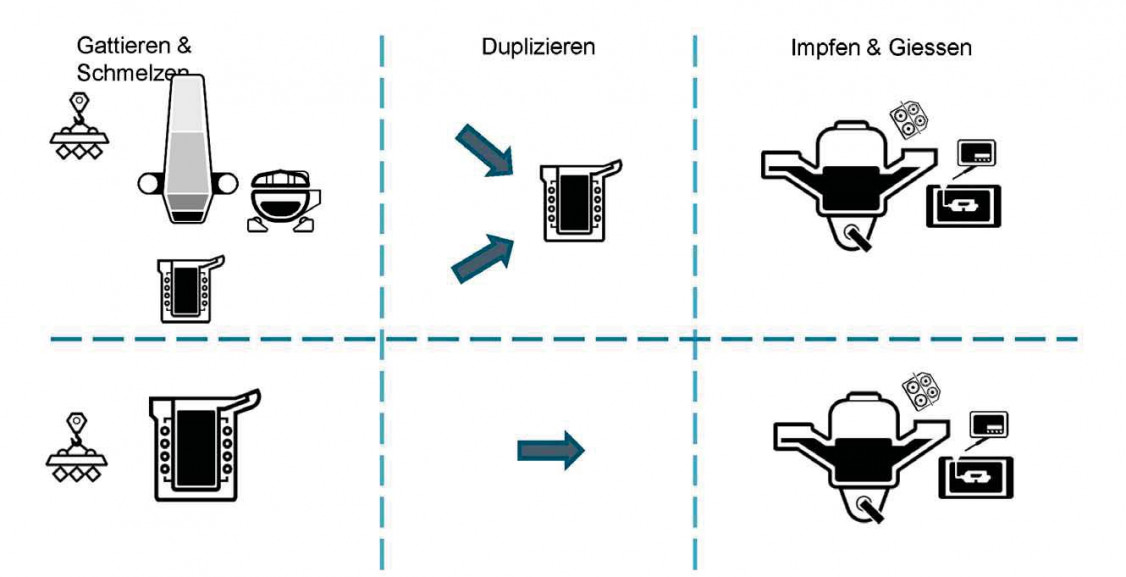
Planung und Umsetzung des Umstiegs
Das Engineering-Team
„Wie muss unsere Schmelzanlage dimensioniert sein?“ „Wie kann ich die Produktivität erhöhen?“ „Welche Erweiterungen rechnen sich im ROI am schnellsten?“ – Fragen, die sich Gießerei-Betreiber bei der Umstellung vom Kupolofen auf den Induktionsofen stellen. Und es sind wichtige Fragen, da sie nicht selten hohe Investitionen bedeuten oder zu einer Erhöhung des Ertrags führen können. Um eine Schmelzanlage perfekt konzipieren, dimensionieren und planen zu können, hat ABP den Meltshop Designer entwickelt. Damit wird ermittelt, welche Lösung die Beste ist, wenn es um den Materialfluss in der Gießerei geht. ABP-Experten können in enger Abstimmung mit den prozessbeteiligten Mitarbeitern des Kunden Simulationen für verschiedene Gießerei-Situationen entwickeln, beim Ofenaufbau Alternativen darstellen und von den Pfannen bis zum Befüllen der Formanlage verschiedene Konfigurationen einbeziehen.
Das metallurgische Team
Das metallurgische Team muss sowohl über Fachkenntnisse in der Gusseisenherstellung mit dem Induktionsofen verfügen als auch Fähigkeiten in Bezug auf die Erzeugung des gewünschten Keimzustandes besitzen. Im Gegensatz zum Kupolofen wird dieser im Induktionsofen größtenteils synthetisch erzeugt. Das metallurgische Team erstellt einen digitalen Zwilling der kompletten metallurgischen Prozesskette um alle Prozessschritte im Vorfeld der Umstellung vom Kupolofen zum Induktionsschmelzbetrieb bewerten und optimieren zu können.
Die Energieeffizienz beim induktiven Schmelzen hängt entscheidend von der Abfolge der zu chargierenden Materialien sowie dem Zeitpunkt des Nachchargierens ab. Diese Faktoren fließen in die Wissensgrundlage des Digitalen Zwillings ein, sodass die Zorc Genesis-KI aufgrund dieses Fachwissens die Chargenzusammenstellung und Schmelzreihenfolge berechnet. Zur Bestimmung des optimalen Zeitpunkts für die Zugabe, der sich aus der aktuellen Ankopplung und der Curie-Temperatur ergibt, hat ABP das bereits erwähnte, patentierte Tool Opticharge entwickelt.
Der synthetische Keimzustand wird in mehreren Stufen erzeugt. Dies beginnt im Ofen über die Zugabe von Siliziumcarbid (SiC), dessen besondere Physik beim Lösungsvorgang die Grundlage für den Keimzustand bildet [5]. Der nächste Schritt zur Erzielung des angestrebten Keimzustands bei GJS- und GJV-Legierungen beinhaltet die Zugabe von Cer-Mischmetall (CerMM) sowie die Kohlenstoffzugabe vor der Behandlung. Cer-Verbindungen weisen eine hohe Dichte auf und gehen auch während des Behandlungsprozesses nicht verloren. Bei der Herstellung von dickwandigem Gusseisen muss natürlich berücksichtigt werden, dass Cer-Verbindungen zu unerwünschten Grafitformen führen können, bis hin zu Chunky Grafit. Hierbei ist ein metallurgischer Balanceakt erforderlich, bei dem durch die Zugabe von Elementen wie Antimon oder Bismut ein Gleichgewicht erzeugt wird, dass sich positiv auf die Grafitausscheidung auswirkt.
Ein Kernaspekt des metallurgischen Teams ist die Verzahnung von Beratungsservice und Produktionsbetrieb. Das Serviceteam hat durch seine breite Erfahrungsbasis die Möglichkeit das Produktionsteam umfassend zu schulen. Das Produktionsteam wiederum besitzt genaue Kenntnisse der Gießereiabläufe und bringt einen bedeutsamen Erfahrungsschatz mit, der in die Ablaufplanung einfließen muss.
Die konkrete Umsetzung
Zeitplanung
Die Zeitschiene bei der Umstellung von einem Kupolofen zu einem induktiven Schmelzaggregat ist dabei die größte Herausforderung und erfordert eine strategische Herangehensweise. Sie stellt Anforderungen an das Planungsteam, das ausführende Engineering-Team für die Umsetzung und die Produktion zur Nutzung der neu aufgebauten Prozesskette. Dabei muss der Zustand der bestehenden Produktionsumgebung einschließlich aller eingebundener Aggregate unter Berücksichtigung aller Parameter und Einflussgrößen auf die neu gestaltete Prozess- und Anlagentechnik umgesetzt werden.
Engineering-Phase
In der Engineering Phase kommt der Meltshop-Designer zum Einsatz, den seine Variabilität so wertvoll macht. ABP-Experten können sämtliche Werkstoffe simulieren, indem sie auf eine große Datenbank zugreifen oder neue Werkstoffe in diese einarbeiten. Auch verschiedene einmalige oder periodische Ereignisse lassen sich simulieren, zum Beispiel die Limitierung der Stromzufuhr, ein nicht gerade seltenes Problem, bei dem Energieanbieter zu bestimmten Zeiten die Stromzufuhr reduzieren, wenn an anderen Stellen im Stromnetz gerade mehr Energie abgerufen wird. Grundlage für die Simulation sind Daten: Der Mehrwert entsteht aus der Analyse durch die ABP-Experten basierend auf der Verknüpfung der Informationen. Aus der Simulation ergeben sich die Handlungsempfehlungen für den Umstieg vom Kupolofen auf den Induktionsofen.
Auch die Genesis-KI von Zorc arbeitet mit Daten und nutzt den Digitalen Zwilling als Grundlage, um die Prozessabläufe zu steuern. In der Planungsphase wird sie dazu eingesetzt, die Abläufe im neu gestalteten Schmelzbetrieb zu simulieren und zu optimieren. Dies hilft, Engpässe frühzeitig im Planungsprozess zu erkennen und zu vermeiden.
Übergang der Metallurgie vom Kupolofenprozess zum induktiven Schmelzen
Während der Kupolofen noch aktiv ist, werden Messungen des metallurgischen Zustands mithilfe von thermischer Analyse, Spektrometrie und Verbrennungsanalyse durchgeführt. Hierbei ist die genaue Zuordnung der Daten wichtig, um eine Verbindung zu den erzielten Gefüge- und mechanischen Kennwerten herzustellen. Dies leistet die von Zorc entwickelte serviceorientierte Software Foundry-Cloud. Die moderne thermische Analyse verwendet Doppelkammertiegel, um die finale Gießstrahlimpfung oder Gießsteinimpfung zu simulieren.
Die während dieser Phase gewonnenen Daten dienen einerseits dazu, die Zielparameter für den neuen Schmelzprozess so festzulegen, dass die Kernparameter der Schmelze bei der Umstellung stabil bleiben oder sich verbessern, um einen möglichst reibungslosen Übergang bei der Weiterverarbeitung der Bauteile zu gewährleisten. Diese Phase sollte sich über etwa vier Wochen erstrecken, um sämtliche metallurgischen Zustände zu erfassen. Beim Hochfahren des induktiven Schmelzprozesses dauert es in der Regel weitere vier Wochen bis alle Aspekte des neuen Verfahrens im Digitalen Zwilling korrekt abgebildet werden.
Werkzeuge zur optimalen Planung und Steuerung eines modernen Produktionsprozesses
Wie erfolgt die Steuerung der Metallurgie und wie erfolgt die Steuerung der Transportlogistik und der Schmelze-Behandlungs- und Gießaggregate? Beides lässt sich mit einem Satz beantworten: Mit der Zorc Genesis-KI, deren Wissen in einen Digitalen Zwilling integriert ist. Der Digitale Zwilling spiegelt den Chargier- und Schmelzprozess wider, indem er die physikalischen Vorgänge im Ofen virtuell nachbildet. Dabei berücksichtigt er die Schüttung sowohl in den Chargierrinnen als auch im Ofen selbst. Er simuliert den Sauerstoffhaushalt und die Dynamik der keimwirksamen Elemente. Des Weiteren beschreibt er den Energiefluss im Induktionsschmelzofen einschließlich der Kühlleistung.
Während des Umschütt- und Transportprozesses verfolgt er die Wechselwirkungen mit der Umgebung (Luftsauerstoff) und berechnet den Wärmeabfluss durch Konvektion und Strahlungswärme. Der Digitale Zwilling besitzt eine umfassende Kenntnis über die Physik und Chemie der Drahteinspulververfahren sowie der Überschüttverfahren und simuliert die damit einhergehenden keimwirksamen Prozesse. Im Gieß- und Erstarrungsprozess führt der Zwilling eine simulationsbasierte Analyse durch, um die Auswirkungen der Schmelzzusammensetzung und des Keimzustands auf die Eigenschaften der Werkstücke zu ermitteln. Darüber hinaus behält der Digitale Zwilling auch scheinbar alltägliche Abläufe im Blick: Er kalkuliert die Dauer einer Staplerfahrt, erkennt Engpässe beim Zapfen des Eisens und berücksichtigt die Pausenzeiten der Staplerfahrer.
Datenquellen des Digitalen Zwillings
Um seine Vorhersagen mit der aktuellen Ist-Situation abzugleichen, benötigt der Digitale Zwilling Informationen über den aktuellen Produktionsstatus. Die „Sinne“ des Digitalen Zwillings sind die in der Produktionsumgebung vorhandenen Messgeräte. Traditionelle Messinstrumente wie Spektrometer ermitteln die Schmelzzusammensetzung, während Temperaturmesslanzen und Pyrometer die Badtemperatur messen. Verfahren wie die thermische Analyse erfassen die Dynamik des Erstarrungsprozesses und ermöglichen Schlussfolgerungen über den Keimzustand und die Grafitmorphologie.
Systeme wie das Zorc Track & Trace dienen der Positionsbestimmung von Staplern, sogar in Hallen mittels „Indoor GPS“, sowie der Verfolgung der Pfannenposition im Prozessablauf. Eine serviceorientierte Software wie die Foundry-Cloud stellt sämtliche erforderlichen Dienste zur Verfügung, um Datenquellen wie Messgeräte, SPS-Systeme oder IoT-Geräte auszulesen und in eine strukturierte Datenbasis zu überführen.
Und was macht die KI? Produktionsplanung und Prozesssteuerung
Die KI hat die Aufgabe, die nächsten Schritte kurz-, mittel- und langfristig zu planen, um die gestellten Aufgaben im Produktionsprozess effektiv zu lösen. Ähnlich einem Schachcomputer sucht sie nach der optimalen Strategie. Die Art und Weise, wie die Aufgabenstellung formuliert wird, kann den Charakter der Produktion beeinflussen. Es stellt sich die Frage, ob die Kostenpriorität höher ist als die Einhaltung von Terminen oder umgekehrt. All diese Faktoren können mithilfe von Parametern eingestellt werden. Die KI errechnet optimale zukünftige Trajektorien und entwickelt gleichzeitig einen Plan, der Ressourcen wie Arbeitskräfte, Energieverbrauch, Stromkosten usw. in Betracht zieht.
Interaktion mit Prozessverantwortlichen und Mitarbeitern
Die Zorc Genesis-KI erstellt einen Arbeitsablaufplan auf ähnliche Weise wie ein Navigationssystem eine Route vorschlägt. Analog zu einem Navigationssystem ist der menschliche Planer nicht verpflichtet, sich strikt an diesen Plan zu halten. Stattdessen kann er davon abweichen. Die Genesis-KI berechnet dann, basierend auf der neuen Situation, einen angepassten Arbeitsablauf.
Die Aufgaben innerhalb der Arbeitsabläufe werden über die Foundry-Cloud an die Mitarbeiter mittels mobiler oder stationärer Endgeräte verteilt. Die Rückmeldungen dienen der Genesis-KI dazu den aktuellen Status der Produktion zu erfassen und die Arbeitsabläufe dynamisch an abweichende Situationen anzupassen. Ein sich selbst optimierender Prozess: Durch die beschriebene Vorgehensweise generiert die Produktion innerhalb der FoundryCloud Daten, die dazu dienen, sämtliche Aspekte des Digitalen Zwillings zu verfeinern. Dieser wiederum befähigt die Genesis-KI dazu, sämtliche Produktionsaspekte weiter zu optimieren und gleichzeitig aus den Erfahrungen der Mitarbeiter zu lernen.
Fazit
Um die Ziele der Dekarbonisierung zu erreichen, ist der Umstieg des Betriebs von fossilen Brennstoffen hin zu einer praktisch klimaneutralen Produktion von großer Bedeutung. Wie können sich Gießereien mit Kupolofen-Betrieb der Notwendigkeit der Dekarbonisierung stellen? Für die Experten von ABP Induction und Zorc Technology liegt die Lösung im Umstieg vom Kupolofen- zum Induktionsofen- Betrieb und in der Steuerung der Prozesse durch digitale Tools inklusive KI. Der Induktionsofen weist eindeutige Vorteile beim Betrieb mit hochwertigen Schrotten auf und durch zusätzliche Tools wie ABP OptiCharge und den ABP Meltshop-Designer lassen sich Produktionskapazität und -rate erhöhen und die Energieeffizienz verbessern. Die Flexibilität der Produktion bei hohen Qualitätsanforderungen ist durch eine dynamische Produktionsplanung und -steuerung unter Einsatz der Digitalisierung erzielbar. Der Einsatz der Zorc Genesis-KI stellt die nächste Evolutionsstufe dieser Systeme dar und wird zu einer Effizienzsteigerung auch in komplexen Produktionssituationen führen.
https://abpinduction.com
www.zorc-technology.com
Literatur
[1] Castings, show me your footprint! In: Foundry Planet, abgerufen über: https://www.foundry-planet.com/d/castingsshow-me-your-footprint/
[2] A big step towards a small footprint. In: Foundry Planet, abgerufen über: https://www.foundry-planet.com/d/abig-step-towards-a-small-footprint/
[3] M. Walz, R. Deike, EKALGU- Automatisierte Einblasanlage zur kalkbasierten Entschwefelung und Legierungseinstellung von Gusseisen, Herausgeber: Bundesministerium für Bildung und Forschung, 2020, abgerufen über: https://r-plus-impuls.de/rplus-de/verbundprojekte/projekte/abgeschlossen/ekalgu.php
[4] Deike, R.; Brümmer, A.; Kahrl, A.; Smaha, B.; Walz, M.; Hentsch, R.; Baumgart, W.; Boenkendorf, U.: SubMag – Substitution von Magnesium bei der Entschwefelung von Gusseisen, in Innovative Technologien für Ressourceneffizienz – Strategische Metalle und Mineralien-Ergebnisse der Fördermaßnahme r³ (Hrsg. A. Dürkoop, C. P. Brandstetter, G.Grabe, L. Rentsch), Fraunhofer Verlag, Stuttgart, 2017, (ISBN: 978-3-8396-1102-9)
[5] Semleit, T., Adhiwiguna, I., Wijaya, J., Deike, R.: Investigation of silicon carbide dissolution behavior in molten cast iron under specific consideration of the formation of reaction layers, GIESSEREI Special 01/2021, 46-53, abgerufen über https://doi.org/10.17185/duepublico/77012
Schlagworte
CastingDesignDigitalisierungEisenEnergieeffizienzFertigungForschungFoundryGießereiGussGusseisenGussteileLogistikMagnesiumMesseMetallurgiePlanungProduktionSchmelzenSimulationSoftwareVerlagWerkstoffe