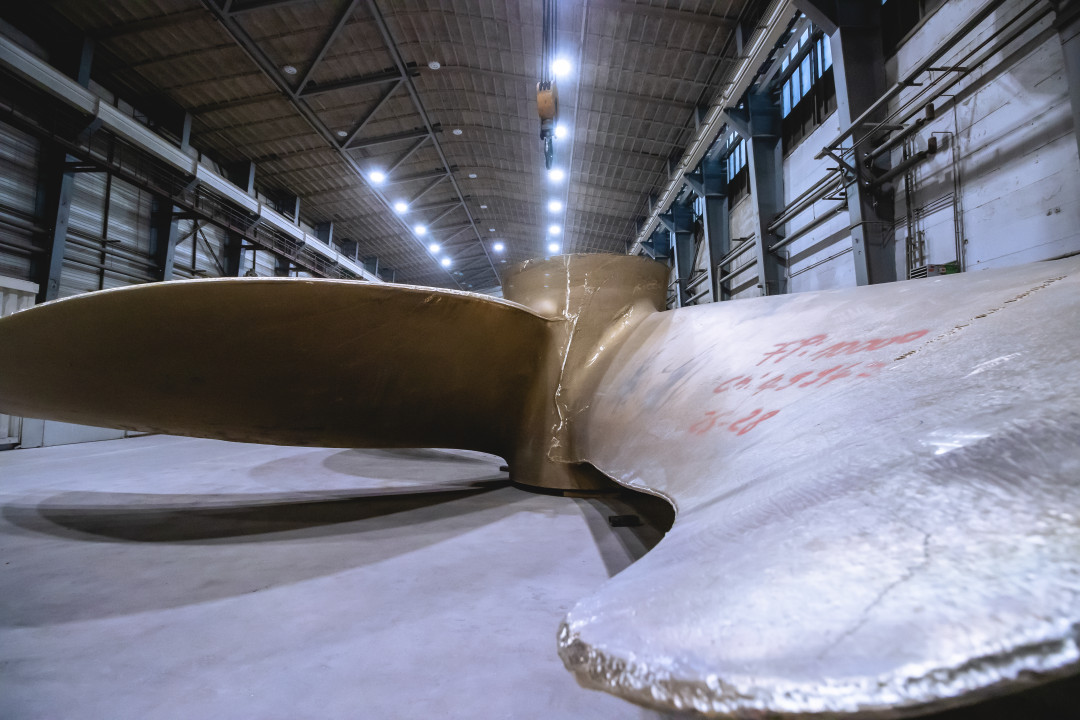
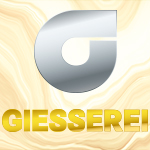
Die Mecklenburger Metallguss GmbH ist ein dynamisches Unternehmen, das sich auf die groß angelegte Produktion und den internationalen Vertrieb von Schiffspropellern spezialisiert hat. Mit einem Erfahrungsschatz von 75 Jahren zählt das Unternehmen zu den Global Playern und agiert erfolgreich unter den Top Ten der internationalen Propellerhersteller. Selbstbewusst richtet das Unternehmen seinen Blick in die Zukunft und erweitert sein Portfolio durch die Einführung neuer Produktlinien.
VON CHRISTIAN THIEME, HAMMINKELN
Etwa eine Autostunde südlich von Rostock entfernt liegt Waren, das Zentrum der Mecklenburgischen Seenplatte. Der Kurort, mit seinen rund 21.000 Bewohnern, grenzt an die Müritz, den größten innerdeutschen See. Der örtliche Hafen dient als Ausgangspunkt für zahlreiche Personenschiffe, die das Ufer der Müritz ansteuern und das ganze Jahr über Touristen in die Region locken. Obwohl Waren als ein maritimer Ort bekannt ist, realisieren viele Besucher nicht sofort, dass hier auch Schiffspropeller für die größten Containerschiffe der Welt hergestellt werden.
Seit 75 Jahren produziert die heutige Mecklenburger Metallguss GmbH (MMG) Schiffspropeller an diesem Standort. Obwohl der Standort auf eine noch längere Geschichte zurückblickt, entwickelte sich der maritime Fokus erst in der Nachkriegszeit. Im Jahr 1948 forderte die Sowjetische Militäradministration eine Erhöhung der Schiffsbaukapazität. Aufgrund der günstigen Lage nahe der Küste und des umfangreichen Know-hows mit qualifiziertem Personal wurde die Gießerei in Waren beauftragt, Gussteile für den Maschinen- und Anlagenbau sowie Propeller und Ausrüstungen wie Bullaugen und Lukenabdeckungen für den Schiffbau zu produzieren. Heute ist MMG ein international renommiertes Hightech-Unternehmen und zählt zu den weltweit führenden Herstellern von Schiffspropellern. Mit einem selbstbewussten Blick in die Zukunft strebt die Gießerei danach, ihre Position weiter zu stärken und zusätzliche Geschäftsfelder zu erschließen.
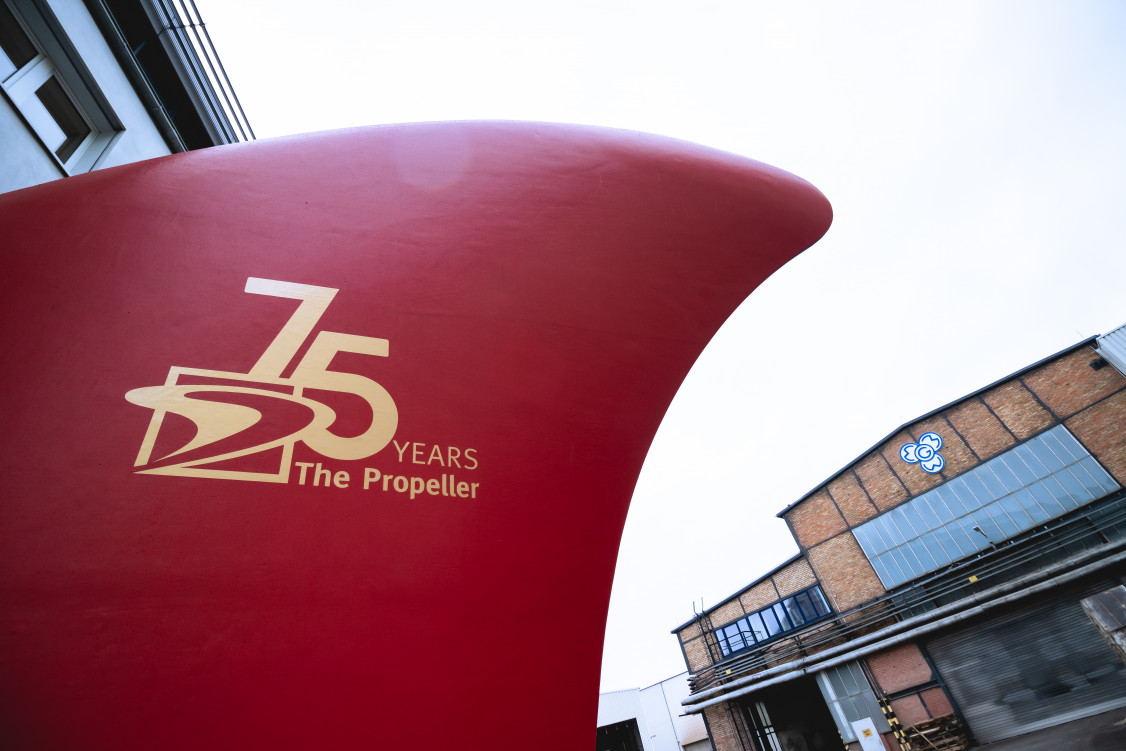
Das grüne Produkt zieht Mitarbeiter an
„Unser Jubiläum haben wir am 23.09.2023 hier am Standort gefeiert“, berichtet Dr.-Ing. Lars Greitsch, Geschäftsführer des Unternehmens. „Beim Tag der offenen Tür konnten wir über 3.000 Gäste empfangen und unseren Betrieb präsentieren“. Das Unternehmen befindet sich derzeit auf Wachstumskurs, ist stolz auf sein Know-how und beschäftigt knapp über 200 Mitarbeiter. „In den letzten 18 Monaten haben wir etwa 40 neue Mitarbeiter eingestellt und hatten keine personellen Engpässe“, fügt Greitsch stolz hinzu. Durch die Erschließung neuer Geschäftsfelder sollen zukünftig weitere Arbeitsplätze entstehen.
„Die Region bietet uns den Vorteil, dass wir nicht mit vielen Industriebetrieben um Mitarbeiter konkurrieren müssen, und wir haben ein herausragendes Produkt. Im Austausch mit anderen Unternehmen bemerken wir, dass junge Menschen eher in grünen Wirtschaftszweigen arbeiten möchten. Im Gegensatz dazu haben der klassische Maschinenbau und der Automotivebereich deutlich mehr Schwierigkeiten“, stellt Greitsch fest. Er führt dies auf den eigenen Beitrag zu einer umweltfreundlicheren Schifffahrt im globalen Maßstab zurück, insbesondere im Retrofit-Bereich.
Wachstumskurs dank internationale Regularien
In diesem Jahr nähert sich das Unternehmen der Umsatzmarke von 100 Millionen Euro und verzeichnet damit das zweitbeste Ergebnis seit 2015. „Die Geschäftslage ist positiv, da Reedereien weltweit unter Druck stehen, ihre Energiekosten und den CO2-Ausstoß zu reduzieren“, erklärt Greitsch. Dieser Druck auf die Eigentümer resultiert aus verschiedenen Faktoren. Gemäß den Richtlinien der International Maritime Organization (IMO), einer Sonderorganisation der Vereinten Nationen, müssen neue Schiffe bereits seit vielen Jahren einen Energieeffizienzindex (Energy Efficiency Design Index, EEDI) erfüllen. „Das bedeutet, dass jedes neue Schiff einen Zertifizierungsprozess durchlaufen muss, um sicherzustellen, dass die Effizienz bestimmten Standards entspricht. Dies wird beim finalen Modellversuch überprüft, bevor das Schiff gebaut wird. Darüber hinaus hat die IMO begonnen, auf Grundlage der gleichen mathematischen Grundlage den Energieeffizienzindex auf bestehende Schiffe zu übertragen, was zum Energy Efficiency eXisting ship Index (EEXI) geführt hat“, so Greitsch.
Im Jahr 2013 wurde in Waren das erste Retrofit-Pilotprojekt durchgeführt. Dabei werden beispielsweise alte Propeller gegen effizientere ausgetauscht oder durch effizienzsteigernde Maßnahmen ergänzt. Mittlerweile gibt es zwei verschiedene Regularien in diesem Bereich, die von den Reedereien eingehalten werden müssen. „Die IMO hat einen Index für alle größeren Handelsschiffe herausgegeben, der einmalig nachgewiesen werden muss und von den meisten Schiffen nicht erfüllt wird“, fasst Greitsch zusammen. „Oft reicht jedoch eine Motordrosselung aus, um die Grenzwerte einzuhalten“. MMG profitiert von der daraus resultierenden niedrigeren Endgeschwindigkeit, da für eine schnellere Fahrt effizientere Propeller erforderlich sind.
„Zu dem einmaligen Index kommt noch fortlaufend der Carbon Intensity Indicator (CII) hinzu“, ergänzt Greitsch. Der CII ist ein Maß für die Energieeffizienz eines Schiffes und wird in Gramm CO2-Emissionen pro Ladekapazität und Seemeile angegeben. Dieser wird nicht aus technischen Daten des Schiffes berechnet, sondern aus dem Treibstoffverbrauch, der mit der theoretisch möglichen Ladungsmenge ins Verhältnis gesetzt wird. „Es handelt sich also um eine Art Transporteffizienz“. Hierbei gibt es vier verschiedene Effizienzklassen. Schiffe mit der Kennzeichnung E müssen beispielsweise einen Maßnahmenplan vorlegen, der innerhalb eines Jahres umgesetzt werden muss.
Zusätzlich zu den international gültigen Regularien entsteht weiterer Druck durch Großkunden, die Endkunden beliefern. „Container werden beispielsweise von Unternehmen wie Amazon und Co. gebucht. Die Endkunden hingegen erwarten einen umweltfreundlichen Transport“, erklärt Greitsch. Die Folge: Die Reedereien müssen bessere Effizienzklassen erreichen, damit die Schiffe weiter gebucht werden. Der Geschäftsführer merkt jedoch an, dass der klassische B2B-Bereich wie Öltanker nicht so stark unter Druck steht.
Die Gießereien ziehen Nutzen aus den kontinuierlichen Verbesserungsprozessen. In der unmittelbaren Perspektive bieten sie Lösungen durch Retrofit-Projekte, während langfristig die Nachfrage nach neuen Schiffspropellern besteht. Derzeit liegt die Produktionsquote im Retrofit-Bereich in Waren bei etwa 60 Prozent, Tendenz steigend, wie Greitsch erklärt.
Jährlich verlassen zwischen 70 und 90 Propeller das Werk. Die Exportquote beläuft sich auf 95 Prozent, wobei zahlreiche Werften in Asien beliefert werden. „Für nächstes Jahr sehen wir eine weitere Steigerung. Bei der Entwicklung kommt es aber auch auf den Neubausektor an. Derzeit sprechen wir schon über Projekte die Ende 2024 und darüber hinaus beginnen. Wir hoffen, dass es dann konstant weitergeht“.
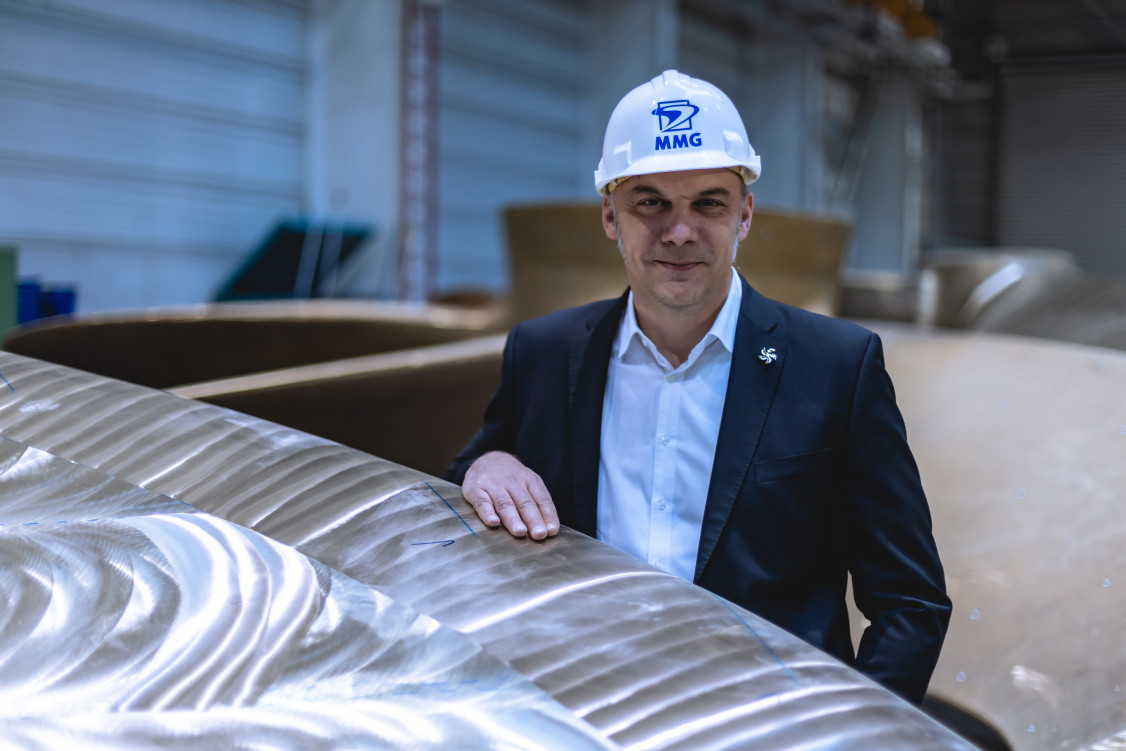
Die Schifffahrt im Umbruch
Effizienz ist das Schlüsselwort in der Branche. Neben den traditionellen Optimierungen am Antriebsstrang werden zunehmend unterstützende Antriebssysteme wie Flettner-Rotoren und Wingsails eingesetzt. Der Gießer ist jedoch sicher, dass sie den klassischen Motor nicht vollständig verdrängen können. Die Anforderungen an Manövrierfähigkeit und Redundanz in verschiedenen Schiffskategorien machen eine emissionsfreie Schifffahrt praktisch unmöglich. Neue Motoren, die mit synthetischen Kraftstoffen wie Methanol betrieben werden, sind daher besonders gefragt. „Maersk hat kürzlich das erste Containerschiff in Betrieb genommen, das den Betrieb mit Methanol ermöglicht. Weitere Schiffe sind bereits bestellt“, fügt Greitsch hinzu. Die geringere Energiedichte des Treibstoffs macht die Effizienz zum zentralen Treiber von Innovationen. MMG bringt sich heute bereits frühzeitig in den Bauprozess mit der eigenen Expertise ein.
Im Schiffsbau ist es üblich, einen Modellversuch mit einem maßstabsgetreuen Modell durchzuführen. MMG setzt jedoch bereits seit zehn Jahren Simulationen im Auslegungsprozess ein. „Die Simulation for Design (SfD) bringt viele Vorteile mit sich, da wir beispielsweise die negativen Maßstabseffekte aus dem Modellversuch nicht haben“, erklärt der Gießer. Durch den Einsatz von Simulationen verringern sich für den Eigner die Kosten erheblich, wenn es um Neubauprojekte geht. Greitsch verdeutlicht: „Für uns ist es besonders wichtig, immer das Gesamtsystem im Schiff zu berücksichtigen, insbesondere wenn Hilfssysteme den Antrieb unterstützen. Hier müssen wir viel Überzeugungsarbeit leisten, damit wir frühzeitig im Auslegungsprozess involviert sind, um eine optimale Effizienz zu erreichen“.
Herausforderungen am Standort Deutschland
Was den Standort Deutschland betrifft, sieht das Unternehmen mit Skepsis in die Zukunft. „Aktuell sind wir zwar auch von den steigenden Energiekosten betroffen, können diese aber an unsere Kunden weitergeben. Langfristig sehe ich jedoch Probleme, da es zu einem Standortnachteil wird“, konstatiert der Geschäftsführer. Das Unternehmen betrachtet besonders das Thema Schwertransporte mit Besorgnis. „Man muss ganz klar sagen, dass wir im Transportbereich ein Problem haben. Bei unseren Stückgewichten von bis zu 110 Tonnen werden einige sanierungsbedürftige Brücken für uns unpassierbar, und wir erhalten leichtherzige Absagen. Schlimmer noch ist, dass es keinen Zeithorizont gibt, wann relevante Brücken erneuert werden. Wir wünschen uns in dem Bereich eine deutlich lösungsorientiertere Zusammenarbeit“. Die Mecklenburger Metallguss GmbH liefert die Schiffspropeller überwiegend auf dem Landweg nach Hamburg, die von dort aus werden sie in die ganze Welt verschifft. Alternativ könnte das Unternehmen zwar über Rostock ausweichen, hierdurch entstehen jedoch hohe Zusatzkosten durch die Umladung – Kosten, die nicht jeder Kunde übernehmen möchte und den Preisdruck auf die Warener weiter verschärft, denn viele Konkurrenten sitzen direkt vor Ort in den asiatischen Werften.
Das Unternehmen hat keine Probleme mit Rohstoffknappheit, da es ein effektives Modell entwickelt hat: „Grundsätzlich haben wir den Vorteil, dass wir alle möglichen Schrotte verwenden können, da wir ein eigenes Labor haben und daher selbst legieren können. Bei den Mengen, die wir hier produzieren, bevorzugen wir am liebsten alte Propeller, die eingeschmolzen werden. Im Retrofit-Bereich verhandeln wir mit unseren Kunden, dass wir bei der Lieferung eines neuen Propellers den alten zurückbekommen“. Dieses Verfahren hat doppelten Nutzen: Der Reeder spart Geld und muss sich nicht um die Entsorgung kümmern. MMG übernimmt die Verschrottung und führt das Metall in das eigene Werk zurück, wo es wieder im Materialkreislauf verwendet wird. Durch den internationalen Legierungsstandard müssen die Gießer oft nur minimal nachlegieren, um die eigenen hohen Anforderungen zu erfüllen.
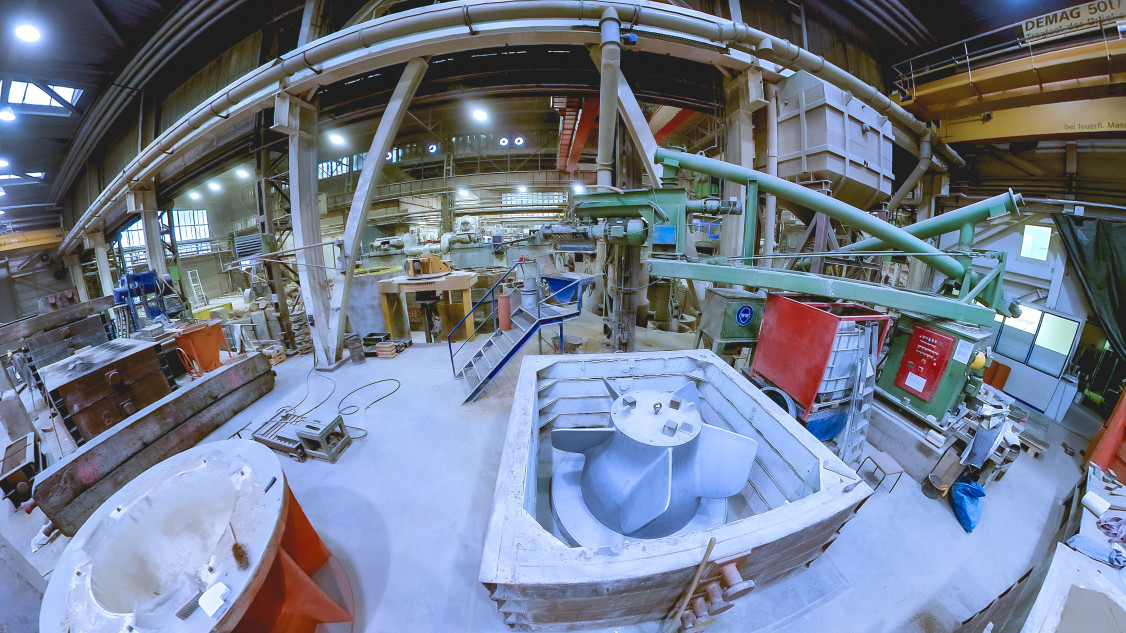
Additive Fertigung und neue Produktzweige
Neben dem etablierten Geschäft arbeitet MMG an zukunftsorientierten Projekten. „Zum einen werden wir in Zukunft Aluminium im Großguss anbieten. Im Schleuderguss haben wir viel Erfahrung gesammelt, jetzt erweitern wir unser Portfolio um größere Tonnagen. Zudem führen wir die additive Fertigung ein“, erklärt Greitsch. Die additive Fertigung beginnt mit kupferbasierten Werkstoffen und wird später Edelstahl und Aluminium umfassen. „In Zusammenarbeit mit einem Partner werden wir Edelstahlpropeller anbieten, die beispielsweise bei eisgehenden Schiffen notwendig sind“. Aber auch kleinere Propeller möchte das Unternehmen künftig zu besseren Preisen anbieten können und damit einen weiteren Markt erschließen.
MMG setzt dabei auf das Wire Arc Additive Manufacturing (WAAM)-Verfahren. Erste Modelle der Propeller wurden auf der Formnext in Frankfurt präsentiert (GIESSEREI 12/2023, Seite 26 ff.). „Die Herausforderung besteht darin, die Klassifikationsgesellschaften mitzunehmen, die das Produkt zertifizieren müssen. Mittlerweile gibt es eigene Abteilungen dafür, die sich mit additiver Fertigung auseinandersetzen. Wichtig ist, dass die Materialeigenschaften den Anforderungen entsprechen. Derzeit beschäftigen wir uns damit, den vollständigen Nachweis zu erbringen, dass wir diese Fertigungsmethode beherrschen“, erklärt Greitsch. Ein weiterer Meilenstein wurde mit einem Trinkbrunnen für den Kunden Hamburg Wasser erreicht. „Der Designer hat eine schöne Form mit innenliegenden Wasserkanälen entworfen“, so Greitsch. Die Herausforderung lag im organischen Design des im WAAM-Verfahren hergestellten Werkstücks. Der Trinkbrunnen erhielt eine besondere Erwähnung des Internationalen Designpreises FOCUS OPEN 2023 von Baden-Württemberg. Eine Fortsetzung mit ähnlichen Projekten ist geplant, da MMG in diesem neuen Geschäftsfeld weiteres Potenzial sieht.
Die Implementierung von Großrobotik ist ebenfalls in Waren in vollem Gange. In Zusammenarbeit mit dem Fraunhofer-Institut für Großstrukturen in der Produktionstechnik (IGP) in Rostock gießt und baut das Unternehmen einen eigenen Roboter, der später bei der Bearbeitung der Schiffspropeller eingesetzt wird. Greitsch betont, dass es dabei um den Aufbau von Know-how geht, das man später auch anderen Unternehmen zur Verfügung stellen möchte.
Durch die breitere Ausrichtung sieht sich das Unternehmen gut für die nächsten Jahre aufgestellt und blickt selbstbewusst nach vorne.
Schiffspropeller sind im wahrsten Sinne des Wortes Giganten. In Waren werden Propeller mit einem beeindruckenden Gewicht von bis zu 110 Tonnen und einem Durchmesser von mehr als zehn Metern hergestellt. Diese imposanten Modelle kommen später bei den größten Containerschiffen zum Einsatz. Das größte Containerschiffe weltweit bietet Platz für 24.000 TEU (Twenty-Foot Equivalent Unit). Hierbei steht TEU für das englische "Twenty-Foot Equivalent Unit" und bezeichnet einen 20-Fuß-Standardcontainer. International dient TEU als standardisierte Einheit zur Zählung dieser genormten ISO-Container. Um ein Schiff dieser Größe zu entladen, würden etwa 12.000 Lastwagen benötigt.
Schlagworte
Additive FertigungAluminiumAnlagenbauDesignEdelstahlEisenEnergieeffizienzFertigungGussGussteileKupferMaschinenbauMesseOrganisationProduktionRobotikSimulationStahlVertriebWerkstoffe