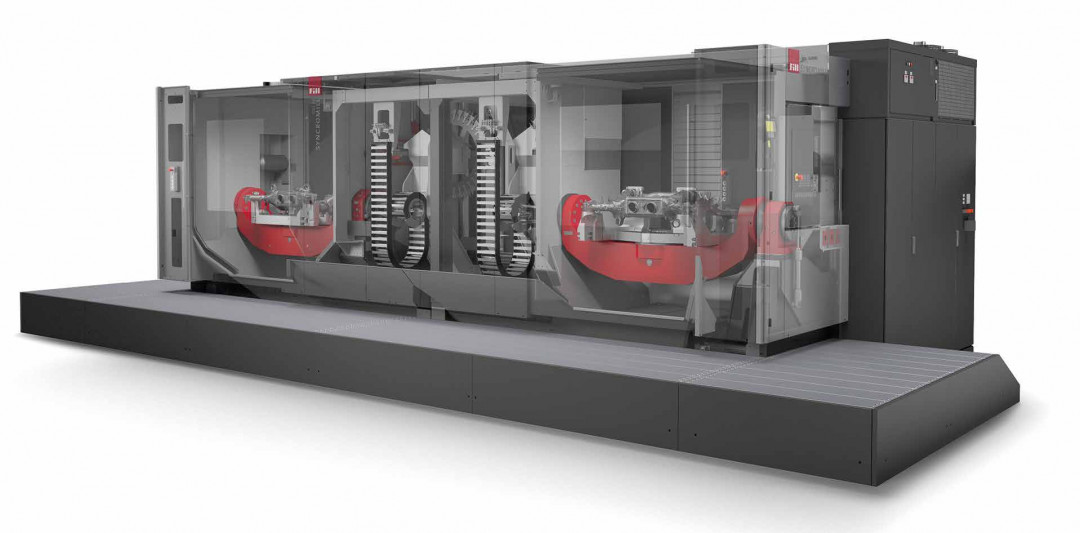
The innovative machine concept of the Syncromill series from Fill stands for high-precision and cost-effective machining of the most diverse and complex workpieces. From electric motor housings, axle carriers and battery trays to crankcases, spring supports and hinges - with its broad machine portfolio, Fill offers the ideal machining solution including the additionally required sub-processes.
The Syncromill D machining centre has two independent and large machining areas and is perfectly suited to the high-precision machining of large-volume giga and megacast structural components. Numerous configuration options - such as different rotary table combinations, tool interfaces or the expansion of tool stations - make the Syncromill D adaptable to individual customer or workpiece requirements.
The Syncromill D is also characterised by maximum flexibility. Loading and unloading can be carried out from above or from the front, either manually or automatically using robots or loading handling. This represents high added value when purchasing or designing the entire system. In addition to interlinking with upstream or downstream processes, the use of classic and innovative transport systems such as AGVs is of great importance for efficient implementation.
Automatic workpiece inspection using camera systems is also playing an increasingly important role in fully automated production systems. With Cybernetics Vision, Fill offers a range of industrial image processing solutions. The product range extends from simple 2D position detection, position determination or type checks to 3D component reconstruction and optical quality control of surfaces using self-learning algorithms that imitate the decisions of the system operator.
Further advantages of the innovative machine concept of the Syncromill series are the end-to-end processing - from design to production and commissioning of the workpiece clamping device - as well as the design of the machining tools. This enables the shortest possible commissioning times to be realised. A central contact person responsible for the entire system means fewer interfaces for the end customer and therefore a significant advantage.
The Austrian machine manufacturer Fill is the only company in the world able to supply all machining processes - from the moulded, machined, tested, welded and packaged workpiece - from a single source. Major fluctuations in workpiece geometries, materials, processes and quantities are currently presenting the entire industry with major challenges. In order to continue to be successful, these can only be overcome with short reaction times and flexible machine and system concepts.
See Fill's solution expertise for yourself and visit the machine engineering experts at EUROGUSS 2024.
FILL Gesellschaft m.b.H.
Fillstraße 1
A-4942 Gurten
www.fill.co.at
Hall 7A, Stand 123