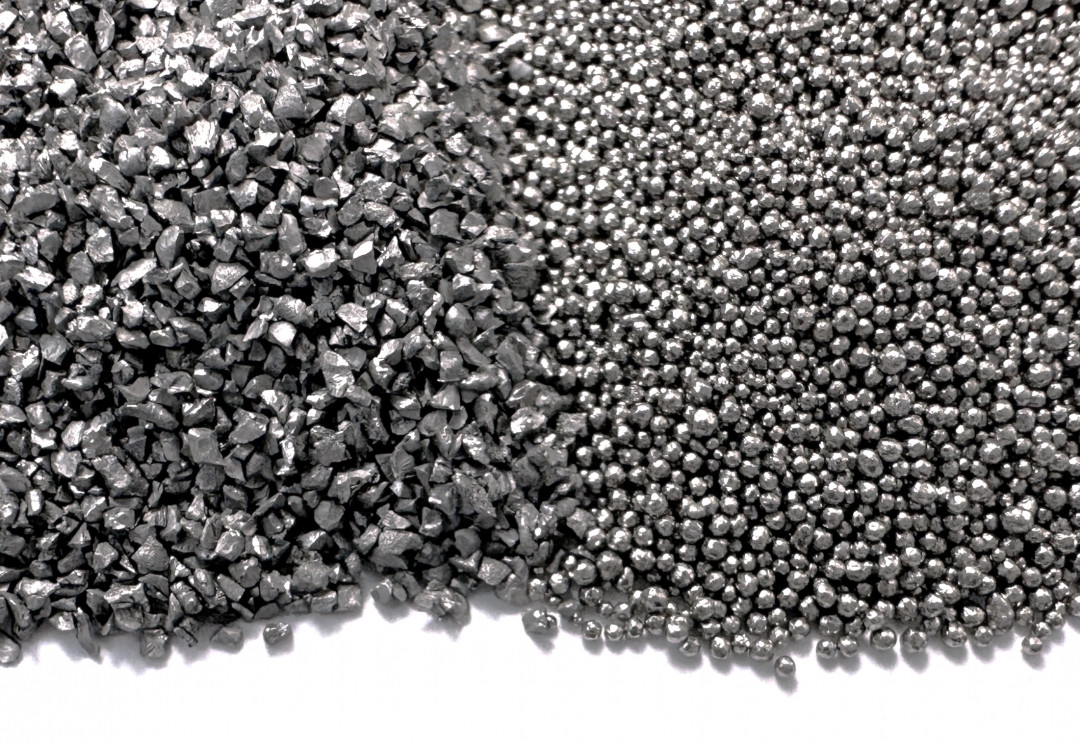
At GIFA 2023, Vulkan Inox, Hattingen, Germany, will showcase Chronital and Grittal blasting abrasives, which the company has been producing exclusively with renewable energy since 2022. This improves the eco-balance of its customers, because the blasting media they purchase brings a significantly smaller CO2 footprint. In addition, the reusable stainless steel blasting abrasives reduce consumption to just a few percent compared with mineral-based ones. Thus, when blasting metal workpieces, they make a significant contribution to the sustainability of production.
The stainless steel blasting abrasives are made from melted steel scrap and are completely recycled back into the metal cycle – a prime example of functioning recycling management. When used by customers it significantly improves the eco-balance, because they wear very slowly on impact with the workpieces and cycle again and again in a closed circuit. Vulkan’s blasting media reduces the amount of abrasives used to just a few percent of the quantities previously required compared with mineral materials.
The high dimensional stability of the individual stainless steel grains prevents the formation of dust and noticeably improves working and visibility conditions. In addition, their use reduces the amount of waste and the cost of disposal.
Christian Hoffmann, Sales Manager at Vulkan Inox, knows that his customers are making great efforts to reduce their own footprint. Once again, he sees his compavy as a pioneer in its industry: "We have made many adjustments: As a starting material, we deliberately buy secondary input materials with a low CO2 footprint . Since 2022, we have been operating our induction furnaces with electricity generated from renewable sources and implementing waste heat recovery to power the drying process. Overall, we have reduced CO2 emissions from our own and third-party energy sources (Scope 1 and 2) by 87 percent since 2018. This means we are conserving valuable resources. Our goal is to convert the entire process so that gas will no longer be required.“