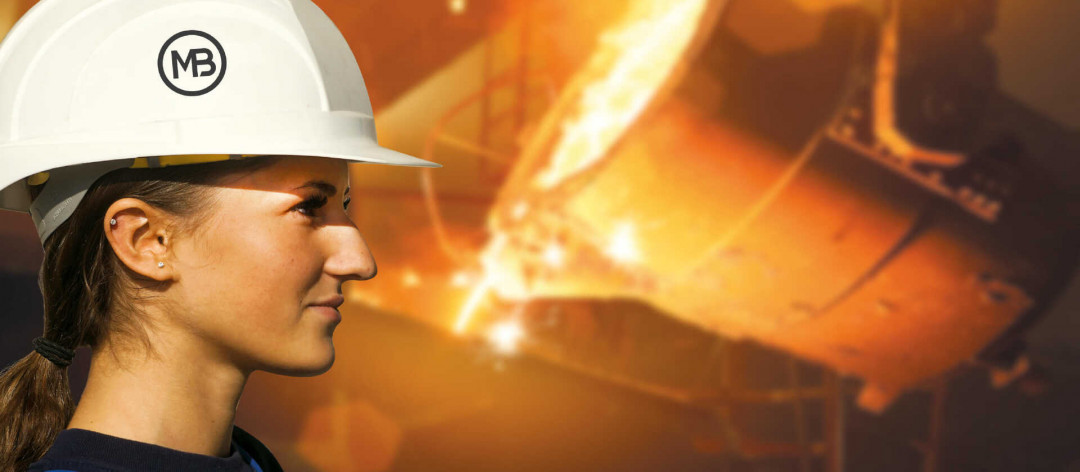
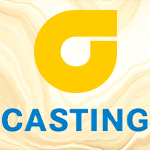
The family business M. Busch is constantly growing and modernising. New halls, high-tech automation and investments in the millions are the result of a modern corporate strategy. The company is focussing on ready-to-install and pre-assembled truck parts and is expanding its involvement in the railway sector. With a future-orientated mindset and extensive investments in production facilities and sustainability, the Sauerland-based company is facing up to current challenges and remaining competitive.
BY CHRISTIAN THIEME, HAMMINKELN
Due to their heavy weight, commercial vehicles require particularly powerful braking systems. A poor or defective brake system is highly dangerous, because no other component is as important for safety. When a truck makes an emergency stop, several tonnes of weight must be brought to a standstill as quickly as possible. This can only be reliably achieved with high-quality brake components - because in an emergency, every centimetre counts.
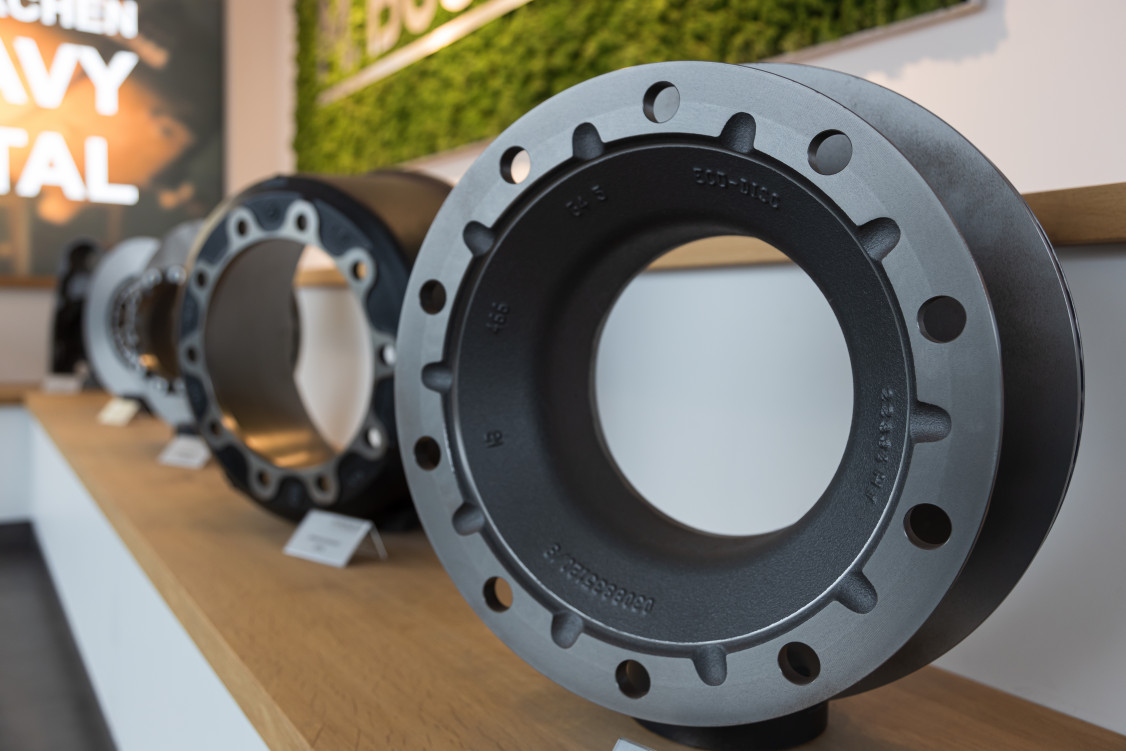
This is where M. Busch's special expertise comes into play: the medium-sized, family-run company has focussed on the truck sector as a large-scale foundry. This business segment accounts for a good 80 per cent. The focus is evenly split between trucks and trailers - each accounting for 50 per cent of the portfolio. The company mainly manufactures brake discs, brake drums and flywheels for trucks and stationary engines. The remaining 20 per cent are products for construction and agricultural machinery and, in future, an increasing proportion of brake discs for rail vehicles. Andreas Güll, Managing Director of M. Busch GmbH & Co. KG, emphasises the strategic decision: "We entered the railway business a year and a half ago. We have dealt intensively with the topic, recognised the rail sector as a growth market and set the course accordingly." Currently, 6,000 brake discs for the railways leave the plant every year, and forecasts show a significant increase to around 100,000 units in the next five years.
Investments for the growth course
You can see from afar that construction is underway on the company premises in Bestwig. Fences are being erected, new car parks are being built and a new hall was even opened a few months ago. The busy Ruhr Valley cycle path runs right on the edge of the company premises, as the Ruhr flows through the valley just a few hundred metres away. The history of the company, which today has two sites in Bestwig and Meschede-Wehrstapel, 4.5 km away, and has developed into an internationally active company in the automotive industry, began in 1830 in the immediate neighbourhood. However, time has by no means stood still at this location. Behind the hall facade, automation and high-tech dominate.
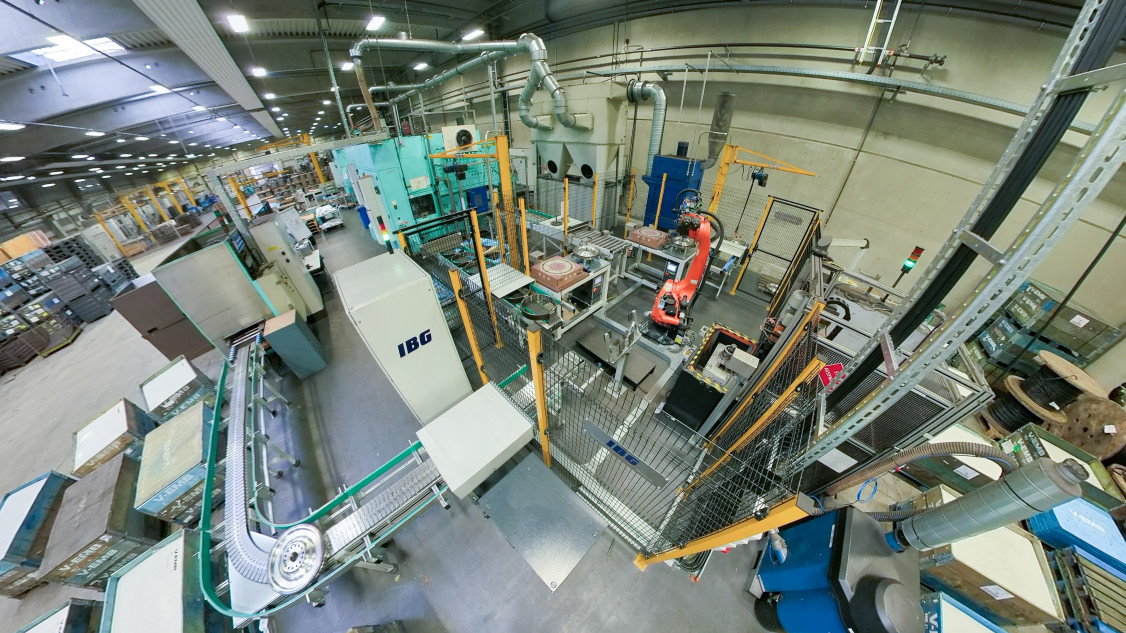
M. Busch relies on a future-orientated corporate strategy, which is proving to be a solid foundation for the company's current success. Güll emphasises the importance of this approach: "In the past, only simple annual planning was carried out. We have done away with this and replaced it with a multi-year planning model". Five years ago, the Sauerland-based company initiated the pioneering five-year strategy "MB 2022", the success of which now forms the basis for the next strategy cycle "MB 5.0 Next Level", which is scheduled to run until 2027. This comprises 34 projects spanning all areas of the company. The new strategy enables M. Busch to react more flexibly and in a more targeted manner to developments in the truck sector. For the company, however, strategic planning means more than just investment planning. It also includes defining visions, goals and values, with a particular focus on transparency towards employees. "This is well received by the employees, as they recognise a perspective for the future. Goals are created that everyone can orientate themselves by," states Güll.
The strategy cycles involve high investment costs. Over the past five years, the company has invested almost 30 million euros in its infrastructure. "That's enormous for a company of our size," emphasises Güll. Three additional processing lines and a new hall were built at the Bestwig site. This expansion necessitated the construction of an additional logistics hall, which was recently put into operation alongside a new loading hall. The new logistics hall now offers space for the temporary storage of 2,300 pallets of finished products. In addition, three picking stations have been created to prepare lorry loads. Three lorries can be loaded simultaneously in the new loading hall, which both reduces waiting times and increases the company's flexibility. A total of 4865 m² of additional hall space has been created in this way, which can also be used as production space in the future.
As part of the ongoing expansion and modernisation work, the surrounding company premises are also undergoing a comprehensive redesign. The waiting lorries will be relocated to a new waiting area, which will avoid blocking the adjacent Ruhr Valley cycle path in future. In addition, new car parks are being created and massive investments are also being made in safety. The entire area will be fenced off and access will be secured using special systems, also as a prerequisite for TISAX certification.
"The new production line is part of our strategy," states Güll. "We want to further expand our added value, i.e. we don't just want to mould, but also machine and pre-assemble more and more parts ready for installation." This orientation is aimed at increasing the vertical range of manufacture and thus reducing dependence on pure casting orders. Güll emphasises that with a simple raw part there is a risk that orders can be relocated more easily. However, this risk is minimised if the company invests in machining and pre-assembly and supplies fully machined cast parts. In the case of the production line, M. Busch has signed a ten-year contract with Volvo. It is an additional order for the production plant in Bestwig, while the raw part has been produced in the foundry in Meschede for years. Both plants will benefit from the contract, as the raw part will be cast in the Sauerland region for another ten years. "However, the production line not only represents an increase in capacity, but also the new benchmark in terms of productivity, automation, energy efficiency and quality for this product family," adds Güll. The high degree of automation is based not only on standardised production processes, but also on an individual concept that includes robots as well as monitoring and camera systems. Güll explains further: "One employee per shift produces 360,000 truck brake discs on this system in 3-shift operation without any manual work, machined ready for installation, pre-assembled, checked and packaged ready for dispatch - no one else can do that apart from us".
M. Busch believes it is well positioned with regard to the increasing spread of electromobility. "We have a share of around ten per cent of our turnover that will be affected by e-mobility in the future," says Güll. Despite the ongoing development of electromobility, the company's focus remains on the production of brake drums and brake discs. These components are also essential for electric vehicles, as they are still needed despite recuperation.
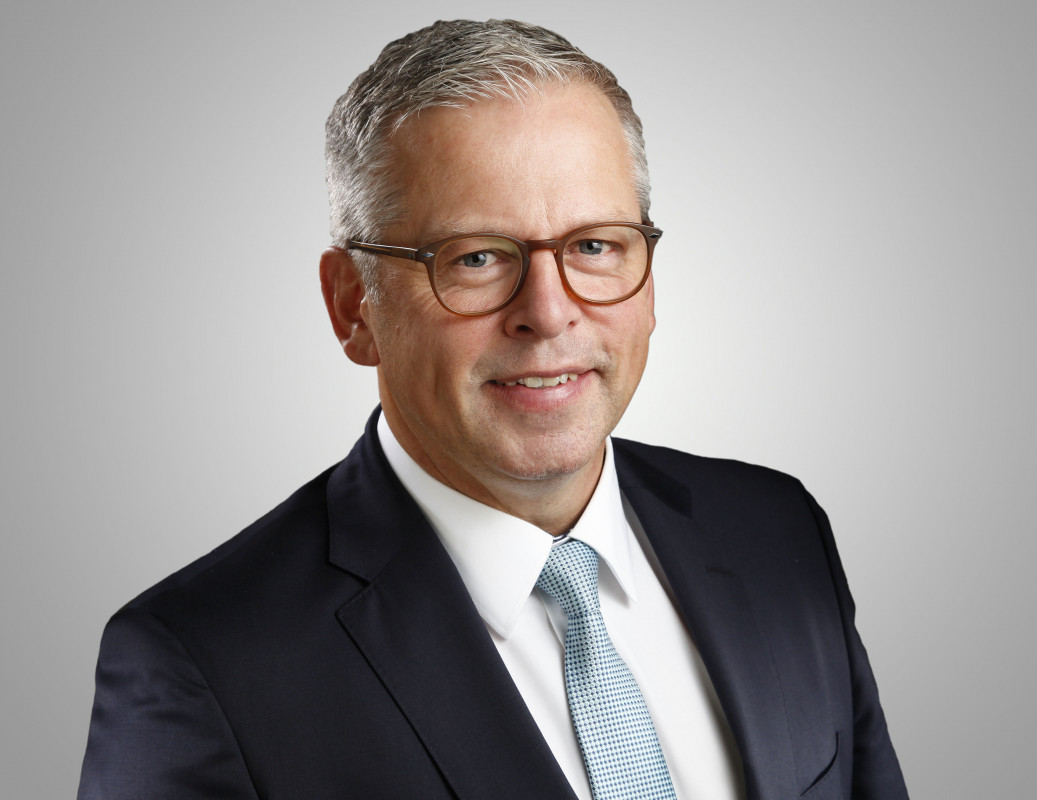
Depth of added value as the key to success
Güll is particularly proud of the high proportion of value added, which in his opinion is an "absolute speciality" on the market and means future security for the foundry. "Following the investments made at the Bestwig plant over the last five years, we now produce 82 per cent of our castings completely ready for installation and partially pre-assembled." The company wants to increase this proportion even further. A flywheel line is currently being built for this purpose. Many truck manufacturers still process castings themselves. However, as soon as space or investment is required, companies like M. Busch have the opportunity to get involved in machining and assembly.
The company has also invested at its site in Wehrstapel - 56.6 million euros in the last ten years. The focus of current investments is on automation, increasing productivity and sustainability aspects. "On a production line where brake discs used to be packed, palletised and strapped by employees, the area is now completely unmanned and automated," says Güll. This development shows how the company is using technology to increase the efficiency and modernisation of its operating processes.
Following the completion of the new halls at the Bestwig site, work continues on the roofs. The new photovoltaic system, which will be installed on three hall roofs, will cost 1.2 million euros. An output of 1122 kWp will later be achieved on an area of 6800 m². Güll: "That sounds enormous, but for the plant in Bestwig it accounts for just 13 per cent of the energy requirement. For the company as a whole, it's just 0.8 per cent." In a thought experiment, Güll makes it clear that seven wind turbines with a total output of 6 megawatts with continuous wind would be required to supply the entire company with electricity around the clock, six days a week.
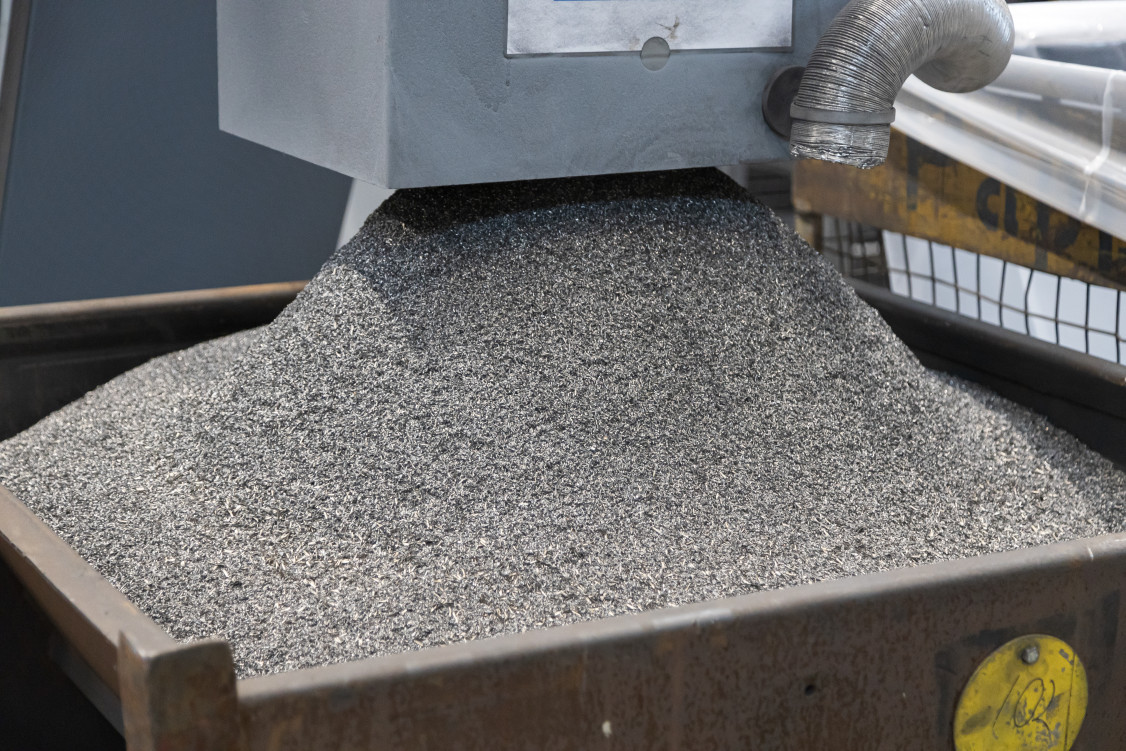
Energy supply also plays a central role for M. Busch in future competition. The company currently uses a cupola furnace as its main melting unit, but additional induction furnaces could take over the process completely in the future. Fortunately, the company is not experiencing any grid connection bottlenecks - an advantage over some other regions in Germany. "Electricity prices and grid fees are a major problem," summarises Güll. The company currently spends 16 million euros a year on energy, compared to around ten million euros two years ago. M. Busch sees the savings potential mainly in the processes upstream and downstream of the actual melting process. "Of course we utilise this, it's day-to-day business in energy-intensive companies. It reduces energy consumption a little, but only a little". The company sees itself competing mainly with Poland and Turkey, as energy prices there are only half as high as in Germany. According to Güll, this could become a problem for the company, particularly when negotiating new contracts.
"The energy price must be brought to an internationally competitive level, by whatever means, and this must be long-term and predictable," summarises Güll. "The recently agreed 'electricity price package' is unfortunately just another bubble for energy-intensive SMEs; for us, it does not mean any relief, but rather a further increase in electricity costs by a high six-figure amount due to the rise in grid fees. We hope and need a significant re-regulation in order to stop the de-industrialisation caused by artificially generated, uncompetitive electricity prices." Despite this situation, M. Busch is confident about the future and is taking personnel precautions to meet the challenges ahead.
Creating attractiveness
The slogan "We make heavy metal" is emblazoned on the company's lorry tarpaulins and is part of M. Busch's campaign for young talent. In terms of employees, the company believes it is currently in a good position, but is working strategically to ensure that this remains the case. "We enjoy a good reputation in the region," says Güll. "Last year, we held an open day in Bestwig for the first time. There were over 1000 visitors, including many from other areas in the neighbourhood. When they saw our production facility, many were impressed by the level of automation. That's all advertising for us." The combination of attractive pay and positive word of mouth has paid off for M. Busch. All twelve apprenticeship places for 2023 have been filled. However, it also means a great deal of effort for M. Busch. The company has invested in the creation of a new position specifically dedicated to social media and public relations. In addition, two full-time training coordinators were hired who "speak the language of the trainees". The use of eye-catching trade fair stands, giveaways and new iPads for the trainees complements the company's commitment. M. Busch makes targeted use of social media for corporate communication, with Facebook and Instagram being used for trainee marketing and LinkedIn specifically for the B2B sector and for addressing managers.
There are no major staff fluctuations at M. Busch. "Most of the trainees stay here," explains Güll. "The second largest proportion goes into further training." At the same time, Güll emphasises the importance of the performance principle in the company: "There are also trainees who only get a temporary extension or no extension at all. But those who perform well can develop within the company." The system seems to work, as former employees who have gained experience elsewhere in the industry also come back. "For us, these are of course the best communicators," says Güll happily.
Sustainability
A glance into the production halls shows that M. Busch is also well advanced in terms of automation technology. There are only a few employees to be seen between the encapsulated production islands. Everything in these cells is completely automated, in some cases invisibly. Even activities such as forklift truck movements are facilitated by computerised systems. Radio chips under the hall floor define storage locations and storage areas. This is made possible by a sophisticated manufacturing execution system (MES). The Sauerland-based company has brought together a total of over 80 machines from different manufacturers and with different control systems. "This system allows us to take a close look at production and obtain valuable information," explains Güll.
The M. Busch iron foundry processes 130,000 tonnes of iron every year, using a combination of cupola and induction furnaces. A comparison with other iron foundries in North Rhine-Westphalia shows that M. Busch achieves remarkably lower CO2 emissions per tonne. Güll explains: "This is the result of a mixture of technology, processes that we have created around the technology and, ultimately, our managers and employees." The company recognised the potential for energy savings early on and, in addition to internal measures, also took part in the InnoGuss project (see info box) run by the BDG. "An important factor is our low reject rate, which leads to significantly lower energy requirements," adds Güll. Added to this are measures such as heat recovery in the cupola furnace for water heating and the drying furnaces. The foundry is currently well positioned with the cupola furnace. "A purely electric melting operation doesn't just have advantages for us, because we would need significantly more energy in the overall process, as heat recovery would be significantly lower with the new furnaces." Currently, the process heat generated is only utilised internally. Theoretically, some of the residual heat could be utilised externally to further increase efficiency. Although there are currently no talks with the city, Güll is certain that such issues will soon be discussed as part of the municipal heat planning process. However, by then it could already be too late, as there is already a concept for converting to e-melting operation, which shows that heat would then no longer be available for other consumers.
Awareness of environmental issues, especially the CO2 footprint, plays a key role for companies in the automotive casting industry, such as M. Busch. In order to manage its CO2 footprint more effectively, the company has become involved in the FRED (Footprint Reduction Tool, see info box) project. Güll explains the importance of this step: "The advantage is that the system is universal. We had previously started to determine the CO2 footprint ourselves, but this is a complex topic. With FRED, comparability is now guaranteed, which is an absolute advantage". Güll is convinced that calculating the CO2 footprint will soon become standard practice for all companies in the industry. However, he emphasises that the availability of all relevant data from the operating areas is a challenge, especially for smaller foundries, as the structure for data collection must first be developed.
M. Busch's commitment in various areas, including sustainable corporate management, has led to positive feedback and confirms that the company is on the right track. Bestwig is optimistic about the future and ready to take on new challenges. This emphasises the need for companies to continuously develop and adapt to change.
InnoGuss
The "InnoGuss" project aims to develop innovative transformation paths specifically for foundries in NRW and derive the relevant technical, economic and political framework conditions. The project is being coordinated by the Federal Association of the German Foundry Industry (BDG), supported by BDG-Service GmbH and the VDEh-Betriebsforschungsinstitut (BFI).
www.guss.de/innoguss
FRED
FRED stands for Footprint Reduction Tool, which foundries can use to determine the carbon footprint of their products and their company - and thus also develop a decarbonisation strategy for their operations. The software complies with the rulebook of the OEM platform Catena-X and is certified in accordance with Gutcert and DIN EN ISO 14067. FRED can also be used to identify process- and site-specific CO2 reduction potential and as a basis for a company's decarbonisation strategies. An absolutely unique feature of the CO2 calculation tool is also a reference database with real industrial data on energy and material consumption www.fred-footprint.de