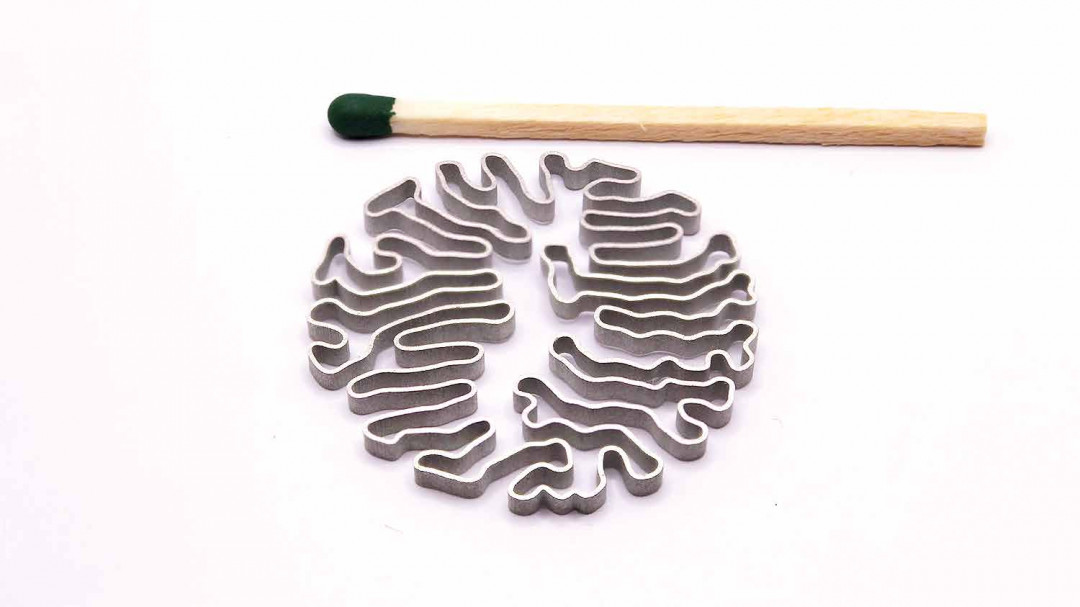
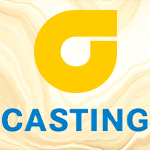
Additive manufacturing (AM) is often perceived as competition by users of traditional manufacturing processes, including micro casting (a form of investment casting). While investment casting has been established for many years for complex metallic components, AM technology has experienced an impressive upswing in recent years. But are these production methods really in competition with each other or should they rather be seen as complementary technologies?
BY SONJA KAPPLER, CHIARA ARMBRUSTER, ANDREAS BAUM, KNUT HEITZMANN, CARLO BURKHARDT
Manufacturing processes for small and micro metallic components
In the field of additive manufacturing, there are only a handful of processes that are suitable for the production of small, high-precision metal components. The direct 3D printing process micro laser melting (M-LPBF), in which metal powder is melted and welded layer by layer with a laser, has the limitation that support structures are required for overhangs, which are costly to remove, and the process is less efficient and economical than the sinter-based, so-called indirect processes, even for higher quantities due to the energy consumption and spot processing.
Sinter-based AM technologies, which are also relevant for small components in the investment casting size range, include metal binder jetting (MBJ) and lithography-based metal manufacturing (LMM), which utilise a two-stage process. In the first phase, a green part is printed with a high proportion of metal powder material. The green part then undergoes a debinding and sintering process in which the binders used in the printing process are removed by thermal treatment.
The sinter-based processes offer new possibilities for overcoming geometric and qualitative limitations, particularly in the production of small components with outstanding detail accuracy and surface quality, and can also represent an interesting alternative to conventional tool-based production for small series and medium quantities thanks to economies of scale. In addition, the LMM process does not require any support structures, for example, and therefore less manual reworking of the component. Compared to the MBJ process, the LMM process is characterised by a higher resolution and therefore better precision and surface quality. The LMM process is therefore the preferred process for components with an edge length of less than approx. 40 mm, while the MBJ process is more economical for larger components (Fig. 1).
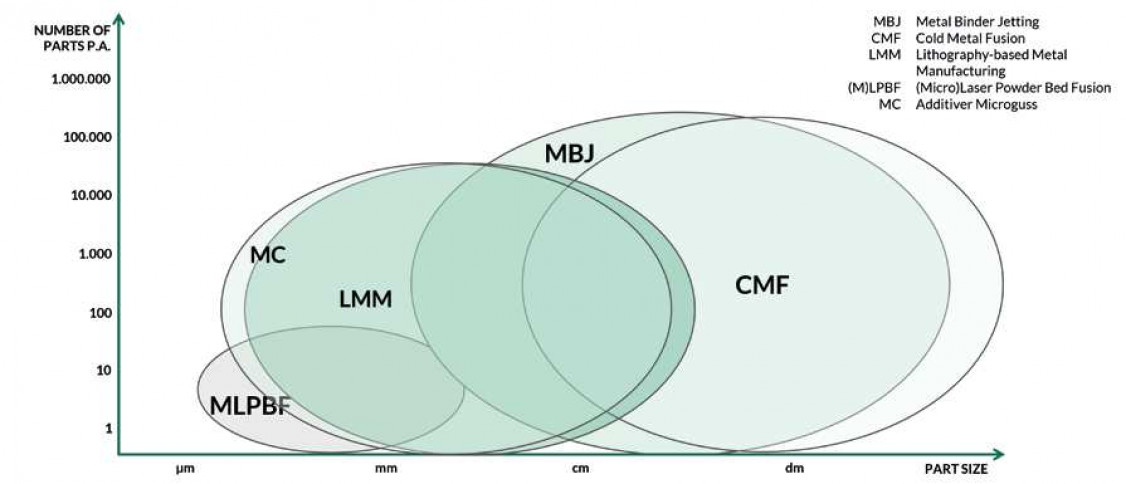
In traditional manufacturing, investment casting processes or metal injection moulding (MIM) are often used to produce small, complex components. As MIM is often only economical for larger quantities in the four- to five-digit range due to high mould costs, many users use additive micro casting, a modified investment casting process specifically for the smallest components, for smaller quantities and prototypes.
As both LMM and additive micro casting are suitable for small to medium annual quantities and complex geometries of small metal components, it is necessary to compare the advantages and limitations of the processes in order to make the best possible decision for the respective component (Fig. 2).
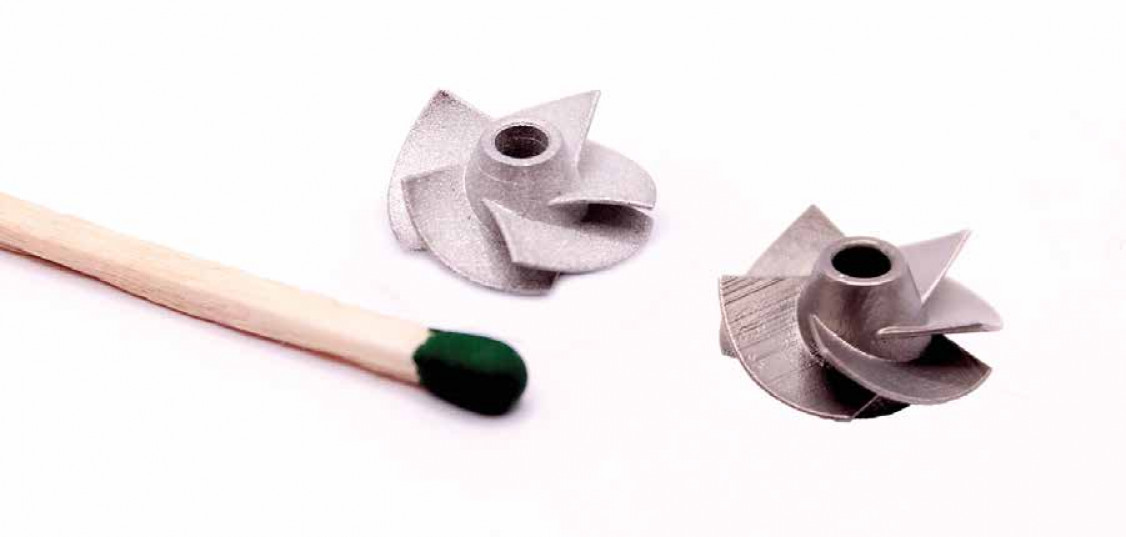
Surface quality
Surface quality is of crucial importance for many applications. As 3D printed models made of wax are usually used as lost models in additive micro moulding for prototypes and small series, the stair-step effect is often still visible in the cast final component. In addition, blowholes can form in the sprue area, meaning that surface defects can occur in this area. Overall, an Ra of up to 6 μm is achieved with additive micro moulding after casting. Subsequent vibratory grinding, blasting and polishing can improve the surfaces to an Ra of up to 1 to 2 μm.
With LMM technology, the surface quality without post-processing is an Ra value between 2 and 3 μm. Surfaces of up to 0.4 μm Ra can currently be achieved with comparable surface processing methods such as additive micro moulding. In terms of surface quality, LMM technology therefore has a process-related advantage over additive microcasting, although this is heavily dependent on the post-processing method selected.
Tolerances and resolution
Another important criterion for selecting a suitable technology is precision and which tolerances can be maintained. Nonnenmacher GmbH's additive microcasting process achieves tolerances of between ±0.1 mm and ±0.03 mm, depending on the size of the component. As both additive micro moulding and the LMM process have to deal with component shrinkage due to thermal process steps, the tolerances must always be understood as a function of the component size. The tolerance class table according to ISO 2768 is therefore also suitable for categorisation, where additive micro casting can serve the classes ISO 2768-m to ISO 2768-f. With MetShape's LMM technology, tolerances of up to ±0.05 mm can be achieved, although this also depends on the component size and involves multiple iteration stages due to the complex thermal process control. In general, classes ISO 2768-m or ISO 2768-c can be expected for the first prototypes. When carrying out a small series or series application with LMM, an oversize correction then enables a tolerance of ISO 2768-f. In the area of tolerances, additive micro moulding therefore shines with a higher accuracy for initial prototypes, which can only be achieved with LMM after several iteration stages. Thanks to the high resolution of both processes of between 15 and 35 μm, components with a very high level of detail can be realised (Figure 3).
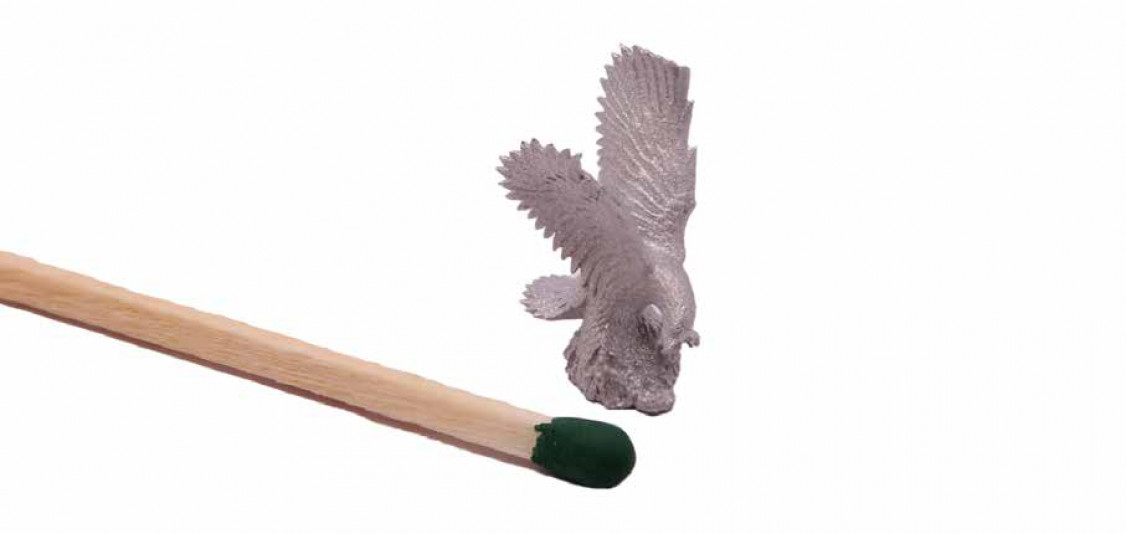
Fine structures and thin wall thicknesses
Wall thicknesses from 0.1 mm can be produced with both processes. However, feasibility depends heavily on the length and height of these wall thicknesses. With additive micro moulding, mould breakage can occur when embedding the 3D-printed model, while with the LMM process, very thin wall thicknesses can break during cleaning. When using very delicate structures, the stability and connection to the component body is therefore crucial for successful realisation (Fig. 7).
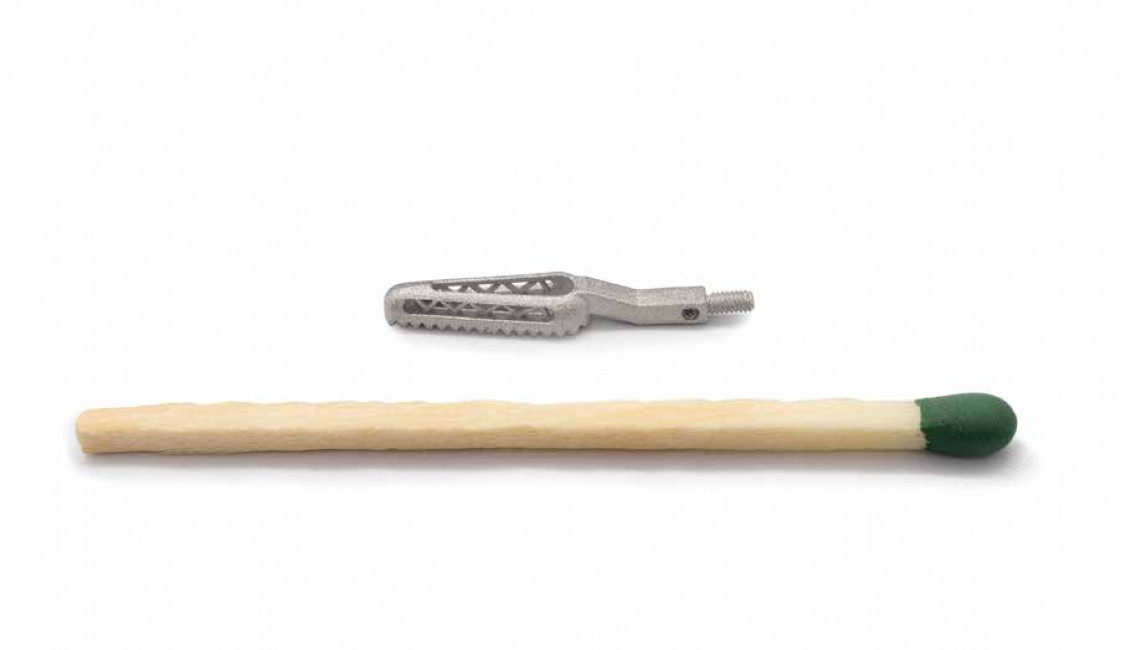
One of the biggest challenges of LMM technology is distortion during sintering, which can occur particularly with very thin webs. Components such as those shown in Figure 4 can be produced with minimal deformation using additive micro moulding, whereas with LMM technology this would only be possible with subsequent straightening of the component. In contrast, components with fine wall structures such as those in the lead image are preferably produced using LMM technology, as the application of sprues and the material flow are very difficult to realise using additive micro casting.
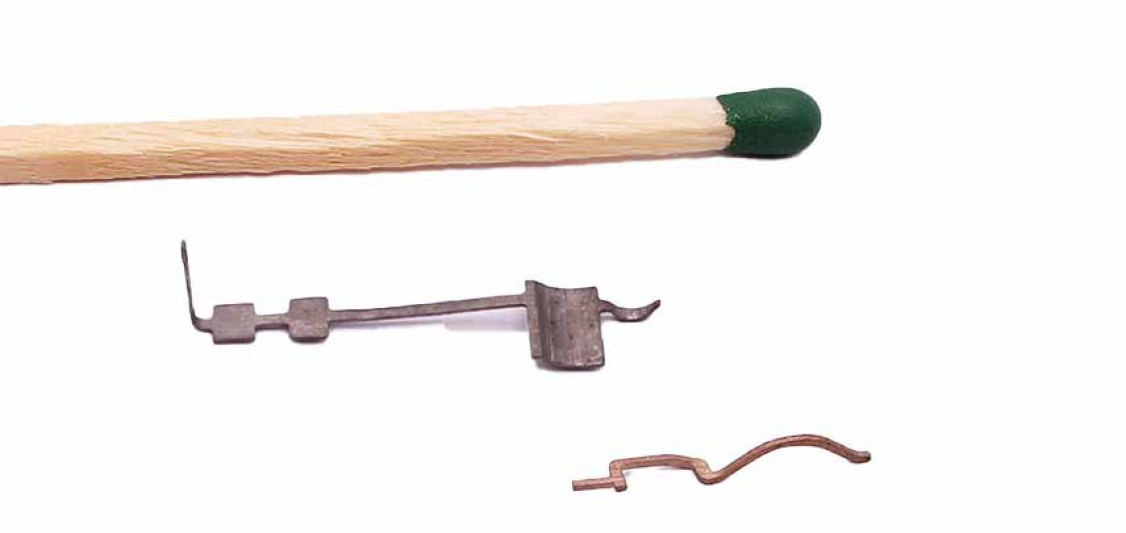
Variety of materials
In terms of material diversity, investment casting offers a wide range of materials from copper-based alloys to aluminium and austenitic stainless steels. In general, all metals and alloys with a melting temperature below 1500 °C can be processed. There are greater restrictions in the area of indirect additive manufacturing. As the processes are still very new and utilise a binder, i.e. additives made of wax and polymers, which have to be removed in a debinding and sintering process, the effort involved in material development is very high. So far, the new LMM process can be used to offer 316L and 17-4 PH stainless steels. With its expertise in the thermal process step of the indirect process chain, MetShape is playing a central role in material development in cooperation with the Institute for Strategic Technology and Precious Metals at Pforzheim University (STI) and Incus GmbH, the 3D printer manufacturer. Part of this cooperative work includes the qualification of titanium grade 5 and precious metals such as gold, as well as the shape memory alloy Nitinol.
Internal channels
In additive micro casting, the challenge with components with internal channels is that the channels of the model can easily break off when embedded in the mould. The possibility of realising internal channels, for example for cooling tools, is one of the aspects in which the new additive manufacturing processes score highly (Fig. 5). As the LMM process can completely dispense with support structures during printing, it is possible to produce the channels with functional fidelity, unlike other additive manufacturing processes. However, the feasibility of corresponding cooling structures depends heavily on the diameter, length and angle of the channel, as in LMM technology the residues of the binder-powder mixture are removed in a rinsing process.
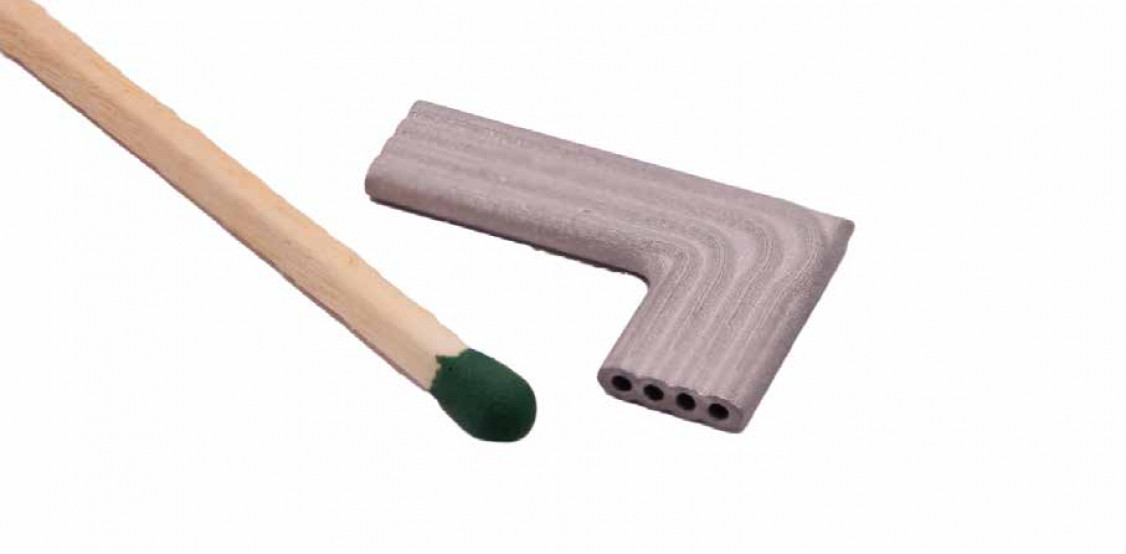
Function integration and assembly substitution
One of the main features of both technologies is that they enable function integration and assembly substitution for complex components (Fig. 6).
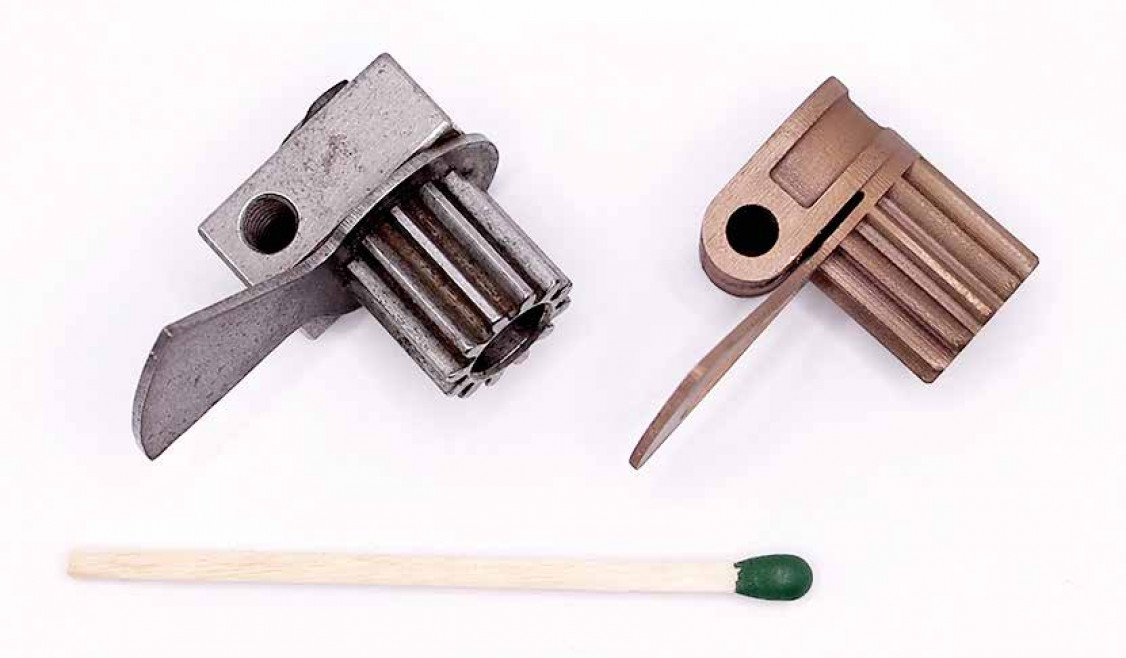
This allows the cost of manufacturing individual components and subsequent assembly to be reduced by producing a complex component. An example of this is the application in Figure 8.
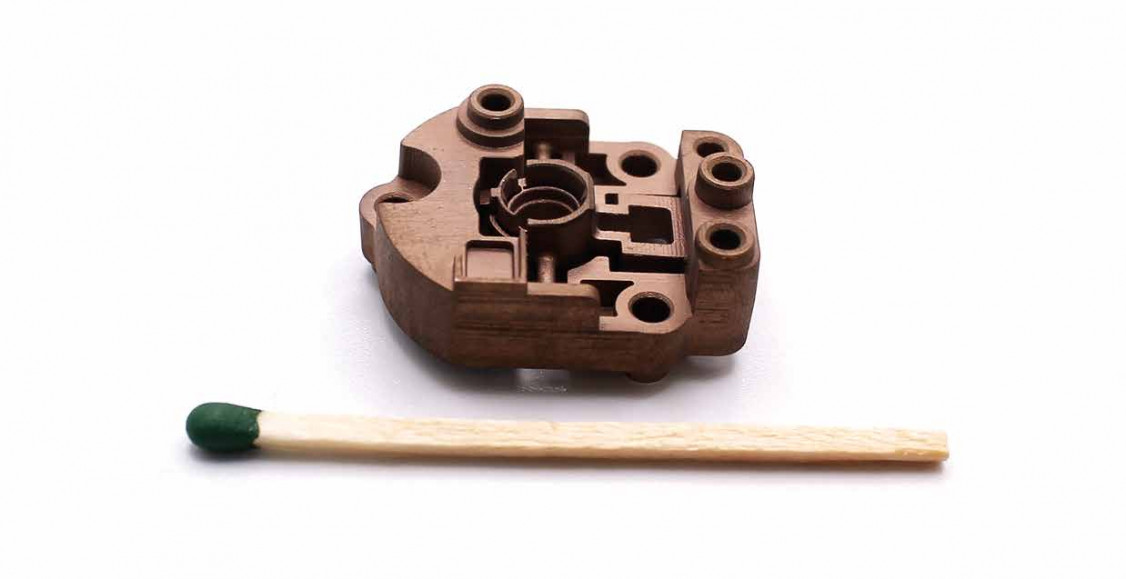
The development of this mount for a laser measuring device was covered with additively manufactured components until all functionalities were available. Among other things, two clip functions are integrated for holding the laser and a torsion spring for its adjustment. After validating these components, a mould was produced for mass production.
Overall, both sinter-based additive manufacturing with LMM technology and additive micro-casting enable the production of complex small and micro metal components in small quantities. Both processes have strengths and weaknesses, which is why the decision as to which process is more suitable must be made on an application-specific basis. If the factors of tolerance or material variety are already decisive for the first prototypes, additive micro casting is preferable. If the surface quality is decisive or very complex structures are involved, the LMM process is recommended.