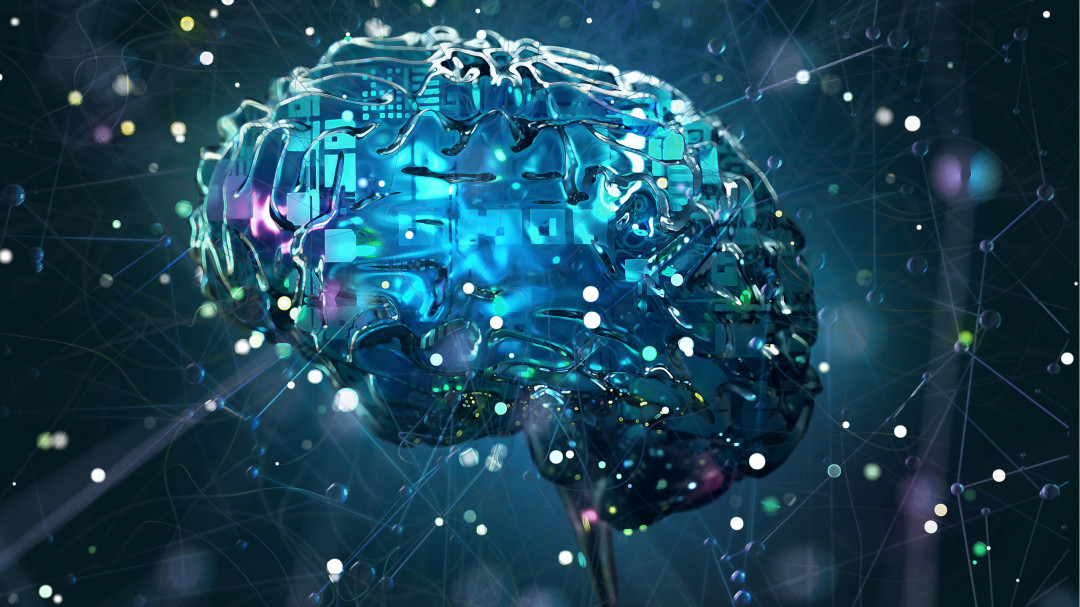
How can complex production systems be integrated into a networked value creation system and new digital manufacturing concepts be developed for an ecologically sustainable foundry industry? A consortium from science and industry is addressing this question in the joint project "ReGAIN". The Federal Ministry for Economic Affairs and Climate Protection (BMWK) is funding the project for three years with a total of around 8.2 million euros.
The ReGAIN project aims to digitally link foundry production systems in order to increase efficiency, flexibility, resilience and sustainability. The aim is to integrate complex production systems into a comprehensively networked value creation system and to develop new digital production concepts for an ecologically sustainable foundry industry in line with the "European Green Deal" updated in 2021. ReGAIN will lay the foundations for a digital product passport to be standardised for each foundry product and made available in Catena-X. Catena-X is an international, open data ecosystem for the automotive industry that optimises business processes through data-driven value chains.
Traceability of components in the casting process and use of AI
The sub-project of the Institute of Production and Information Technology (IPI) and the Laboratory for Optical 3D Metrology and Computer Vision (3dvisionlab) at Kempten University of Applied Sciences addresses challenges specifically in the sand casting process. The technologies to be developed are intended to guarantee complete traceability of cast parts and integrate them into quality management, which enables effective linking of process and quality data. This will enable data-based process optimisation and visualisation. In addition, AI-based assistance systems will visualise the effect between process parameters and quality characteristics and provide preventive recommendations for action for operating personnel. The models and methods developed are intended to serve as benchmarks in the field of process digitalisation and also support other manufacturing industries. The Federal Ministry for Economic Affairs and Climate Protection (BMWK) is funding the sub-project with around 640,000 euros for three years.
The research consortium of over 20 partners includes the IPI - Institute for Production and Information Technology at Kempten University of Applied Sciences, the University of Kassel, Braunschweig Technical University, the Federal Association of the German Foundry Industry, several Fraunhofer Institutes and various partners from the automotive industry, software development and materials technology.