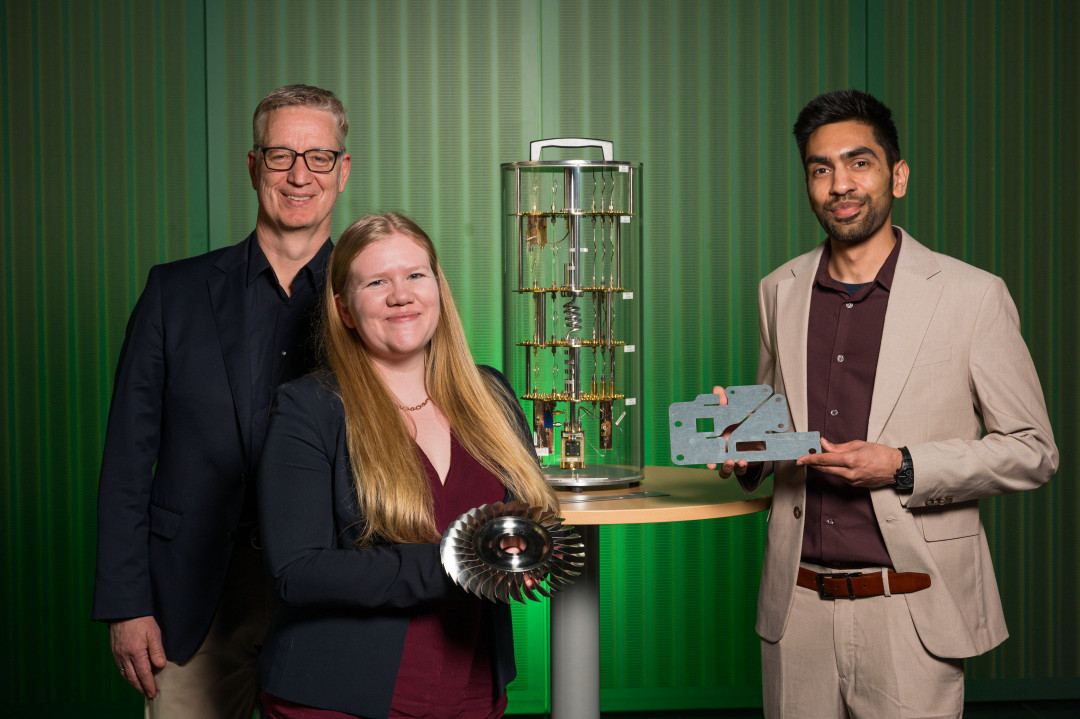
Metal components in perfect shape without rejects and faulty production: the computing power of quanta should optimise production in the metalworking industry in the near future. The team of business informatics specialist Wolfgang Maaß at Saarland University and DFKI is working with partners from science and industry in the "Quasim" project on simulations that still fail today due to computing time and memory limits. The research team will be demonstrating how its processes can improve the quality, productivity and cost-effectiveness of manufacturing at the Hannover Messe from 22 to 26 April (Hall 2 Stand B10).
Precision is required in the construction of aircraft turbines - after all, this part of the engine has to provide the right thrust and withstand adverse conditions. The blade wheel, which looks like a fan and later draws air into the turbine with its intricately curved blades, is milled out: Excess metal is removed. A complicated endeavour. This is because milling sometimes involves movement. If the process with its many adjusting screws does not run absolutely smoothly, a blade begins to oscillate and the vibrations cause the milling machine to cut into the metal. This is an expensive mishap for a component that becomes unusable due to the smallest inaccuracies. "Such production errors are critical for engine manufacturers, they lead to high costs," says Professor Wolfgang Maaß, business information scientist at Saarland University, who heads the Smart Service Engineering research group at the German Research Centre for Artificial Intelligence (DFKI).
Industry and SMEs are experiencing a similar situation with countless metal components - including those that are cut out using lasers. The extreme heat generated in the process can cause the metal to expand in places where it should not. Or parts fall off, get stuck and the machine comes to a standstill. Here too: Rejects and production downtime - material, time and money are lost. "The metalworking industry is one of the most important economic sectors in Germany and the EU. Safety and quality requirements are high. In production, you live with a reject rate of around one per cent - that doesn't sound like much, but in total it is a major factor for competitiveness," explains Wolfgang Maaß.
The solution is simulation. Digitalisation and artificial intelligence can help. A digital twin of the workpiece could be used to simulate everything that happens later in the real component: from planning and production to quality assurance. Everything could be run in a controlled manner, with all the parameters optimised one hundred per cent, from the perfect speed for milling to the precise power of the laser. - But there is a catch: the computing requirements of such high-resolution simulations are gigantic due to the masses of data and bring today's computers to their knees. Quantum computers, which would have the necessary computing power, are not yet ready. The result: "Simulations are rarely used in practice. This is because the computing requirements are too high and because a large amount of very specific data and information is needed, which also requires highly specialised expertise," explains doctoral student Hannah Stein from Maaß's research team. Industry and SMEs are therefore content with rough estimates for the digital twin and rely on the experience and expertise of their specialists in production and manufacturing.
There is still a long way to go before quantum computers ignite the "warp drive" for the lightning calculation of large amounts of data. But what the research partners in the Quasim project are working on is not a dream of the future. The partners from science and practice are working on harnessing the power of quanta for simulation in manufacturing in the short and long term. "Our initial investigations have shown that quantum mechanical functional principles and quantum-based machine learning can solve algorithmic problems better and significantly faster," says project coordinator Wolfgang Maaß. "Although today's quantum computers are still in their infancy, their technologies can already be used where conventional computers reach their limits and take an immense amount of time to calculate," explains the business information scientist.
The researchers are trialling various quantum computing methods in order to speed up the simulations and make them suitable for practical use. To this end, they are combining conventional simulation methods such as physical material science models and mathematical equation systems with quantum computing technologies. They are also investigating quantum-based machine learning methods. They compare their approaches with conventional methods, test the various solutions against each other in parallel and develop innovative solutions that could be used in the near future. To this end, they are integrating their results into existing simulation methods. "We are developing the first prototypes for this. Hybrid models in particular, which combine the various methods, quantum technologies and machine learning, are proving to be very promising based on the results so far," says researcher Hannah Stein.
The scientists use data from real production in everything they do. For example, engine manufacturers will soon be able to use quantum computer-aided simulations to predict blade vibrations during milling and, thanks to a digital twin, precisely adjust parameters such as the speed of the milling machine so that no inaccuracies cause rejects. And thanks to simulation, the laser also cuts perfect metal components with the right heat and processing sequence. At the Hannover Messe, the Saarbrücken-based business IT specialists will be using the example of milling and laser cutting to demonstrate how conventional manufacturing can be supplemented by quantum-based simulations, thereby speeding up processes and improving quality.
In QUASIM, short for "QC-Enhanced Service Ecosystem for Simulation in Manufacturing", Wolfgang Maaß's research group at Saarland University and the German Research Centre for Artificial Intelligence (DFKI) is cooperating with Professor Frank-Wilhelm Mauch's group at the Jülich Research Centre and Saarland University, the Fraunhofer Institute for Production Technology (IPT), the machine tool manufacturer Trumpf, the software component provider ModuleWorks and the associated partners Ford and the engine manufacturer MTU Aero Engines. The Federal Ministry for Economic Affairs and Climate Protection and the German Aerospace Centre (DLR) are funding the research with a total volume of over five million euros.