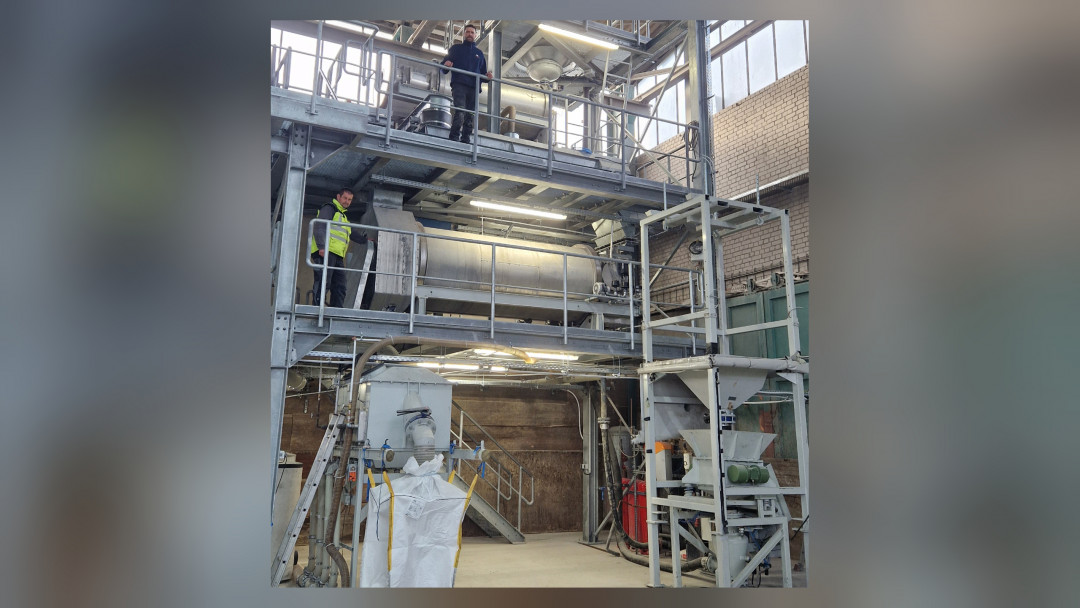
FSP, Stuttgart, Germany, has commissioned a pilot-scale reclamation plant for water-glass bonded sands. The plant is based on a wet reclamation process patented by Deantec. This process is highly energy-efficient and close to carbon-neutral.
Foundries spend a great effort and considerable financial means on reclaiming foundry sands and core sands containing organic- or inorganic binder systems. Especially against the backdrop of the dramatic rise in energy prices, energy efficiency of reclamation processes has been moving increasingly into the focus. The patented process used by FSP reduces the energy required to dry the sand by about 60 % and what’s more, it is carbon-neutral. With this process, foundries can substitute some 95 % of their new sand requirements, reducing the costs of used sand dumping at the same time. The reclaimed product has the same quality as new sand. As an alternative option, FSP also supplies a basic-grade product that can be flexibly blended with new sand to achieve the sand quality specified by the customer.
With this process, all common water-glass bonded foundry sands and special sands from 3D printing can be completely reclaimed. In the patented drying system, the sand is not dried with air but by turning the water it contains from liquid into gas. For this, energy recuperated from the condensation process is used to the greatest possible extent. By recuperating more than 60 % of the condensation energy, the evaporation energy is kept within the system. In addition to this, dust particles are removed from the sand in a patented fluid bed cooling separator. The process water is treated and maintained within a closed circuit. One ton of sand generates just 12 liters of waste water. Only this amount of fresh water has to be added to the process. Also during the distillation process, condensation energy is recovered. 95 % of the energy required for the evaporation process is energy recuperated from condensation. The distillate is entirely demineralized. Thus, it is even better suited for the sand washing process than fresh water.
In addition to the sale of the plants, FSP offers an operator model. Within this framework, the company processes used sand of most different origins in its own plants near foundry locations and returns a regenerate tailored to the customers' processes to the foundries. Plants on the company premises of individual customers are also possible. In both cases, FSP GmbH is the operator.