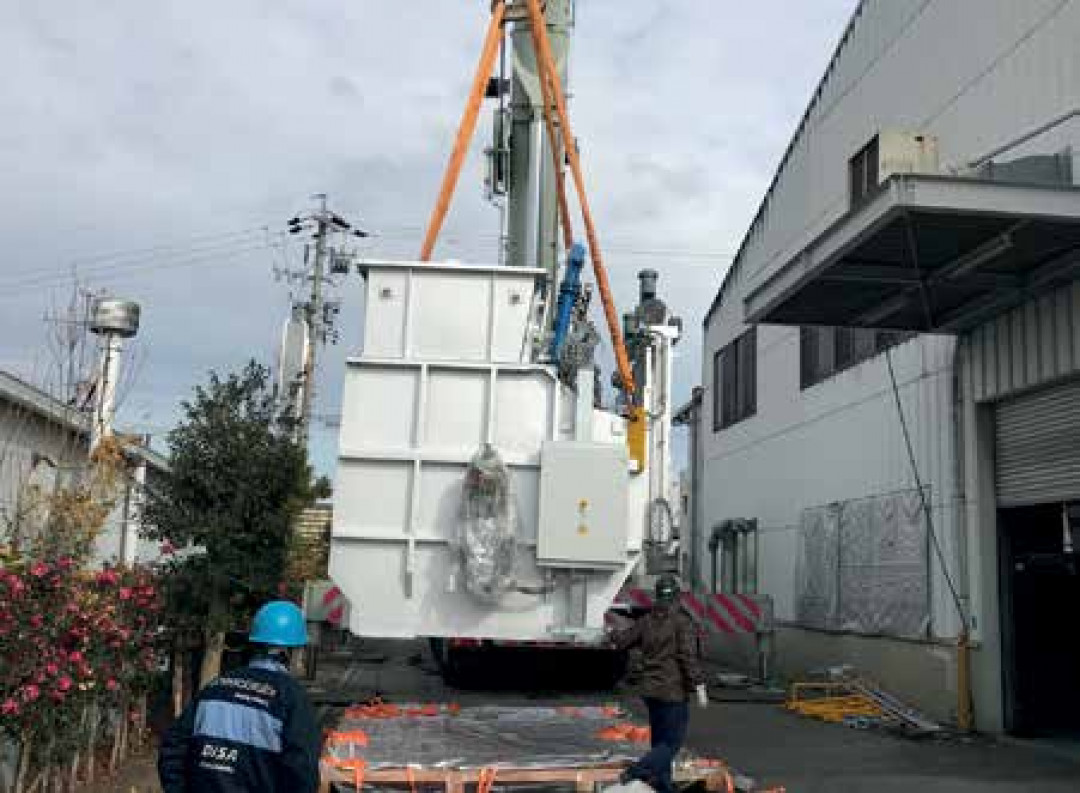
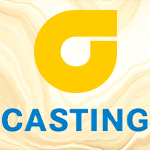
Read an article from CP+T 01/2020. Hattori Diecast has become the first Japanese company to order and install a
StrikoMelter melting furnace from StrikoWestofen.
Peter Reuther, Striko Westofen, Gummersbach
Eyeing efficient growth
Established in 1963, Hattori Diecast produces automotive parts for major brands including Toyota. The family run business specialises in aluminium parts such as computer housings, air-bag sensors, sump valves, accumulators and cylinders. Located near to Nagoya, the company has more than 100 employees.
Unsatisfied with a melting furnace that had been in operation at its plant for 15 years, Hattori ecided to decommission it and began looking for a new furnace that would support its growth and productivity ambitions and reduce key monthly melt shop costs, from gas consumption to maintenance.
The team at Hattori were familiar with StrikoWestofen through the Westomat dosing furnace already operating in the factory, and also thanks to its wider reputation in Japan where over 400 dosing furnaces have been sold.
With an additional understanding of the local insight and support offered by Norican Group which has operated in Japan for over 30 years – and keen to gain a march on competitors by seizing the advantages of world class technology, Hattori invited StrikoWestofen to tender for the project.
A trip to China – seeing is believing
Hattori was impressed with StrikoMelter’s technical credentials, in particular its ability (thanks to clever shaft geometry and special burner technology) to combine preheating, heating and melting processes in one furnace shaft to maximise efficiency and minimise metal loss.
Happy with performance on paper, the team was keen to see their proposed new furnace – a StrikoMelter 1 MH II-B 4000/1500, in person. The result? A trip to China. During the visit, Hattori could see the furnace’s performance in live operating conditions and received a show and tell of its PLC. The results impressed and the decision was made.
Capitalising on Norican expertise
Before the installation even began, Hattori experienced the benefit of working with the wider Norican Group. For example, a limitation on the transport of goods exceeding 45 tonnes within Japan meant that complex permissions needed to be obtained. These were secured thanks to Norican’s on-the-ground expertise. In fact, Norican’s detailed knowledge of Japanese government financial support structures also reduced the initial cost of Hattori purchasing the melting furnace. Norican went on to provide on-theground knowledge, logistical support, engineering expertise and warehousing space for parts for the duration of the project.
Two weeks to a cleaner, leaner melting process
Project constraints meant StrikoWestofen had just over two weeks (16 days) to complete the installation which included the removal of the old machine and sintering. Four engineers worked together on the project fulltime. The installation work began with the removal of the old furnace and the craning in of the new StrikoMelter. These tasks required sections of wall and the factory roof to be taken out and rebuilt during windy, rainy and even snowy December conditions. Impeccable project coordination combined with the team’s dedication meant this was all completed within a week.
Another logistical challenge was the size of the Hattori plant, which at 10,220 m2 is small for an aluminium foundry. With parts of the plant remaining in operation, the installation team had to work around staff, which was made difficult by the limited space. Overcoming all challenges, the melting furnace installation and refurbishment works were completed on time. As soon as equipment was operational, the team at Hattori received qualitative training on how to use the StrikoMelter. To ensure high-performance is maintained, Norican will visit Hattori every week for the first 3 months to monitor each status and optimise performance.
Transforming operations - and the bottom line
Hattori immediately felt the impact of its investment. Overall, the StrikoMelter has halved furnace-related energy costs thanks to a 43% reduction in gas consumption and the cutting of metal loss from 6% to just 2% when compared with the previous melting furnace. It isn’t just these headline figures that are pleasing Hattori. The company has benefitted from less cleaning and its engineers have been able to conduct more maintenance in-house, such as replacing the air fan filter and checking the bath temperature.
Mr. Sasaki, Casting Department Subsection Leader at Hattori Diecast said: “Remaining a leader means investing in the very best technology, so when looking to replace our melting furnace, we wanted a machine that would keep us at the forefront of diecasting – globally. “While the savings unlocked by our new StrikoMelter speak for themselves, it is also important to note that the quality of parts and simple operation of the machine both exceeded our expectations. We would like to thank Norican Group for ensuring a smooth installation and for helping us to streamline our business.”
Yoichiro Sakai, OEM sales, Norican Group, Japan said: “The results that Hattori is benefitting from will not go unnoticed by Japanese foundries. The StrikoMelter offers huge performance gains that cannot be ignored. We look forward to helping many more Japanese operators to seize the benefits of market leading StrikoMelter technology.”