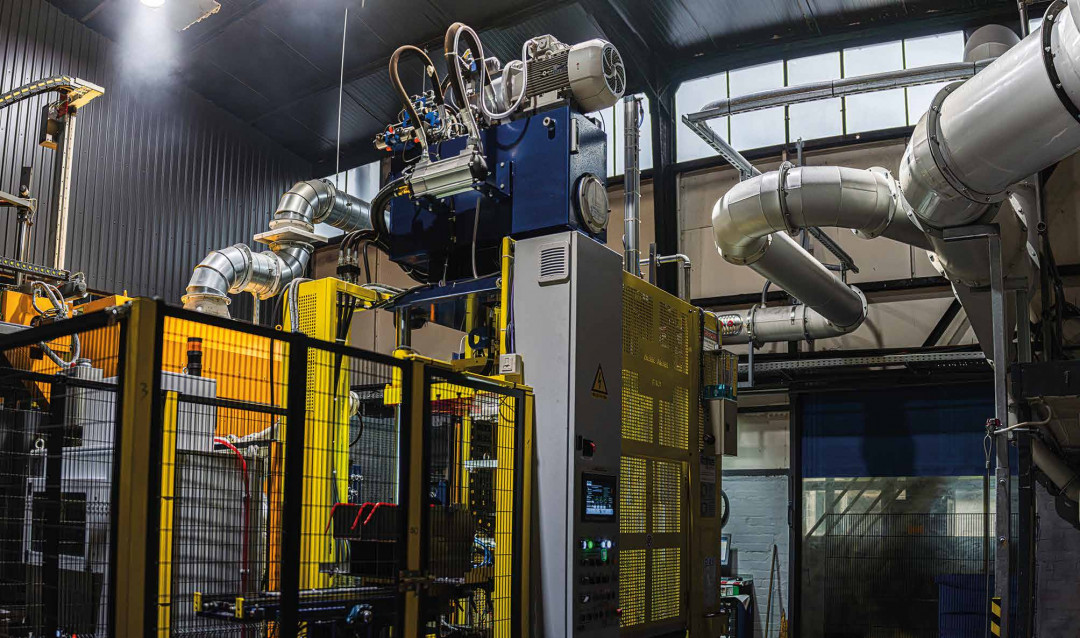
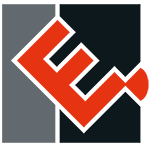
The last few years have not always been easy for the foundry industry. It started with the pandemic and was exacerbated by the Ukraine conflict and some of the associated effects. Energy became a scarce commodity and supply costs continued to rise steadily.
There is now talk of one of THE crises in the die casting industry. Not so at Matthies Druckguss GmbH & Co. KG. The medium-sized company, which has been established on the market for almost 70 years, has used the last few years to reorganise itself in many areas. In addition to infrastructural changes and optimisations, the company has also invested heavily in plant technology. Over the last two years, the owner-managed company has invested more than 1.2 million euros in the restructuring of its in-house die-casting foundry. This included not only the replacement or expansion of casting machines and the associated peripherals, but also drastic energy savings. Thanks to improved drive technology and optimised melting and holding technology, electricity costs were reduced by almost 40 %. The basis for all considerations was not only capacity expansion, but also ways to achieve greater sustainability in production.
A special extraction system also cleans all the air in the foundry and, in addition to improving the indoor climate, above all minimises emissions in the air. The separated substances are removed after filtering and can be disposed of separately.
"We are aware of our responsibility towards nature," says Marco Matthies, Managing Partner of Matthies Druckguss GmbH & Co. KG and continues: "My personal ambition is to show the world that a production company, and a foundry in particular, can also break new ground towards CO2 neutrality!". He is supported in this endeavour by a young and highly motivated management team.
But the development does not stop there - Matthies Druckguss has further goals: Further measures are planned for the coming years, for example, heat recovery from melting processes is to be pushed more strongly and thus utilised energetically for the building supply without hindering the melting process. There are also further opportunities for improvements in the melting and holding process. The possibilities of converting the melting furnaces from fossil fuels to the use of green hydrogen are currently being explored. Matthies Druckguss is working closely with a specialist company on this.
All types of packaging required for shipping the finished cast parts are currently being converted to sustainable solutions. The aim is firstly to be free of plastic in the packaging and secondly to only use packaging that can be used multiple times.
The company's carbon footprint has improved significantly as a result of the measures implemented. And the success speaks for itself: the reorganisation has enabled Matthies Druckguss to win new markets and customers and strengthen its market position. Customer awareness has changed and is now more focussed than ever on the environment and its preservation. Because sustainability concerns us all!
Matthies Druckguss GmbH & Co. KG
Bredstedter Street 29 - 31
24768 Rendsburg
www.druckgiesser.com
EUROGUSS: Hall 9, Stand 347