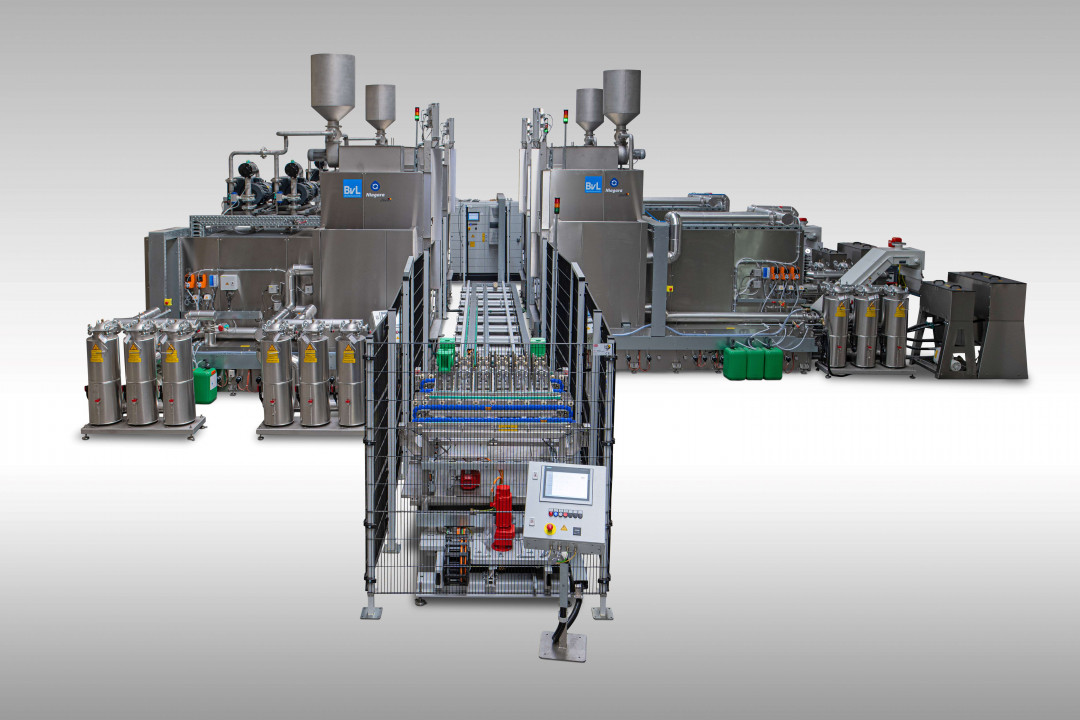
When cleaning components for industrial applications, the technological requirements placed on the cleaning system are often complex. The cleaning system described here features a particularly high level of efficiency and productivity. Gearbox housings of different heights are cleaned in an impressively short cycle time.
The automated BvL cleaning system NiagaraDFS features a four-chamber system, which works in conjunction with an efficient shuttle transport system and enables a high throughput of 14 batches per hour.
This high throughput is a key advantage that significantly increases the efficiency and productivity of the cleaning processes.
A special feature of this cleaning system is the ability to clean gearbox housings of different heights in one chamber. Thanks to adjustable hold-down devices that automatically adjust to the respective batch height, the gearbox housings of different heights are securely fixed in place while rotating during the washing process. This system makes it possible to clean gearbox housings with height differences of up to 80 mm. The workpiece pallets are rotated during the washing process, ensuring that they are thoroughly cleaned from all sides. A renowned German gear motor manufacturer has already successfully implemented this cleaning concept from BvL Oberflächentechnik GmbH at a factory in China. The positive feedback and the good results confirm the efficiency of this cleaning technology.
Continuous, fully automated cleaning process
The cleaning process starts after loading, when the gearbox housings are transported to the cleaning chambers via an automatic shuttle system. The process includes pre-cleaning, passivation and drying, which are divided between two chambers. Doubling the system to four chambers in combination with the shuttle system enables high throughput and short cycle times. This allows the individual cleaning processes to run in parallel and the cleaning chambers are continuously loaded.
Complete data transparency and flexible operation
Optimum interface communication enables the cleaning system to be seamlessly integrated into the customer's driverless transport systems. Information is collected and evaluated on the cleaning system in order to provide real-time data to the user. An interface to the database server on the customer's network ensures complete transparency and forms an ideal basis for reliable production analyses. At BvL Oberflächentechnik, automation and software programming experts are on hand to ensure that customer-specific requirements for IT interfaces and databases are fulfilled without any problems. This includes seamless integration with upstream and downstream systems as well as higher-level IT systems.
Thanks to a modern remote maintenance system, rapid error diagnosis and troubleshooting can be carried out online. Both software updates and changes can be easily implemented at the customer's site.
Flexible operation of the cleaning system at different locations is made possible by three stationary control consoles and two mobile control panels. This provides the system operator with quick-access and convenient control of the cleaning process.
Smart Cleaning technology for predictive maintenance
Thanks to the innovative Smart Cleaning concept, one of the features offered by the BvL cleaning technology is a bag filter usage forecast. This function visualises the current contamination status of the filter bag and provides information about when the filter needs to be changed. This allows maintenance work and the stocking of spare parts to be planned and carried out efficiently.
The Libelle Fluid Control used measures the level of contamination of the cleaning fluid via a sensor. This process control enables the system operator to respond to changes in bath contamination and ensure constant cleanliness of components.
To reduce heat loss, system components such as pipes, filters and tank covers are insulated. This saves energy costs and conserves energy resources.
BvL Oberflächentechnik enables system designers to create cleaning processes that are more efficient, more thorough and require less time. The combination of state-of-the-art technology, intelligent design and optimal interface communication offers a reliable and innovative solution for a wide range of cleaning requirements.
Come and visit BvL Oberflächentechnik at the EMO trade fair in Hanover from 18 to 23 September 2023. The BvL team will provide advice on all aspects of cleaning systems for reliable technical cleanliness, and will personally address any customer-specific requirements. Exhibition stand: Hall 11, Stand A 32.