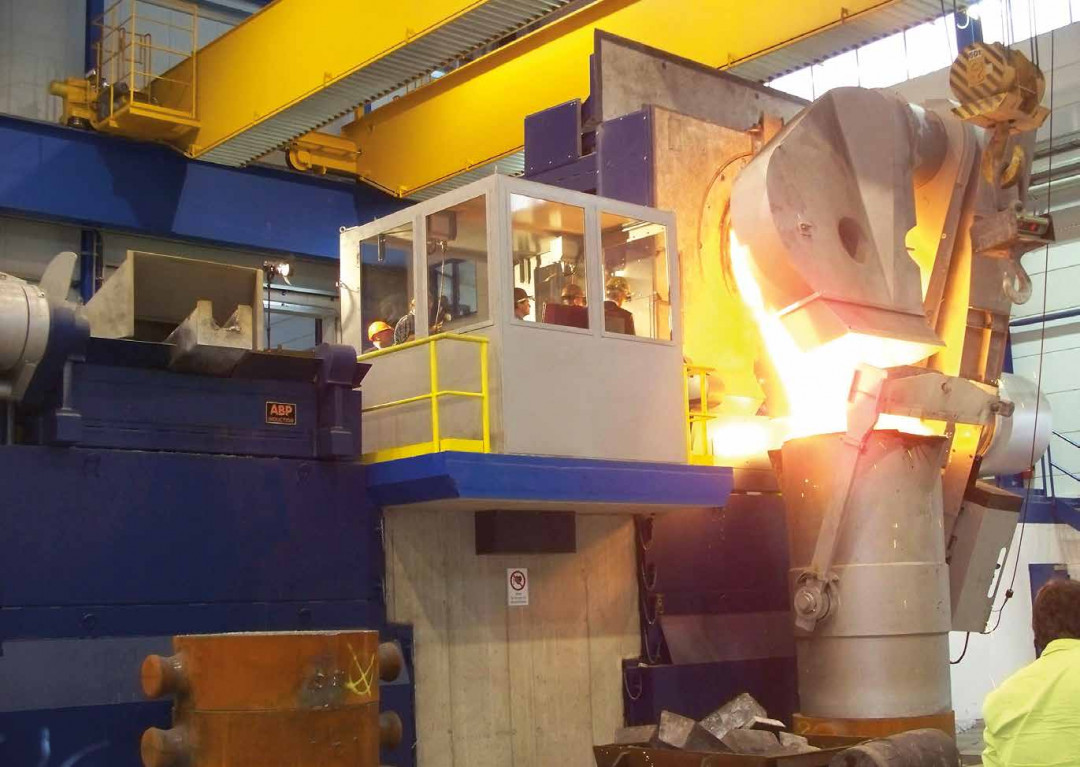
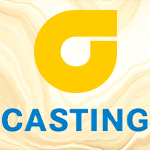
The metalworking industry is one of the biggest industrial producers of CO2 emissions worldwide. An alternative solution for reducing CO2 is induction for heating processes using green electricity. ABP Induction Systems GmbH is now going one step further and also using the technology to store energy.
BY MARCO RISCHE
The induction heating process is dynamic, easily controllable and almost CO2-neutral when using green electricity. Due to the direct energy input into the material, it is a good supplement or even a replacement for heating using previously established, CO2-intensive energy sources. Developing the concept further leads directly to the current discussion on the use of energy storage systems. ABP takes the energy storage system a step further and relates it to induction furnace technology. When implemented, this leads to a measurable reduction in CO2 emissions in the process and to optimum utilisation of available energy resources on the electricity market.
On the road to climate neutrality with all-electric heating
The major geopolitical and social upheavals in recent years have placed a heavy burden on the metalworking industry as an energy price-sensitive and comparatively climate-damaging industry. Even though the industry is dependent on further developments in these areas and, in many cases, on political decisions, it can also take action itself to noticeably avoid price sensitivity on the energy market and the production of climate-damaging CO2: Decarbonisation is the keyword that ABP Induction has been using here since GIFA 2023. ABP has recognised the paradigm shift towards CO2 neutrality and has embraced this through its "Your Partner on the way to Zero Emission" campaign.
ABP sees great potential in replacing fossil fuels with modern induction furnace technology to achieve ecological, economic and technical independence in order to meet the demand for decarbonisation. In this way, users can make a significant contribution to achieving the decarbonisation targets. If the metalworking industry embarks on the path to fundamental change, several premises must be taken into account when making the switch. It is about:
- implement a reduction in CO2 emissions to achieve the climate targets,
- ensure that the production of castings is maintained at internationally competitive prices,
- achieve a flexibilisation of the product range to increase competitiveness.
Naturally, the industry faces certain challenges in the transition. For many traditional, established companies, the core issue is initially the metallurgical changeover from cupola furnace iron to induction furnace iron. The focus is also on the aforementioned costs of electrical energy compared to conventional energy sources. Planning and costs for the new investment should also be taken into account. Ultimately, the players are dealing with a changed material flow and space requirements for the changeover.
Several energy market policy factors play a role in the energy requirements of the metalworking industry. The focus is on the price, but also on the energy mix and finally on the time at which the electrical energy is utilised. All three factors are related to the framework conditions of the energy market, in particular the electricity market for industrial use. On the supply side, it must always be ensured that as much energy is made available as is consumed. This has to do with the fact that load peaks must also be covered in the off-take, meaning that corresponding capacities or reserves are mandatory. The amount of off-take fluctuates depending on the time of day and night, although this is not specific to the metalworking industry, but to the market as a whole. Options for compensating for potential undersupply scenarios from Germany's own electricity generation can be electricity imports, or the storage of surplus energy at off-peak times and feeding it back at peak times, or in the case of fluctuating renewable generation. This is because it is subject to different geographical, topographical and climatic conditions.
Contribution of renewable energies to gross final energy consumption in Germany
As renewable generation is becoming increasingly important, it is also becoming a component to be taken into account in energy consumption planning. According to current estimates by the Federal Environment Agency [1], 22% of Germany's gross final energy consumption was covered by renewable energies in 2023 in accordance with the calculation rules of the EU Renewable Energy Directive (Figure 1).
![© STATISTA [2] © STATISTA [2]](/storage/media_foundry/images/4785/conversions/b1-full.jpg)
This corresponds to an increase of 1.4 % compared to the previous year. In 2020, Germany exceeded its target of 18% in accordance with the EU Directive and achieved a share of 19.1%. Further growth in renewable energies will be necessary in order to achieve the EU's new, ambitious climate targets. The wind energy sector in particular offers potential. Other sectors such as biomass, on the other hand, appear to have reached their maximum potential.
With regard to the industrial use of electricity for metal processing and other industries, the share of renewable energy in the electricity sector has risen significantly from 41.5% in 2021 to 46.0% in 2022. In 2022, a total of 254.2 billion kWh of electricity was generated from renewable energy sources, which corresponds to over 17 billion kWh more than in the previous year (+7%) [3]. A look at the consumption side shows In 2023, a total of 513 billion kWh was used from renewable energy sources. Around 53 % of this energy volume came from renewable energy sources for electricity production (Fig. 2).
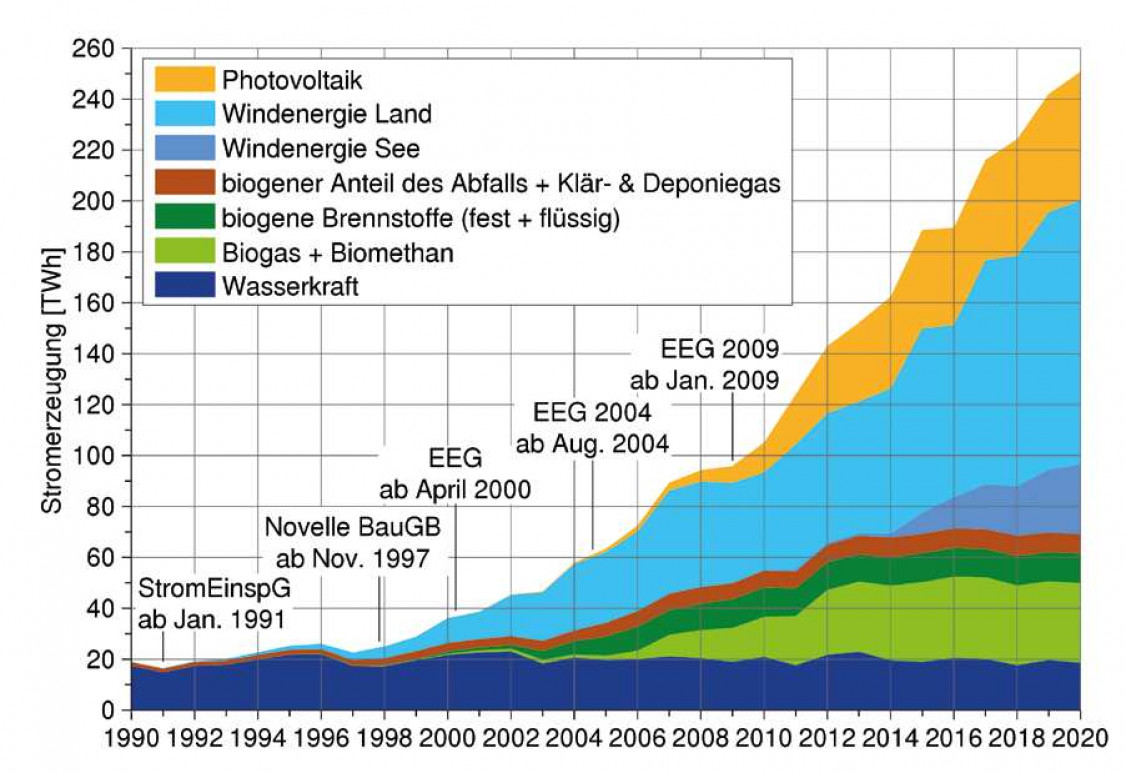
Biomass is the most important player in the spectrum of renewable energy sources due to its diverse uses in all sectors. It is used in the form of solid fuels for heating, biofuels for transport or biogas for electricity generation and accounts for almost 50 % of the supply of renewable final energy. Wind energy follows in second place with a share of 28 %. The use of solar energy in photovoltaic and solar thermal systems contributes a further 14 %. Hydropower and geothermal energy each account for a further 8 %. Spatial distributions and special features must be taken into account here. The time of day and season also play a relevant role [4].
The increasing use of renewable energies means that fossil fuels are being displaced and climate-damaging greenhouse gases can be avoided. According to the Federal Environment Agency, renewable energies could save around 250 million tonnes of CO2 equivalents in 2023 [4]. The largest share is accounted for by electricity generation from renewable sources (195 million tonnes of CO2 equivalents, i.e. around 78% of the total). In the heating sector, almost 18% of greenhouse gas emissions were avoided, which corresponds to 44 million tonnes of CO2 equivalent. Biofuels have a share of around 4%, which corresponds to around 10 million tonnes of CO2 equivalents.
Calculations by the Federal Environment Agency show that renewable energies are replacing hard coal and natural gas in the German energy mix. The use of renewable energies leads to savings in heating oil and natural gas in the heating supply sector. In the transport sector, diesel and petrol in particular are being replaced by renewable energies.
Stationary energy storage for peak load capping
Companies often have strongly fluctuating electricity consumption, which depends on the time of day and season (Fig. 3).
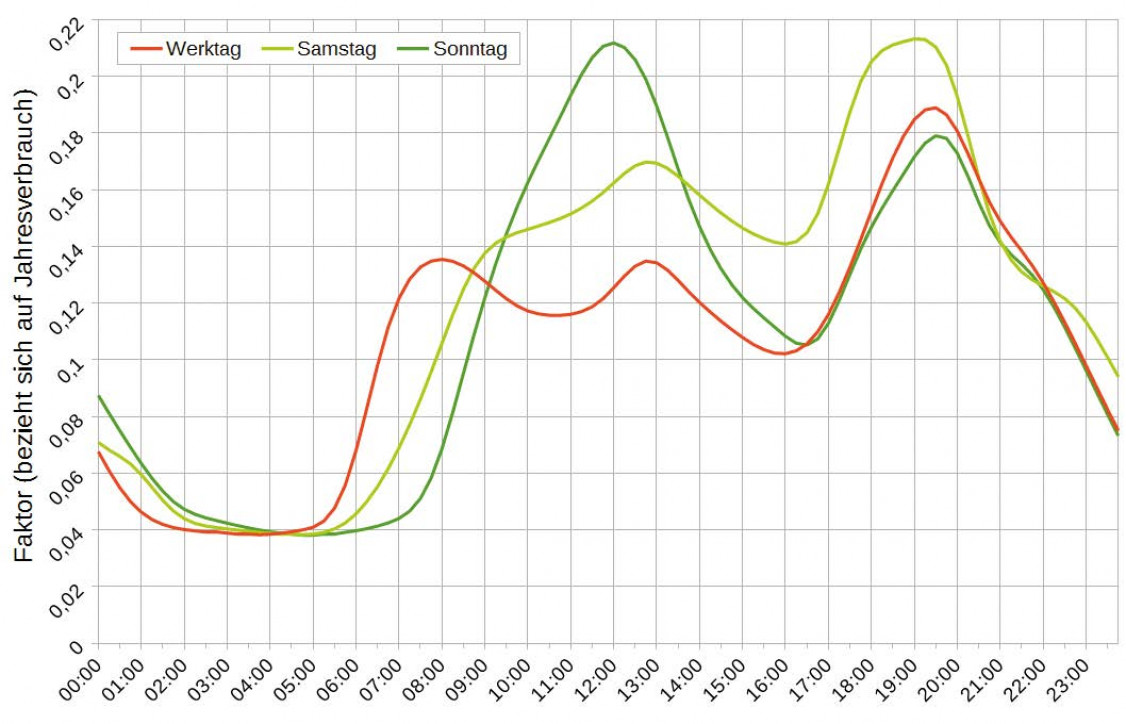
If, for example, several machines are started up at the same time, a higher amount of electricity is required. This maximum load on the electricity grid is usually referred to as "peak load" or "peak load". The consumption of energy is therefore anything but constant. In companies, so-called load peaks occur at certain times. These peaks are reflected in the electricity bill, as electricity suppliers have to permanently reserve the power that is only called up for a short time. The next peak is difficult to plan for.
When calculating electricity costs for industrial companies, not only the energy costs purchased (labour price) are taken into account, but also the costs for load peaks that occur (power price). This significantly increases the electricity tariffs for companies, regardless of the frequency or duration of the peak loads. The calculation of grid charges by the energy supplier also depends on the load peaks. A reduction in peak loads leads directly to cost savings for the company. There are two basic ways to avoid peak loads: Companies can start machines with a time delay or switch off production facilities. However, this represents a serious intervention in often sensitive production processes.
Another way to reduce energy costs is to avoid peak loads by using energy storage systems that act as an energy supplier when the company's electricity consumption is particularly high. This method adapts perfectly to individual workflows and does not interfere with sensitive production processes. This can be achieved, for example, through physical peak shaving (LSK) or peak shaving with registered load profile (RLM). In both cases, the power consumption of systems and machines is controlled in such a way that the energy required during peak loads is drawn directly from the storage system and not from the grid. This can be realised via a battery storage system or - and this is a unique feature for the metalworking industry - via a liquid iron storage system in the process.
The liquid iron storage system as a game changer in energy storage
A molten iron storage system can be the basis for an innovative production strategy to replace fossil fuels. This enables a transformation of the foundry towards the production of environmentally friendly castings at competitive costs. Various influencing factors must be taken into account in order to ensure agile production planning. One core element is the use of a fast, inductive melting system [6] (Fig. 4).
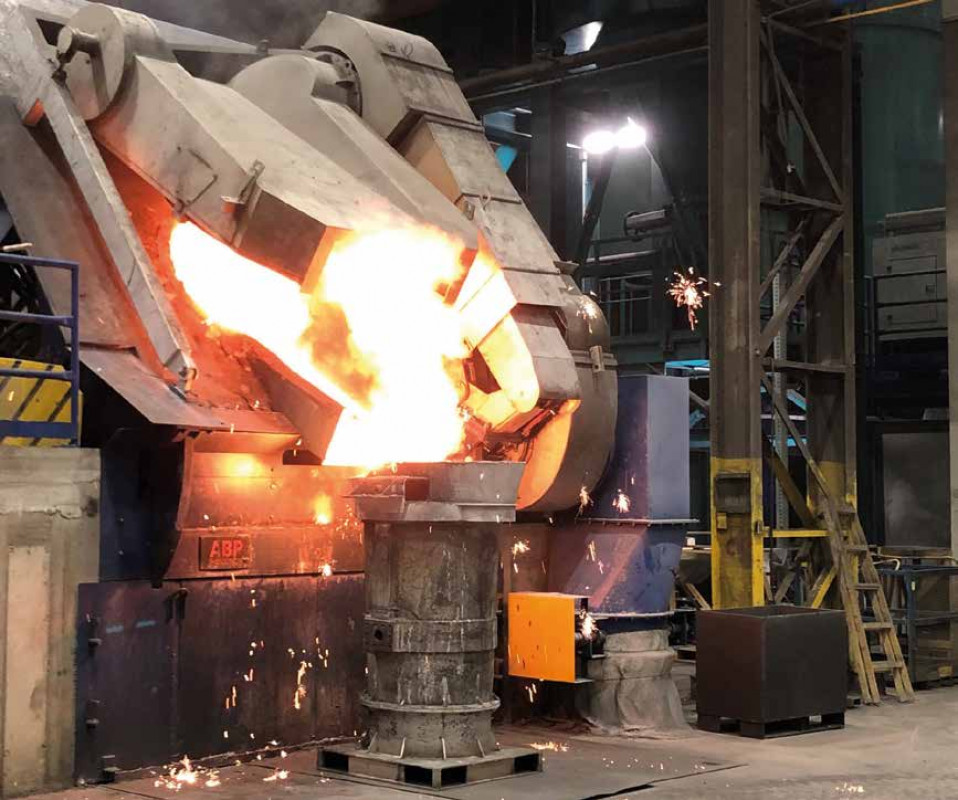
This requires flexible production planning with customised personnel deployment. The aim is to use only 100% green electricity, which is procured at favourable prices through a proactive purchasing strategy. The dynamic predictions of the generation forecasts are taken into account. Another factor is the creation of energy storage options in order to utilise off-peak periods.
A liquid iron storage system offers fundamental advantages here, as the energy is stored in a state that allows direct further processing. This is particularly interesting for foundries that are currently still relying on cupola furnace technology, which is being phased out, and are considering switching to induction furnace technology. However, there is also potential for optimising existing foundries that already rely on induction. It's all about flexibility in the process: the aim is to balance out fluctuations in energy utilisation against varying energy costs. This requires storage options. ABP Induction has developed appropriate tools for simulation and optimisation and is also focusing on the digitalisation of processes in the foundry in order to enable sustainable, economical and effective action. These tools are briefly presented below. The focus is on the Meltshop Designer and OptiCharge solutions.
Heating via induction as a principle
As just mentioned, the starting point for using a liquid iron storage system to store energy is inductive heating using electrical energy in conjunction with green electricity. The heat required for the process is transferred directly into the molten material. The process is effective and also climate-neutral when green energy is used. ABP can plan the entire process chain, including the replacement of the conventionally heated cupola furnace, and work with the customer to switch to electrically powered induction furnace technology. The ABP path is completed by digital tools that bring transparency to the process and thus control options for synchronising the available energy flow with the material flow. The aim is to optimise energy use while maximising production output.
When foundries consider making the switch in order to utilise the potential, there are two challenges to consider:
- Firstly, it means switching from continuous supply to discontinuous operation, i.e. batch operation.
- The second challenge is scrap quality. In cupola furnace melting operations, it is not uncommon for poor scrap quality to be used. Induction furnace operation cannot cope with this because the coupling is then significantly worse. Achieving a utilisation rate of 100 % is therefore much more difficult or even impossible. Utilisation rates of 60 % are more likely. Keeping this gap as small as possible depends on how the electromagnetic field couples to the scrap. This depends on the scrap quality and the parameters of the electrical energy supply.
Planning the system with the Meltshop Designer If you want to utilise the advantages of induction furnace technology and convert the system from cupola furnace to induction, for example, careful planning is essential. Especially when it comes to using the liquid iron storage tank as an energy store and integrating it into the process. The entire process can be planned in advance. ABP has developed the Meltshop Designer (Fig. 5) to design, dimension and plan a melting plant perfectly in this respect.
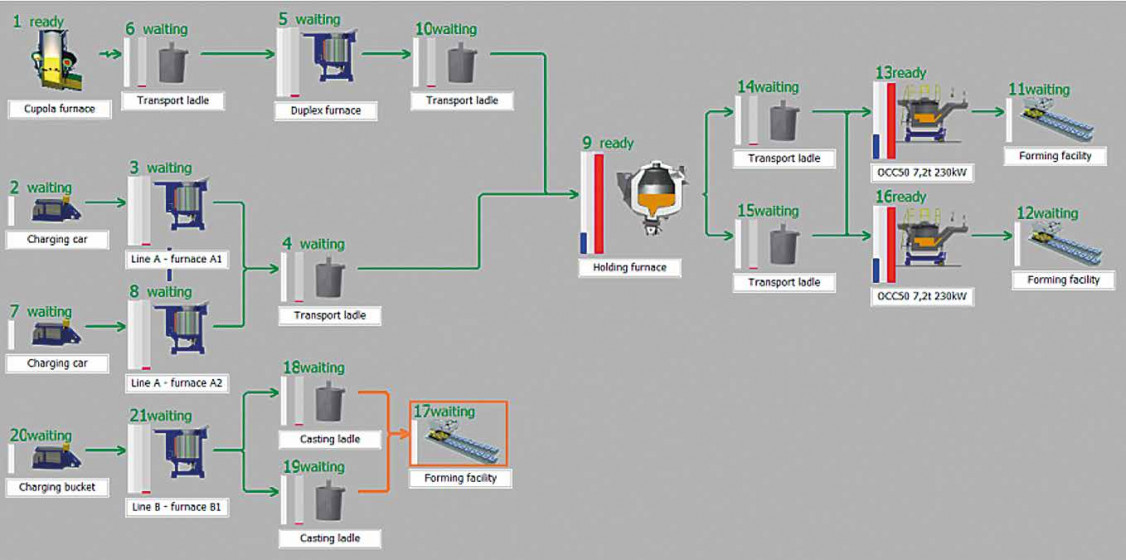
This ABP in-house development is used to determine which solution is the best when it comes to the material flow in the foundry. ABP experts can develop simulations for various foundry situations in close consultation with the customer's employees involved in the process, present alternatives for the furnace design and incorporate various configurations from the ladles to the filling of the moulding plant.
It is important to precisely allocate the data in order to establish a link to the achieved microstructure and mechanical parameters. The data obtained during this phase is used to define the target parameters for the new melting process in such a way that the core parameters of the melt remain stable or improve during the changeover in order to ensure the smoothest possible transition during further processing of the components. This phase should last around four weeks in order to record all metallurgical conditions. When the induction melting process is ramped up, it usually takes another four weeks until all aspects of the new process are correctly mapped.
OptiCharge: working in the constant power range
Further optimisations are possible during operation. Foundries can also start here to improve their own processes and maximise the potential of the molten iron storage system in terms of energy management and avoiding peak loads. Let's take a look at the coupling of the induction furnace, which is dependent on the load circuit: the power of the system is adjusted according to the charge of the input material based on its electrical and magnetic properties. Stationary losses due to recharging must therefore be optimised.
ABP makes it possible to measure and analyse these processes and to guide the customer during charging. The proprietary and patented OptiCharge tool (Fig. 6) is used for this purpose.
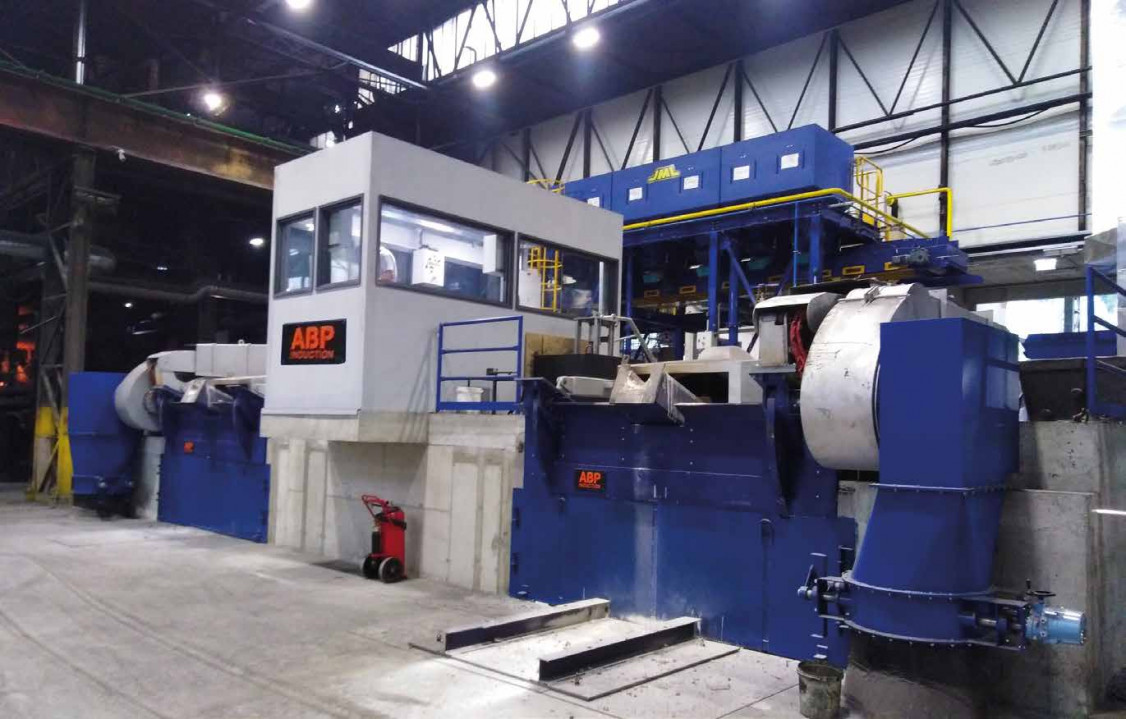
It measures the electrical parameters required to optimise performance. These parameters are mirrored against the current weight and the algorithm determines the lowest possible weight required to achieve full power consumption. The desired result is controlled charging to optimise the adjustment of the weight to the power consumption over the entire batch duration. Whenever the physical conditions allow, recharging is possible. This cold material couples optimally due to its ferromagnetic properties until it loses these properties when the Curie temperature is reached. The technical furnace parameters for this are recorded via the digital inverter control and converted into recommendations for action via the OptiCharge system. When a batch is started up with a partial filling of ferromagnetic melting material, small portions of this material are automatically refilled. As a result, measurable energy savings and production increases are realised in daily production operations compared to uncontrolled charging.
Conclusion
Decarbonisation is forcing future technology in melting operations to switch from cupola furnaces to induction furnace technology as CO2 prices rise. The supply of green electrical energy must be guaranteed at competitive world market prices in the long term. The metalworking industry has a special opportunity here: it has the potential to utilise liquid iron as an energy storage medium in order to use energy peaks. This factor can play a major role in economic efficiency after the changeover. At the same time, the market is changing towards smaller series, which is accelerating the process towards greater flexibility. ABP Induction has developed solutions here, with effective planning tools, suitable furnace sizes and corresponding transformation strategies. The metallurgical changeover is accompanied by the expertise of the ABP digitisation platform 'myABP2.0' with corresponding applications based on expert knowledge. The future is already here: there are already various reference projects for a successful changeover that can be scaled to practically all market and production conditions.
Practical example of a "successful transition"
In order to achieve the goals of decarbonisation, the transition of operations from fossil fuels to practically climate-neutral production is of great importance, as this article has shown. A detailed explanation of the metallurgical changeover as well as the advantages in operation and control using tools such as ABP OptiCharge and the ABP Meltshop Designer can be found in issue 10/2023 of Giesserei [7], where practical examples are used to show how a changeover can succeed.
Literature
[1] www.umweltbundesamt.de/themen/klima-energie/erneuerbare-energien/erneuerbare-energien-in-zahlen#ueberblickbeitrag-erneuerbare (retrieved 12/03/2024).
[2] www.de.statista.com/statistik/daten/studie/156695/umfrage/brutto-stromerzeugung-in-deutschland-nach-energietraegern-seit-2007/ (retrieved on 12/03/2024).
[3] www.energiewechsel.de/KAENEF/Navigation/DE/Energiewechsel/Erneuerbare-Energien/erneuerbare-energien (accessed 12/03/2024).
[4] www.umweltbundesamt.de/themen/erstmals-ueber-die-haelfte-des-stroms-in (accessed 12/03/2024).
[5] https://upload.wikimedia.org/wikipedia/commons/7/7a/Lastprofil_VDEW_H0_Winter.pngLastprofile show consumer behaviour (retrieved 12.03.2024).
[6] www.bundesregierung.de/breg-de/schwerpunkte/klimaschutz/faq-energiewende-2067498 (retrieved 12/03/2024).
[7] Foundry 110 (2023), [No. 10], pp. 30-37.