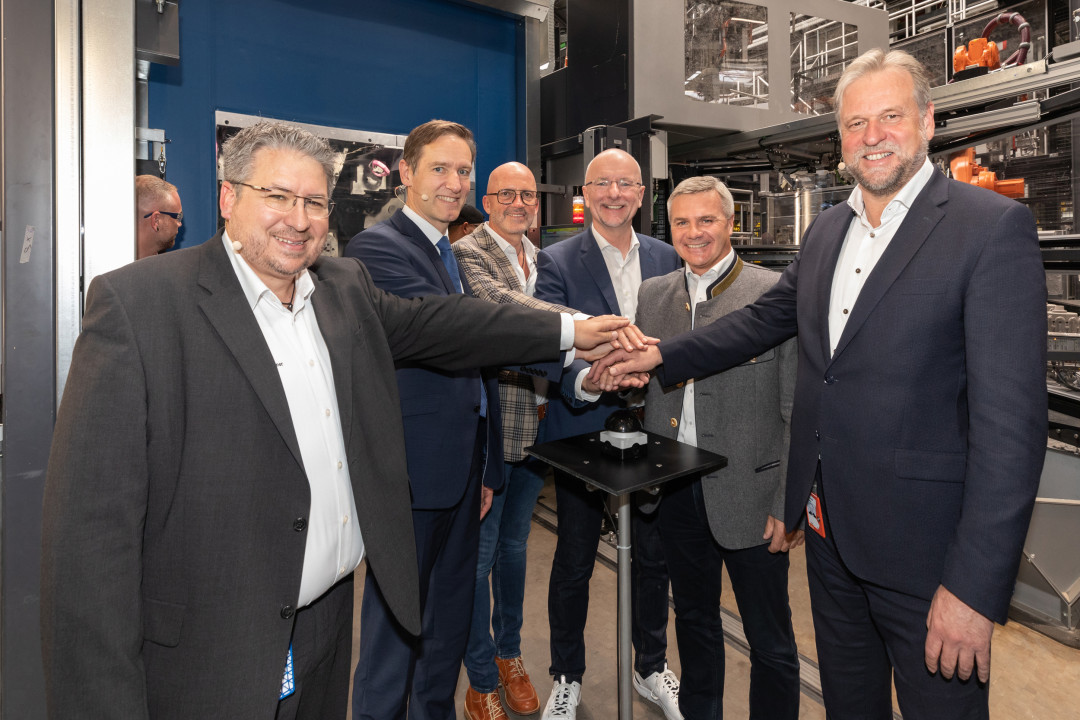
The light metal foundry at the BMW Group plant in Landshut is entering a new era. At the beginning of October, the official first casting of an aluminium housing for the highly integrated fifth-generation electric drive took place on an extensive expansion area.
In a few days, the innovative manufacturing area will start series production. This will increase the annual production capacity for the key cast component of the BMW Group e-drive system to up to 800,000 units per year. "This is a milestone for the Landshut light metal foundry and the Landshut plant," said site manager Dr Stefan Kasperowski.
The BMW Group is investing more than 200 million euros in the expansion of the Landshut light metal foundry. The focus is on expanding capacity for the production of the central housing for the highly integrated electric drive topology. The cast component, which is highly complex in terms of its contour and functional integration, combines the electric motor, transmission and inverter.
The new light metal foundry uses the so-called Injector Casting process. The innovative casting technology was designed and patented by process specialists at the Landshut light metal foundry and developed for highly industrialised series production. The high quality requirements and the complex geometry of the central housing called for a new casting technology that combines the advantages of a wide variety of casting processes. Injector casting guarantees a significantly finer microstructure and thus improved mechanical properties of the casting. In addition, it enables a reduced cycle time and, as a result, a significant reduction in energy consumption as well as lower CO2 emissions due to a lower casting temperature. The process is also characterised by reduced resource consumption, as less recycled material is required. This is because no additional sprue system is required due to the filling with the injector. The process thus saves up to 40 per cent of the melt.
As in all areas of the Landshut light metal foundry, only cores made of inorganic binder systems are used in the new systems, which are emission-free and environmentally friendly. This, too, is an innovation developed in Landshut.
In mid-November, the Landshut light metal foundry receives the renowned Automotive Lean Production Award in the "Component Supplier" category for its innovation of injector casting. Winners of this award are among the absolute "Champions League" in the automotive sector.
With the expansion of the Landshut light metal foundry, the location strengthens its importance for a successful transformation of the BMW Group towards e-mobility. In future, Landshut will supply the housings for all motor/transmission variants for fully electric vehicles of the fifth generation, up to 800,000 units per year. They are currently used in the fully electric BMW i4, BMW i5 and BMW i7 models as well as the BMW iX and BMW iX1. From 2025, the Landshut plant will also supply the next generation of all-electric vehicles, the New Class. Production of the e-drive combination will take place in the Competence Centre for E-Components at the Dingolfing plant.