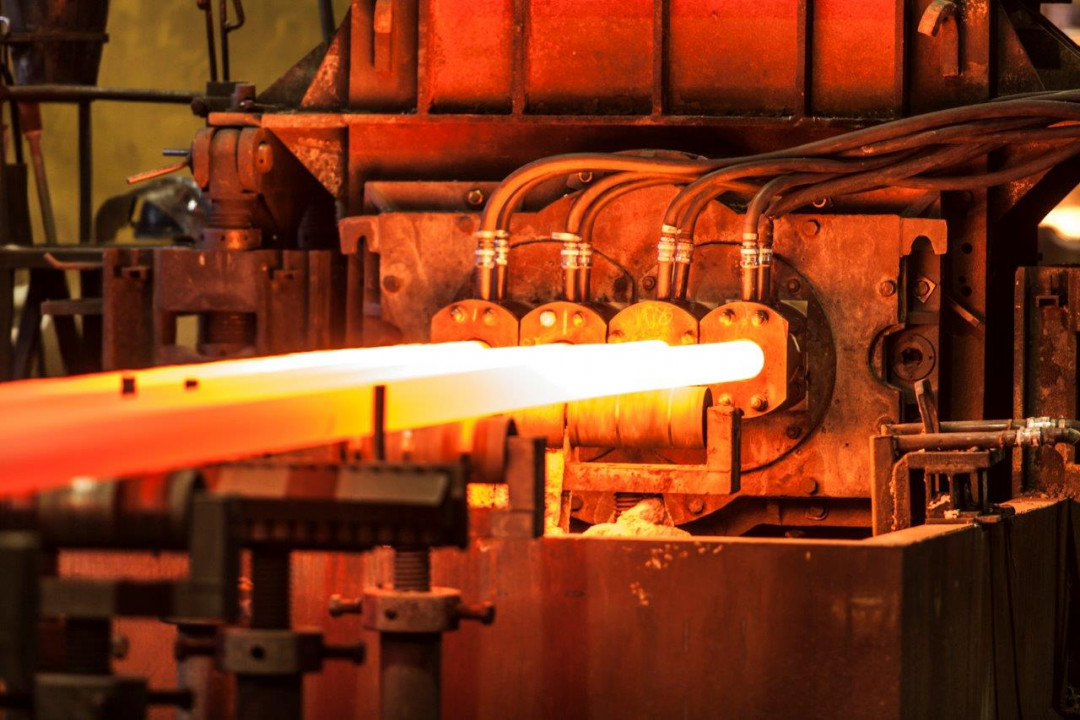
By using scientific models and artificial intelligence, a new PhD project will open the furnaces at the Danish iron foundry, TASSO, Odense.
What exactly happens when molten iron is cast has always been a mystery to the foundry industry, and the answer to this mystery may very well pave the way for the digital transformation of the entire industry. Since 2020, PhD student at the Technical University of Denmark, Ashish Chawla, has been connected to the Danish iron foundry, TASSO. Here, he is well underway writing his final PhD thesis, which will use advanced mathematical models and artificial intelligence to form the basis for digitizing TASSO's cast iron production.
The thesis is divided into three stages, of which the first stage has just been completed and the results published in a renowned academic journal on casting engineering. Through the development of an advanced science-based model, the first stage attempts to simulate what happens when the molten iron in TASSO's furnaces is cast into continuous cast iron. By looking into this process, it is possible to locate the optimal places to place sensors that will support the following digitization of the cast iron production.
Ashish Chawla explains that the next stages of his thesis are exploring how to digitize this process: “Scientific- and physics-based models that simulates the casting process will be integrated with state-of-the-art data analytics and AI models to achieve better control of the manufacturing process. This technology will form the basis for digitalization to optimize production processes in the form of streamlining workflows, robust production and reducing energy consumption, so there is also a sustainable aspect involved”.
CEO at TASSO, Kristian B. Pedersen, is very enthusiastic about the project and sees great potential in digitizing cast iron production – both for TASSO itself, but also for the foundry industry as a whole: “As the thesis is not finished yet, we do not know the results yet, but so far it looks promising. From TASSO's point of view, we have a goal of being able to produce an average of 420 tons of continuously cast iron per week, and a potential digitalization of our production may help us achieve this goal, he explains”. TASSO's electricity consumption reached 15 MWh last year, while the company emitted around 3,000 tons of CO2 within scope 1 and 2. The iron foundry has a strong focus on sustainability and Kristian B. Pedersen therefore hopes that increased digitization in the long term can help reduce energy consumption and thus the company’s climate footprint: “The casting production requires that the iron is heated up to around 1,400 degrees, and this obviously absorbs a large amount of energy. Therefore, even the smallest optimizations of the casting processes can lead to relatively large reductions in our climate footprint, and that makes digitization even more interesting for an iron foundry like us and the foundry industry in general”, he concludes.