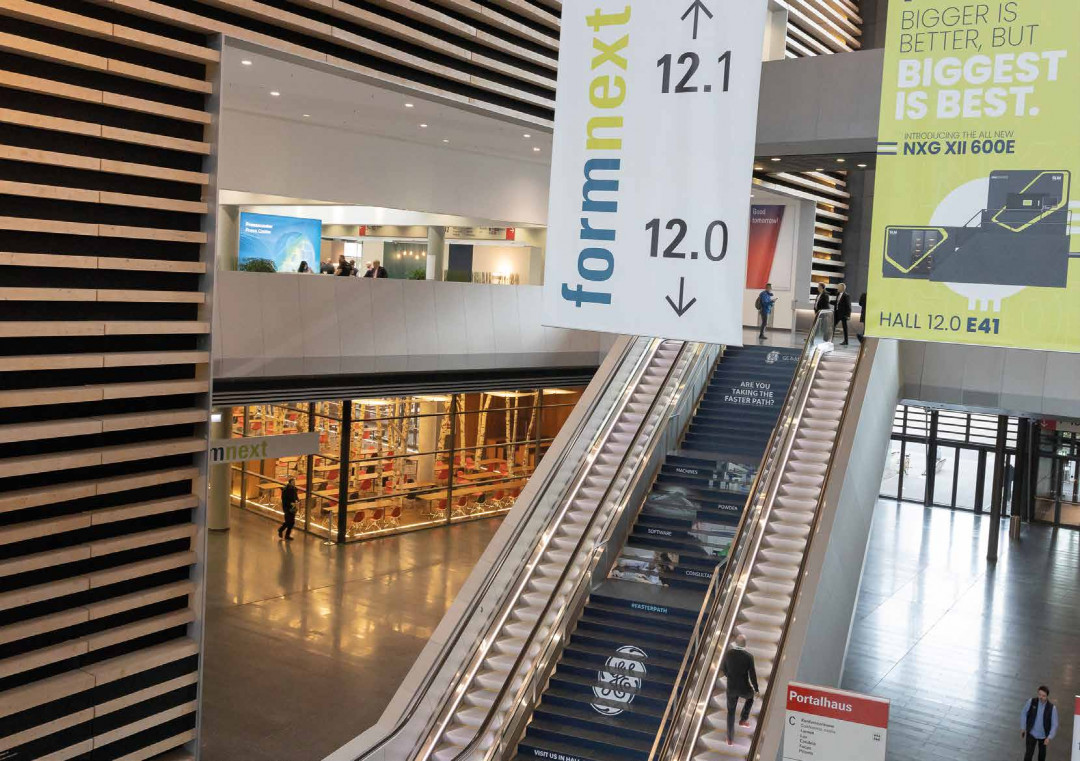
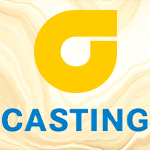
For four days, everything at Formnext 2022 in Frankfurt/Main revolved around the topic of Additive Manufacturing. Innovations from the areas of software, machines and materials were on display. The diverse application scenarios showed how fluid the transitions between different industries have become.
By Christian Thieme
For an industry with innovation cycles of only a few months, Formnext represents an important hub as an industry meeting point on the Frankfurt trade show floor. This was also clearly reflected in the increased exhibitor numbers after the trade show closed. With 802 companies – almost 200 exhibitors more than in the previous year – it is clear that the trade show has a high relevance in the industry. In addition to the number of exhibiting companies, the number of visitors again increased significantly. After all, 65.6 percent compared to 2021. “We are proud that we have again reached the impressive level of the pre-Corona era with Formnext,” said Sascha F. Wenzler, Vice President Formnext at organizer Mesago Messe Frankfurt GmbH.
Alex Kingsbury, Industry Consultant at Additive Economics, highlights the relevance of Additive Manufacturing (AM) to industrial production, adding, “If modern manufacturers want to become more flexible and responsive, they will inevitably have to embrace advanced and new technologies. AM is an innovative technology that, if used correctly, can increase manufacturing capacity enormously.” Not all of the technologies presented in Frankfurt are necessarily relevant to the foundry industry, but it is nevertheless evident that the sectors are becoming increasingly intertwined. New machines make components possible that are not feasible in the casting process. Special components made of different alloys can be realized in a single production step, and there is also a lot of movement in the area of printable alloys. Here, development is focused on the automotive and aerospace sectors.
AM goes digital
However, there is particularly great potential in the digital world. At a press conference, RWTH Aachen University presented the OVF (Open Vector Format) for the first time, a data format that could be used in all software solutions in the AM sector in the future and flank proprietary formats. Companies such as Dyndrite also made it clear that the process limitations in terms of speed and precision are often not to be found in the machines, but that the software plays an essential role. Faster data processing and software solutions that dynamically process and interleave workpiece parameters offer the potential to control machines even more precisely. With the appropriate software, it becomes possible to define each component segment with individual manufacturing parameters, which in turn has a positive effect on the structural design of the workpieces.
New alloys expand the range of applications
At the Trumpf booth, the company not only presented new AM machines, but also introduced CustAlloy from ECKA Granules, a new metal alloy that holds several advantages especially for automotive manufacturers. “With standard aluminum, automakers have reached their limits, especially in terms of the combination of strength and elongation. This is where CustAlloy helps,” says Jan Christian Schauer, materials expert for Additive Manufacturing at Trumpf. This aluminum alloy has very good mechanical properties; it does not break or crack as quickly. This makes crash-relevant applications possible. At the same time, CustAlloy is far less expensive to purchase than comparable high-end aluminum alloys, which achieve their properties with expensive alloying elements.
New tool steel with good corrosion resistance
Also to be found at Trumpf – the tool steel M789 AMPO. This is used primarily in tool and mold making. Users can use it to print components without preheating the powder. Because it is easy to process and at the same time very corrosion-resistant, users use the steel, for example, for the production of tools that are used in combination with more aggressive materials.
New developments at voxeljet
Dr. Ingo Ederer, CEO at Voxeljet, presented the BFP project that is being developed with GE at the booth. The company is currently working on the realization of large-format sand molds that will be used in the production of the GE Haliade X wind turbine. The project is currently still at an early stage, but Voxeljet would like to present the first results in the coming year.
Specifically, the project involves the production of sand molds with a diameter of up to 9.5 meters. Casting quality is expected to be significantly improved by the new process, particularly with regard to surface quality. A new print head will be developed for this application, and the handling concept in the foundry will also have to be adapted to the new possibilities.
Sand molds as a service
At Formnext, the Langenfeld-based company innoCast presented its new brand innoForm to the trade show audience for the first time. In the future, the company intends to supply foundries with finished sand molds. InnoCast uses various rapid prototyping processes. Here, either sand molds or melt-out models made of PMMA (thermoplastic material) are printed directly from 3D data.
SLM sets benchmarks
SLM Solutions, Lübeck, Germany, presented the world’s first solution for the production of metal components with a size of up to 3.0 x 1.2 x 1.2 meters at Formnext. The machine concept includes a core unit and a size-flexible build envelope that enables the production of components in individual dimensions. Sam O’Leary, CEO of SLM Solutions explains, “This is another technology that opens up new possibilities for AM applications by removing previously accepted geometric limitations.” The new solution makes it possible to additively manufacture large metal parts that were previously impossible to produce. At the same time, like all other SLM machines, it offers the full benefits of SLM technology, such as design freedom or the reduction of multiple components to a single one.
Combined know-how
For the first time, Desktop Metal united a company portfolio of nine companies on a European booth: “We reached a very international audience with very many new contacts. The stand visitors, including representatives from the oil and gas industry, OEMs from the automotive sector and foundries, were pre-informed and came to us with concrete projects and budgets. We closed deals for our sand, polymer and metal plants,” reports Guersel Demircali, Vice President EMEA Sales Channel, Desktop Metal. ExOne (Fig. 4) was also represented at the joint booth, where it exhibited its S-Max Flex. The printer offers a build envelope of 1900 x 1000 x 1000 mm and a build volume of 1900 l.
Extensive and varied supporting program
The supporting program of Formnext 2022 was more extensive than ever before, the organizer emphasizes. Recurring themes included the implementation of decentralized Additive Manufacturing, the promotion of sustainable manufacturing concepts, and the increased maturity of additive manufacturing in the industrial environment. The next Formnext will take place in Frankfurt/Main from Nov. 07 to 10, 2023.
You can also find the complete article in the CP+T issue 04/2022.