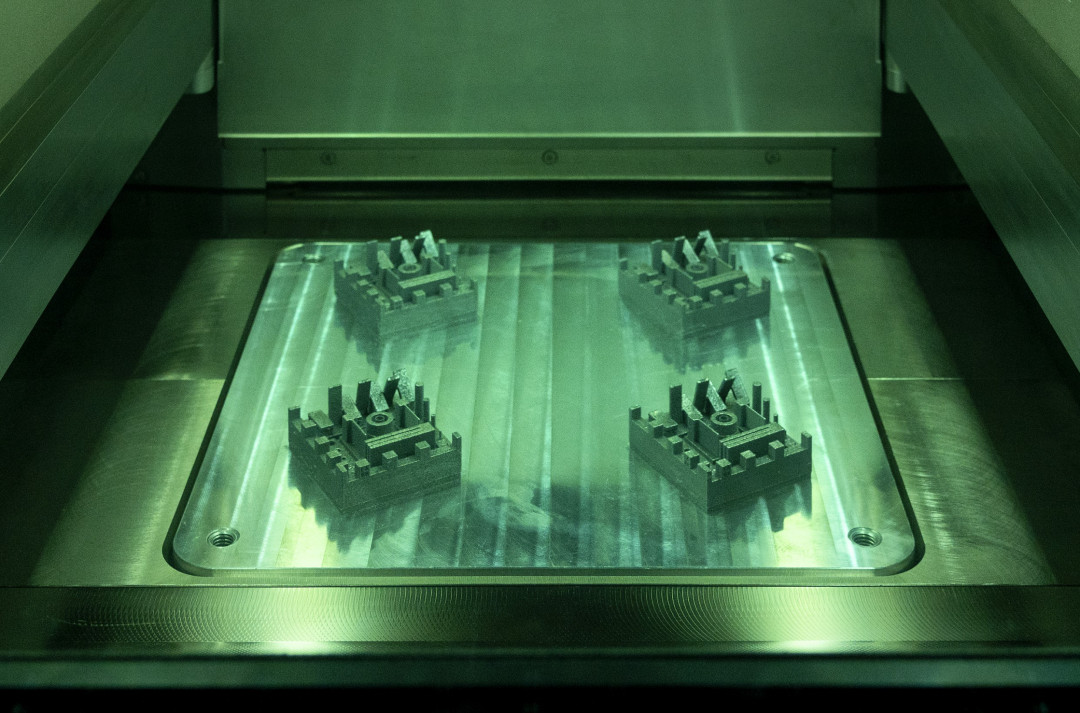
Additive manufacturing has made considerable progress in the production industry in recent years. Components can be created layer by layer, resulting in unique material properties. The Federal Institute for Materials Research and Testing (BAM) has now published reference data on additively manufactured materials made of titanium, nickel and a stainless steel for the first time. This data can be used to ensure the quality and safety of components and drive forward material development in 3D printing.
The safety of materials is particularly important in the aerospace and medical technology sectors, as faulty components can have serious consequences. The unique microstructures created by additive manufacturing influence the mechanical, thermal and chemical properties of a component, such as its strength or corrosion resistance. "In order to minimise potential risks and ensure the quality of 3D-printed components, reliable reference data is essential," says Prof. Birgit Skrotzki, materials scientist at BAM. "Our reference data on the elastic properties of additively manufactured metals represents an important contribution that not only ensures the quality and safety of these components, but also enables innovations in material development."
The team led by scientists Dr Birgit Rehmer and Prof Birgit Skrotzki from the Department of Materials Engineering and the Competence Centre Additive Manufacturing at BAM characterised three metal alloys using the Dynamic Resonance Method (DRM). This involved exciting the material with a periodic mechanical impulse and measuring the resulting resonance frequencies. They discovered, for example, that 3D-printed components exhibit significant differences in their elastic properties depending on the direction of construction and the direction in which the samples are removed.
The directional dependency, which occurs at all the temperatures investigated, has an impact on use in specific applications such as turbine blades. This must be taken into account when designing components where the direction of loading plays a role. The parameters of the additive manufacturing process also influence the properties. A thinner powder layer thickness, for example, results in higher elastic characteristic values for stainless steel.
The extensive data sets contain information on the manufacturing processes and parameters, heat treatments, grain size, sample dimensions and weight together with their measurement uncertainties. They can be used by designers, testing laboratories and researchers to evaluate the performance of additively manufactured materials, perform quality tests and improve simulations. The reference data is now available via the Zenodo open data platform.