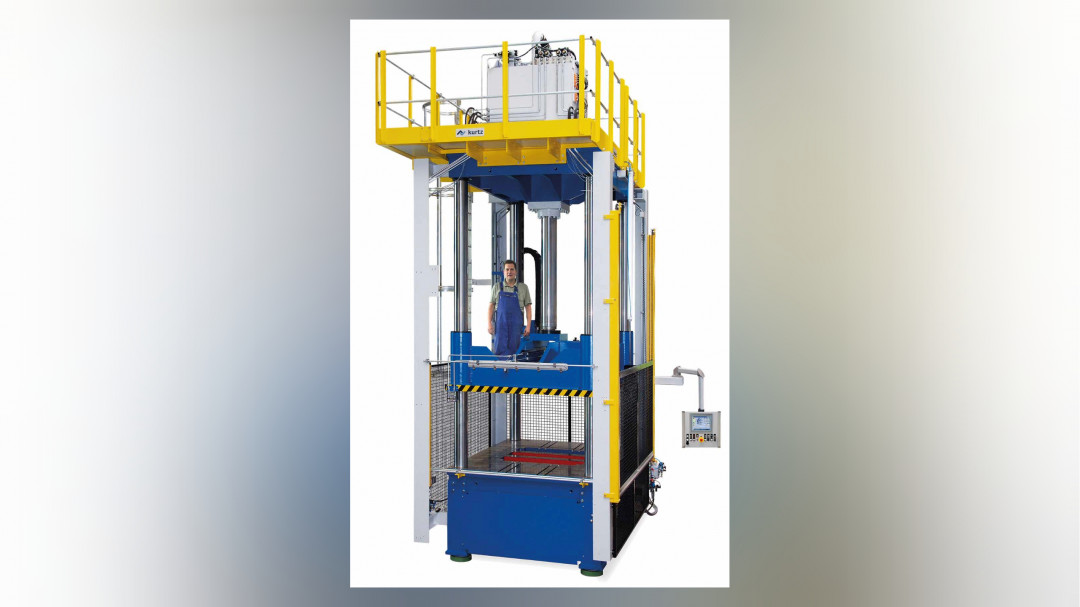
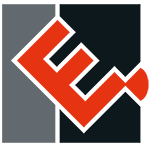
While the removal of filters, sprue and overflows with deburring presses was a "must" for previous die-cast parts, GIGA castings were not initially deburred using the tried and tested technology. Both the cast parts and the necessary tools and presses were considered too large and not economically feasible. Now you could say: "And yet it works"!
Previously, Kurtz deburring presses worked in die casting cells with a clamping force of up to 6000 tonnes. Kurtz received its first enquiries about deburring GIGA castings with GIGA presses from Asia. Initially, the deburring of castings produced on die casting machines with a clamping force of up to 9000 tonnes was discussed. There are numerous reasons why GIGA-Castings also relies on the proven technology - i.e. deburring directly in the die-casting cell. Concrete advantages: less logistical effort, shorter deburring process, shorter distances and therefore more favourable, efficient process flow analogous to existing automation processes from the previous die casting, cost-efficient thanks to reduced footprint and fewer downstream handling processes, simple and safe operation as well as quick findings regarding quality directly after the casting process.
The requirements for the GIGA presses were the same as before, apart from two challenges: the clamping surface - and therefore the size of the mould - and the weight. The necessary cutting force was available, as Kurtz had already built several presses with a punching or cutting force of 300 tonnes. For the clamping area, the specification was 4000 x 3000 mm and for the weight, the presses had to be able to hold tools of up to 25 tonnes.
Whereas structural parts were previously mostly deburred on sliding/tilting table presses, the "normal" 4-column press is the preferred choice for these dimensions. The advantage of such a press is that less space is required in the die-casting cell. However, more attention must be paid to the deburring process during mould construction.
Despite the size of the presses, they must not slow down. Development in die casting is known to be rapid, which means that the cycle times in the casting process are also reduced. The press must not slow down the casting process. If you deduct the loading and unloading time of the press using robots, there is not much time left for the deburring process itself. Fast presses are therefore necessary, comparable to the previous large presses from the Kurtz programme. In addition to the standard requirements for presses, sufficient slide connections should be available due to the more complex shape of the cast parts. Previous experience has shown that up to ten slides are required.
Kurtz benefits from its accumulated expertise in the construction of deburring presses and GIGA low-pressure casting machines in the design and construction of GIGA presses. In addition to fast and powerful hydraulics, the software is the linchpin. The mould protection developed by Kurtz has proven its worth and is used in GIGA presses. This is because damage and failure of large deburring tools are even more painful than is already the case with conventional tools. We are currently receiving enquiries for presses for installation next to die casting machines with a clamping force of up to 12,000 tonnes. The requested cutting force is 400 tonnes.
Kurtz GmbH & Co. KG
Frankenstraße 2
97892 Kreuzwertheim
www.kurtzersa.de
Hall 7A, Stand 650