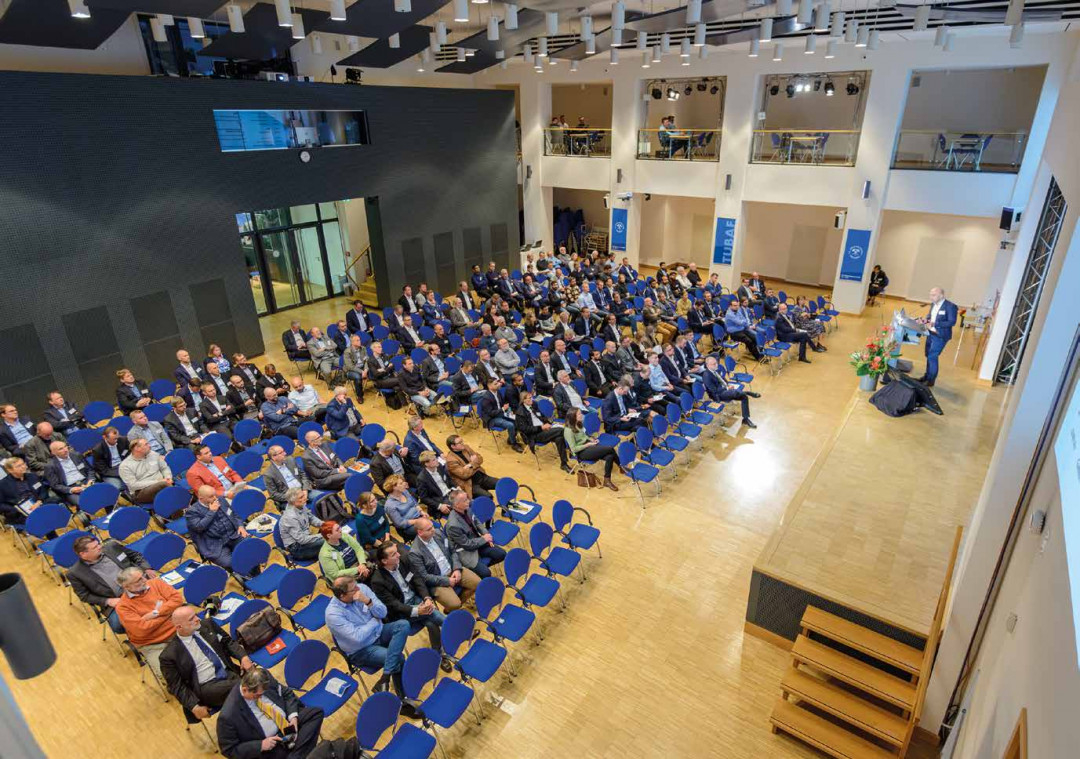
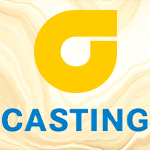
More than 250 participants accepted the invitation to Freiberg this year. In addition to new scientific findings and technical developments, the discussions also focussed on the enormous challenges facing the industry in terms of sustainability and energy supply.
BY MONIKA WIRTH
Institute Director Gotthart Wolf welcomed his guests with an overview of news from the Freiberg Foundry Institute. The sand recycling facility inaugurated last year is well utilised and a new hall is currently under construction, in which all activities related to CO2-free melting will take place from spring 2024; in particular, the new space will enable an upscaling of the research facilities. Wolf will retire at the end of next year and will be succeeded by Professor Michal Szucki, who currently holds a tenure-track professorship at the institute. Wolf expressed concern about the declining number of first-year students, although the English-language Master's programme is well attended. The institute has put together an advertising kit that can be requested by companies, for example for school days.
The future of the foundry industry
In his welcoming address, BDG President Clemens Küpper emphasised the important role of research in solving problems by applying its knowledge. He said it was the responsibility of politicians to utilise this potential and thus take responsibility with intelligence. He regretted that political decision-makers do not seek enough advice from technology institutes. The companies that mainly drive the economy in Germany, namely SMEs, are also rarely consulted. However, the campaigns organised in recent months, such as the joint day of action with IG Metall at the Baumgarte foundry, have made the industry more visible. He emphasised the importance of the association, which is the mouthpiece of the industry: "We are the key to the energy transition, we are doing good and we need to talk about it." Christiane Heunisch-Grotz also agreed with this, reporting on the customer day at the HEUNISCH GmbH foundry and posing the question: "Do people in Germany actually still want energy-intensive companies?" (see extra box).
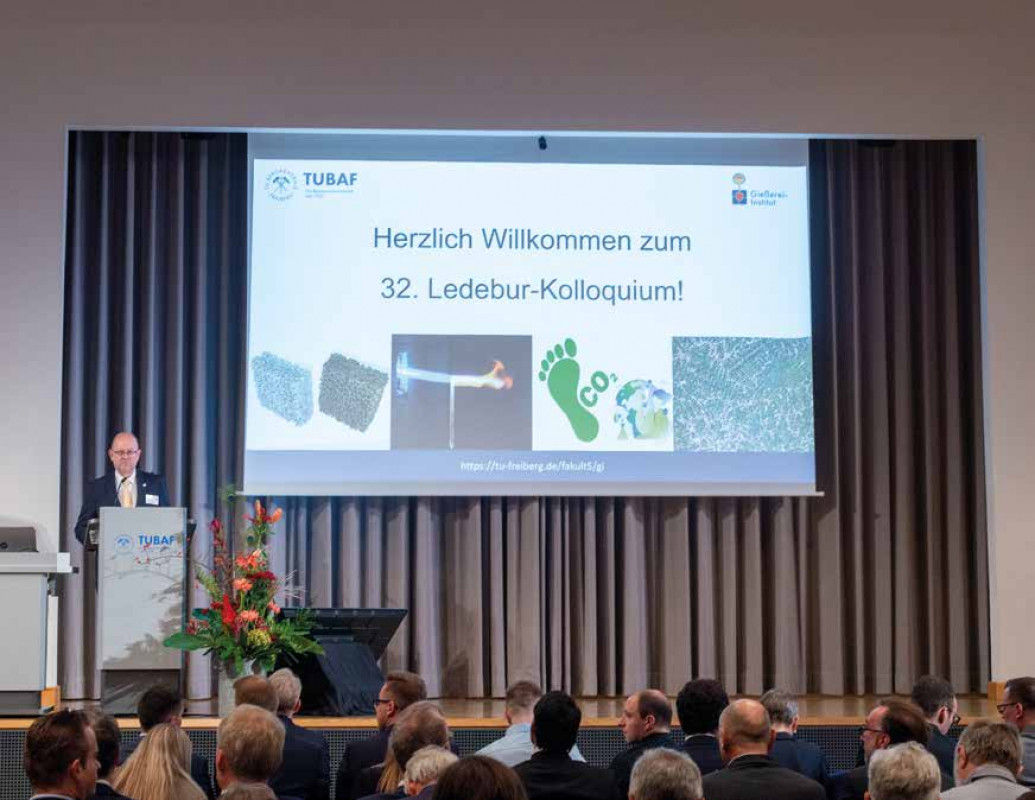
Cast iron research
Spheroidal graphite cast iron (GJS) has great technical potential and is used in many safety-relevant components, such as the rotor hubs of wind turbines. A largely defect-free microstructure is very important here. Wolfram Baer from the Federal Institute for Materials Research and Testing (BAM) demonstrated the dangers of degeneration of the graphite spheres in GJS into so-called chunky graphite, which reduces strength and ductility. Reliable non-destructive detection is currently still difficult, which is why fracture analyses using a scanning electron microscope are used. Christoph Bleicher presented various methods of assessing the reliability of cast iron components that are being developed at Fraunhofer LBF. The aim is to ensure sufficient component load-bearing capacity, even in the case of localised notches or discontinuities, and to achieve optimum lightweight construction and a minimum of rejects with the lowest possible safety coefficients. The creation of virtual limit samples and statistical validation are important components for assessing the transferability from the sample to the cast part. Torsten Moczigemba from the Saxon State Office for the Environment, Agriculture and Geology reported on a joint research project with the Freiberg Foundry Institute on odour nuisance and emissions in the area of iron foundries, which is intended to serve as a basis for approval procedures. This was followed by a lively discussion on various measures in practice. The advantages of the BREF, which provides guidelines for best practice, were listed.
Optimising processes
When using recycled material in cast iron smelting, steel scrap, which often contains boron, is also melted down. Cathrine Hartung, Elkem Silikon Products, spoke about the influence of boron on carbide and ferrite formation. When recycling aluminium scrap, it is primarily iron phases that impair the quality. Michal Szucki, designated successor to Institute Director Wolf, is researching how to remove these and thus increase the secondary content in alloys.
Cores and moulds are increasingly being additively manufactured. The engineers at Salewatec GbR asked themselves why not print models in sand instead of turning them from solid material. So far, good results have been achieved and the models are already suitable for small series production; there is still a need for optimisation in terms of through-hardening. There are plans to extend the application to other areas of modelling. Thoms Aschenbach, Krämer und Grebe GmbH & Co KG, explained the measures that can be taken to make moulds last longer during core production and thus conserve resources. The key to this is a 30% reduction in curing time and digital wear analyses. At the Foundry Institute of the Technical University of Munich, stresses in cast components are measured in situ using cast-in fibre-optic sensors. According to Wolfram Volk, this allows the stresses on a component, e.g. a cylinder head, to be recorded from solidification to failure. However, these sensors are also useful for basic research. For example, the solidification behaviour of an alloy can be examined in detail. To calibrate the sensors, doctoral student Constantin Braun was even able to carry out an experiment during a DFG parabolic flight under virtually weightless conditions.
From Freiberg research
The event concluded with research reports by Freiberg foundry technology doctoral students. Florian Mrugalla is investigating the grain refinement of steel to improve its corrosion, surface and mechanical properties. The late introduction of cerium appears promising. Lukas Mastaler is working on technologies for CO2-free melting: with the Ultra High Temperature (UHT) Thermo-Jet, a hot gas flow, currently adjustable from 20 to 1200 °C, is generated using an electrically inductively heated system. The idea is to simply replace the burner in the existing hearth melting furnaces and not have to replace the entire furnace. Mengmeng Zhang is researching a precise photometric method for determining the bentonite content in green sand regenerates. The best results were obtained by sparingly dosing the contrast agent methylene blue. Inspired by railway technology, Eric Schramm is developing lightweight brake discs made of particle-reinforced aluminium alloys for the automotive sector, particularly for e-mobility. The tilting mould process is used to ensure rapid and homogeneous cooling of the melt.
A thought-provoking guest appearance
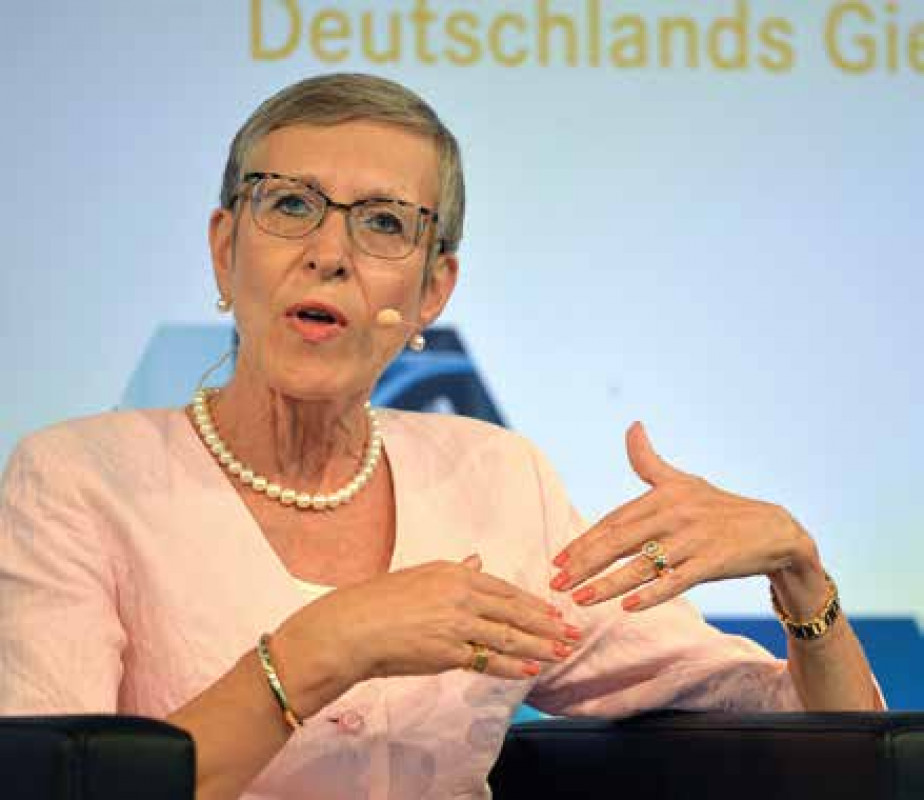
Do we actually still want energy-intensive companies in Germany? This is currently the crucial question for Christiane Heunisch-Grotz. And for the Managing Director of Gießerei Heunisch GmbH, it was also the topic of her appearance in Freiberg - given the political framework conditions. Heunisch-Grotz had also taken this meta-topic into the customer day that the foundry had organised at the Bad Windsheim site, which included BDG speaker Christian Schimansky, who shared his expertise on the subject of energy.
In Freiberg, Heunisch-Grotz recalled important facts: Although the foundry industry only accounts for 1% of value creation in Germany, its products are used in 99% of manufacturing machinery, including renewable power generation plants. Do we really want to do without them? Obviously yes, the entrepreneur surmises - at least that's how she feels in view of the enormous economic and ecological challenges and, above all, political demands. Once you've done one thing, the next comes along, says the Managing Director. Of course, Heunisch takes the issue of sustainability extremely seriously and was the first foundry in Germany to publish a sustainability report. However, the requirements for this are so extensive that it requires additional personnel capacity. The company is also working on implementing the Supply Chain Act.
A new landfill site for used sand was recently opened after years of planning and authorisation procedures. This not only seemed like a big investment financially, but also in terms of stress. The official complexity often seemed to exceed the technical complexity. The enormous bureaucracy behind every law in Germany now seems to be an obstacle to the innovative strength and productivity of German SMEs. If you believe Heunisch-Grotz, it also takes a lot of idealism to keep going despite this.
The company's biggest concern is competitiveness. The German government's climate strategy expects a move away from fossil fuels in favour of green electricity. As far as this is technically possible for the processes in an iron foundry, the company would of course like to fulfil this requirement, but the German electricity price is the second most expensive in the world. How are you supposed to produce competitively? If politicians only make demands without providing support, it is either stupid or one can only assume that they are no longer wanted. Nevertheless, Heunisch refuses to give up and wants to be part of the transformation.